Wet and dry vacuum pumps differ primarily in their lubrication and sealing mechanisms. Wet vacuum pumps use oil or water for lubrication and sealing, which helps reduce friction and wear between moving parts. In contrast, dry vacuum pumps operate without any fluid in the space between rotating mechanisms or static parts, relying on tight tolerances and advanced materials to function effectively. Wet pumps are generally more robust and suitable for heavy-duty applications, while dry pumps are preferred in environments where contamination from oils or fluids must be avoided, such as in cleanrooms or semiconductor manufacturing.
Key Points Explained:
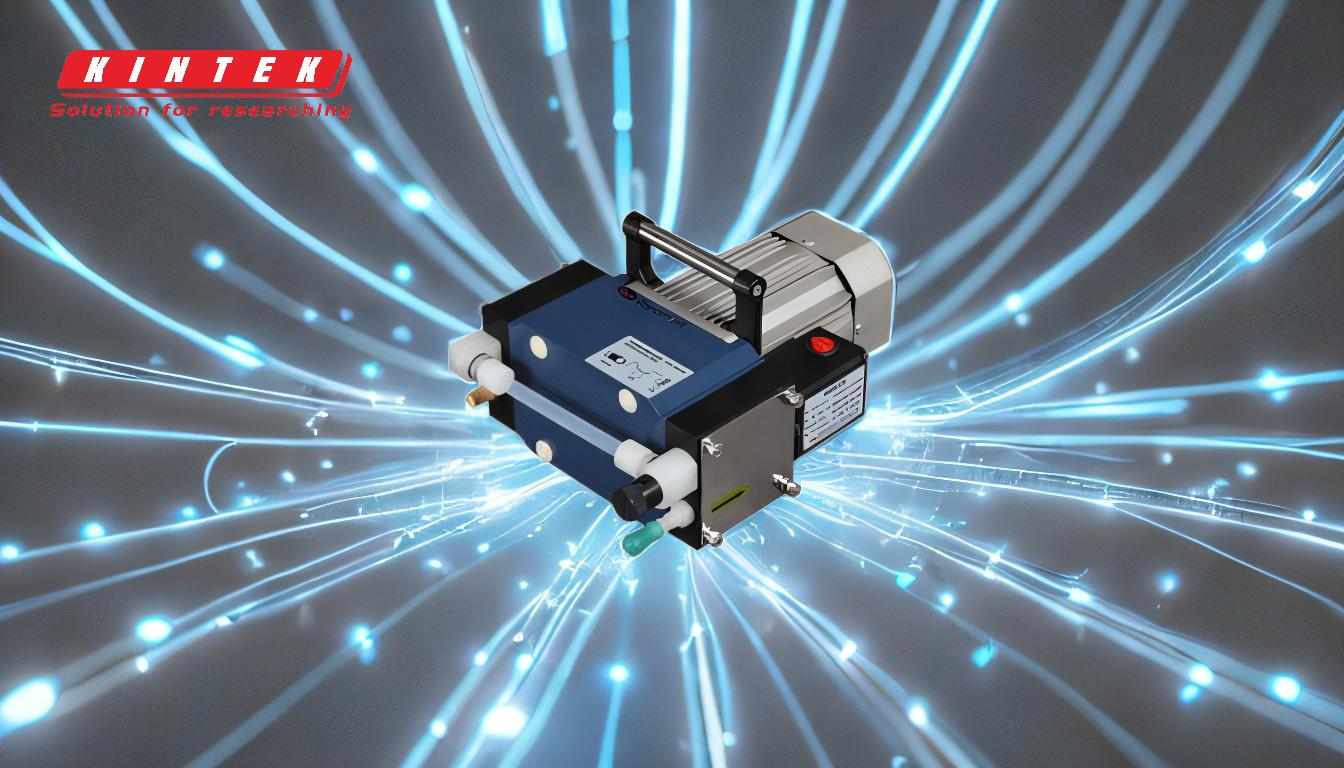
-
Lubrication and Sealing Mechanisms:
- Wet Vacuum Pumps: These pumps use oil or water as a lubricant and sealing medium. The fluid reduces friction between moving parts, ensuring smooth operation and extending the pump's lifespan. The fluid also helps to seal gaps, preventing gas leakage and maintaining vacuum integrity.
- Dry Vacuum Pumps: These pumps operate without any fluid in the working chamber. Instead, they rely on precise engineering, tight tolerances, and advanced materials to minimize friction and wear. This design eliminates the risk of fluid contamination, making them ideal for sensitive applications.
-
Applications and Suitability:
- Wet Vacuum Pumps: Due to their robust design and the use of lubricants, wet vacuum pumps are well-suited for heavy-duty industrial applications where high vacuum levels and continuous operation are required. They are commonly used in industries such as chemical processing, food packaging, and pharmaceuticals.
- Dry Vacuum Pumps: Dry pumps are preferred in environments where contamination from oils or fluids is a concern. They are widely used in cleanrooms, semiconductor manufacturing, and other high-precision industries. Dry pumps are also easier to maintain since they do not require regular fluid changes or disposal.
-
Maintenance and Operational Considerations:
- Wet Vacuum Pumps: These pumps require regular maintenance, including oil or water changes, to ensure optimal performance. The used fluid must be disposed of properly, which can add to operational costs and environmental considerations.
- Dry Vacuum Pumps: Maintenance is generally simpler and less frequent, as there is no need to manage or replace fluids. However, the precision engineering required for dry pumps can make them more expensive initially and more sensitive to improper handling.
-
Performance and Efficiency:
- Wet Vacuum Pumps: The presence of a lubricating fluid can enhance the pump's performance by reducing internal friction and heat generation. This can lead to higher efficiency and the ability to achieve deeper vacuum levels.
- Dry Vacuum Pumps: While dry pumps may not achieve the same vacuum levels as wet pumps, they offer cleaner operation and are less likely to introduce contaminants into the system. Advances in materials and design have significantly improved the performance of dry pumps, making them competitive in many applications.
-
Environmental and Safety Considerations:
- Wet Vacuum Pumps: The use of oil or water can pose environmental and safety risks, particularly in terms of fluid disposal and potential leaks. Proper handling and disposal of used fluids are essential to mitigate these risks.
- Dry Vacuum Pumps: Dry pumps are generally considered more environmentally friendly and safer, as they do not involve the use of hazardous fluids. This makes them a preferred choice in industries with strict environmental regulations.
-
Cost Implications:
- Wet Vacuum Pumps: While the initial cost of wet pumps may be lower, the ongoing maintenance and fluid disposal costs can add up over time. Additionally, the need for regular maintenance can result in more downtime.
- Dry Vacuum Pumps: The initial investment in dry pumps is typically higher due to the precision engineering required. However, the lower maintenance costs and reduced downtime can make them more cost-effective in the long run, especially in applications where contamination is a critical concern.
In summary, the choice between wet and dry vacuum pumps depends on the specific requirements of the application, including the need for lubrication, contamination control, maintenance, and cost considerations. Wet pumps are ideal for heavy-duty applications where robust performance is needed, while dry pumps are better suited for high-precision environments where cleanliness and minimal maintenance are priorities.
Summary Table:
Aspect | Wet Vacuum Pumps | Dry Vacuum Pumps |
---|---|---|
Lubrication | Use oil or water for lubrication and sealing. | Operate without fluids, relying on tight tolerances and advanced materials. |
Applications | Ideal for heavy-duty industrial applications (e.g., chemical, food, pharmaceuticals). | Preferred in cleanrooms, semiconductor manufacturing, and high-precision industries. |
Maintenance | Requires regular fluid changes and proper disposal. | Minimal maintenance; no fluid management needed. |
Performance | Higher efficiency and deeper vacuum levels due to lubrication. | Cleaner operation with reduced contamination risks. |
Environmental Impact | Potential risks from fluid disposal and leaks. | Environmentally friendly; no hazardous fluids involved. |
Cost | Lower initial cost but higher maintenance and disposal expenses. | Higher initial cost but lower long-term maintenance costs. |
Need help choosing the right vacuum pump for your application? Contact our experts today for personalized advice!