The core of a mold is a critical component that shapes the interior or non-cosmetic side of the part being produced. It is typically located on one side of the mold and often houses the ejector system, which helps remove the finished part from the mold. In simpler molds, the core works alongside the cavity, which forms the outer shape of the part. Together, these components ensure the accurate and consistent production of molded parts by defining the internal and external geometries.
Key Points Explained:
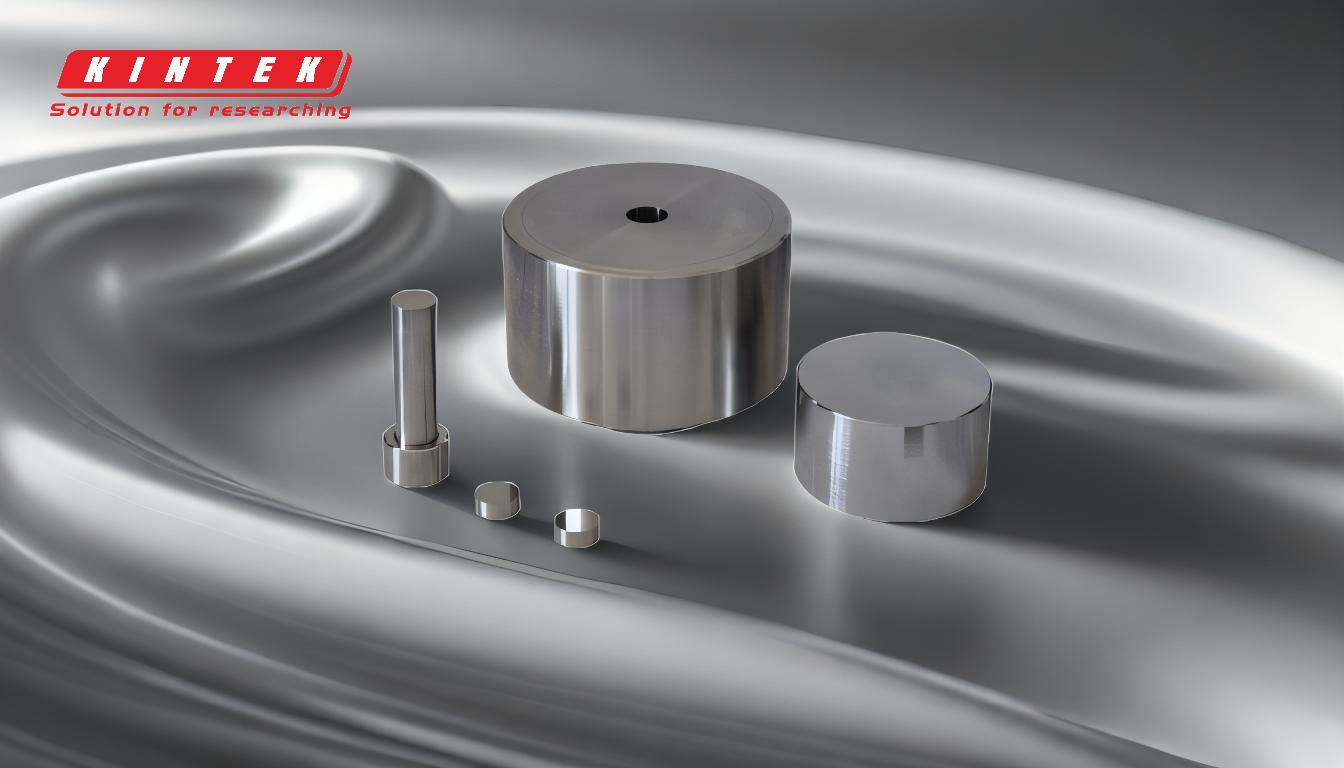
-
Definition of the Core:
- The core is the part of the mold responsible for shaping the interior or non-cosmetic side of the finished product. For example, in a cup mold, the core forms the inside of the cup.
- It is essential for defining the internal features of the part, such as holes, recesses, or intricate details.
-
Location and Function:
- The core is typically located on one side of the mold, opposite the cavity, which shapes the exterior of the part.
- It often houses the ejector system, which is crucial for releasing the finished part from the mold after the molding process is complete.
-
Relationship with the Cavity:
- In a simple mold, the core and cavity work together to form the complete shape of the part. The cavity defines the outer surface, while the core defines the inner surface.
- This dual-component system ensures precision and consistency in the final product.
-
Ejector System Integration:
- The core is where the ejector system is usually integrated. This system uses pins or plates to push the finished part out of the mold once it has solidified.
- Proper integration of the ejector system is vital to avoid damage to the part during ejection.
-
Importance in Mold Design:
- The core is a fundamental part of mold design, as it directly impacts the quality and functionality of the molded part.
- Designers must carefully consider the core's geometry, material, and cooling channels to ensure efficient production and high-quality results.
-
Applications in Manufacturing:
- Cores are used in various manufacturing processes, including injection molding, blow molding, and compression molding.
- They are essential for producing parts with complex internal structures, such as automotive components, consumer goods, and medical devices.
By understanding the core's role and its integration with other mold components, manufacturers can optimize their molding processes and produce high-quality parts consistently.
Summary Table:
Aspect | Details |
---|---|
Definition | Shapes the interior or non-cosmetic side of the part. |
Location | Typically on one side of the mold, opposite the cavity. |
Function | Houses the ejector system for part removal. |
Relationship with Cavity | Core defines internal features; cavity defines external features. |
Ejector System | Uses pins or plates to push the finished part out of the mold. |
Importance in Design | Critical for part quality, geometry, and cooling efficiency. |
Applications | Used in injection, blow, and compression molding for complex parts. |
Optimize your molding process with expert insights—contact us today for tailored solutions!