Ball mills and SAG (Semi-Autogenous Grinding) mills are both used in the mining industry for grinding and pulverizing ore, but they differ significantly in their design, operation, and applications. Ball mills use steel balls as grinding media and are suitable for fine grinding, while SAG mills use a combination of ore and a small amount of steel balls, making them ideal for coarse grinding. SAG mills are larger, more energy-efficient, and often used in the initial stages of grinding, whereas ball mills are smaller and used for secondary grinding. The choice between the two depends on the ore characteristics, desired grind size, and operational efficiency.
Key Points Explained:
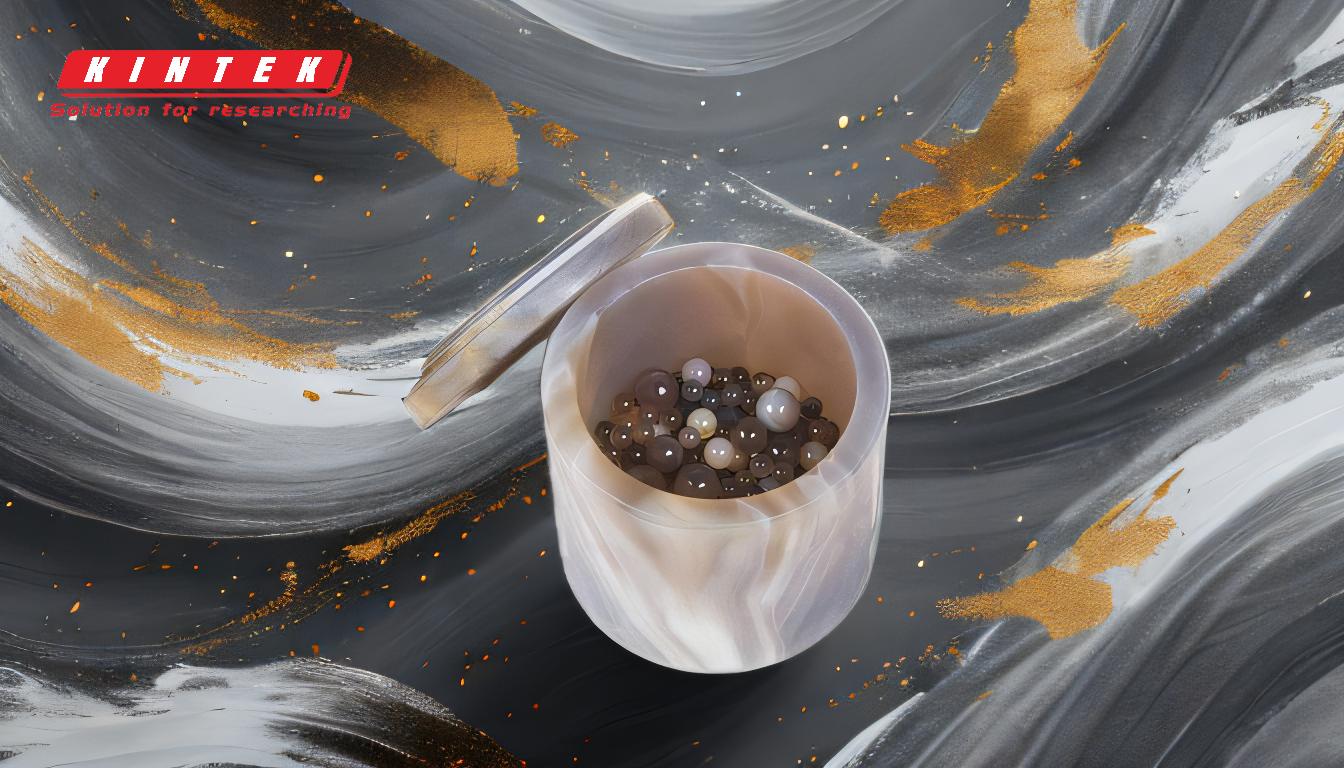
-
Design and Structure:
- Ball Mill: Consists of a rotating cylindrical shell filled with steel balls as grinding media. The ore is fed into the cylinder, and as it rotates, the balls cascade and grind the material.
- SAG Mill: Combines the use of ore itself as grinding media along with a small percentage of steel balls. It has a larger diameter and shorter length compared to ball mills, allowing for a coarser grind.
-
Grinding Mechanism:
- Ball Mill: Relies on the impact and attrition of steel balls to grind the ore. The balls are lifted by the rotation of the mill and then fall back, crushing the material.
- SAG Mill: Utilizes both the ore and steel balls for grinding. The larger size of the mill allows for the ore to be crushed by its own weight and the impact of the steel balls.
-
Applications:
- Ball Mill: Typically used for secondary grinding after the ore has been initially crushed. It is suitable for producing fine and ultra-fine particles.
- SAG Mill: Often used in the primary grinding stage, especially for hard and abrasive ores. It is capable of handling larger feed sizes and produces a coarser product.
-
Energy Efficiency:
- Ball Mill: Generally less energy-efficient compared to SAG mills, especially for coarse grinding. The energy consumption increases with the fineness of the grind.
- SAG Mill: More energy-efficient for coarse grinding due to the larger size and the use of ore as part of the grinding media. It reduces the need for additional crushing stages.
-
Operational Considerations:
- Ball Mill: Requires regular maintenance due to the wear and tear of the steel balls and liners. The smaller size makes it easier to handle and install.
- SAG Mill: Larger and more complex, requiring more sophisticated control systems. However, it can handle larger volumes of ore, reducing the number of mills needed.
-
Cost Implications:
- Ball Mill: Lower initial cost and simpler operation, but higher operational costs due to energy consumption and maintenance.
- SAG Mill: Higher initial investment but lower operational costs over time due to energy efficiency and reduced need for secondary grinding.
-
Ore Characteristics:
- Ball Mill: Best suited for ores that require fine grinding and where the feed size is relatively small.
- SAG Mill: Ideal for ores that are hard and abrasive, and where the feed size is large. It can handle a wide range of ore types and sizes.
In summary, the choice between a ball mill and a SAG mill depends on the specific requirements of the grinding process, including the type of ore, desired grind size, and overall operational efficiency. Both mills have their unique advantages and are often used in combination to achieve the desired grinding results.
Summary Table:
Aspect | Ball Mill | SAG Mill |
---|---|---|
Design | Rotating cylindrical shell with steel balls | Larger diameter, shorter length; uses ore and steel balls |
Grinding Mechanism | Impact and attrition of steel balls | Crushing by ore weight and steel ball impact |
Applications | Secondary grinding, fine and ultra-fine particles | Primary grinding, coarse grinding for hard and abrasive ores |
Energy Efficiency | Less efficient for coarse grinding | More efficient for coarse grinding |
Operational Costs | Lower initial cost, higher maintenance and energy costs | Higher initial cost, lower operational costs over time |
Ore Characteristics | Best for fine grinding, small feed sizes | Ideal for hard, abrasive ores and large feed sizes |
Need help choosing the right mill for your grinding process? Contact our experts today!