Wet vacuum pumps and dry vacuum pumps differ primarily in their use of lubrication and sealing mechanisms. Wet pumps rely on oil or water for lubrication and sealing, which helps in reducing friction and maintaining vacuum efficiency. Dry pumps, on the other hand, operate without any fluid in the pumping chamber, relying on tight mechanical tolerances and advanced materials to function effectively. Dry pumps are generally more versatile, easier to maintain, and resistant to corrosion, making them suitable for a wider range of applications. Wet pumps, while effective, may require more maintenance due to the presence of fluids.
Key Points Explained:
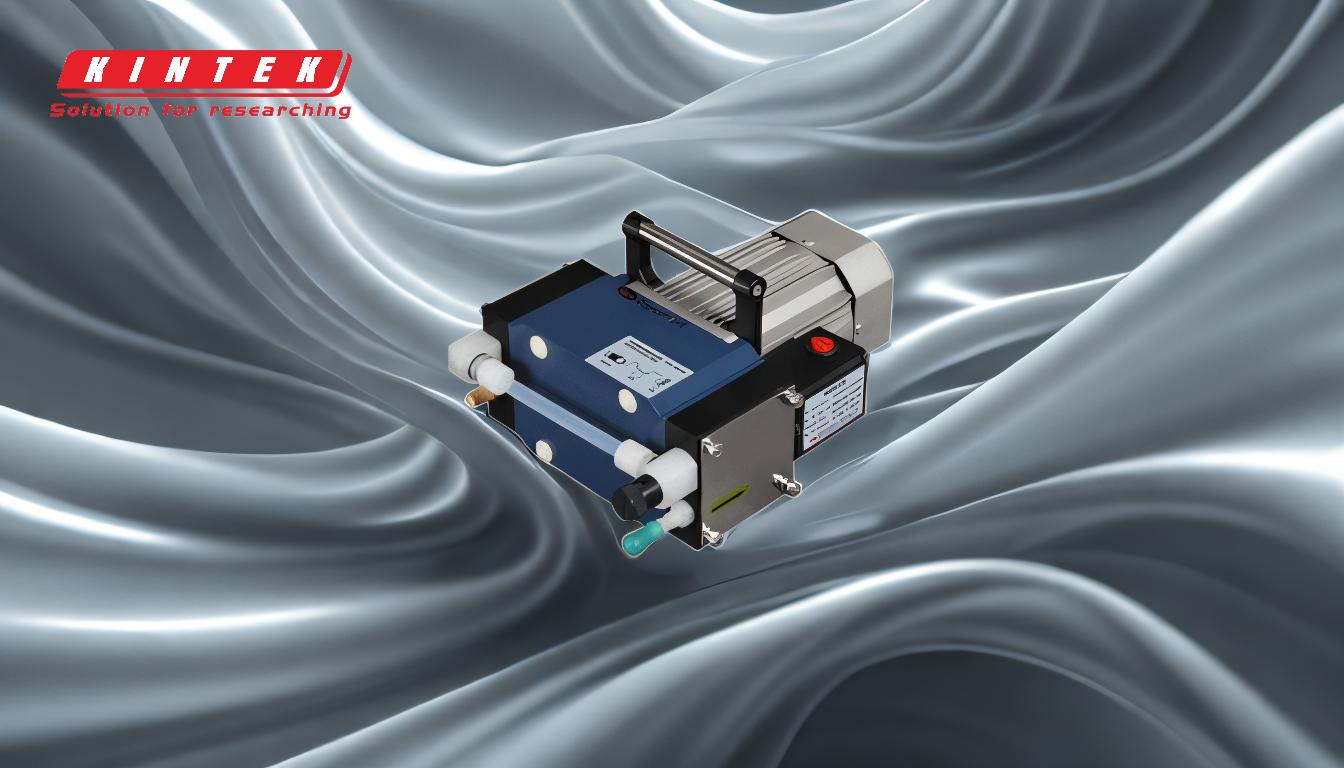
-
Lubrication and Sealing Mechanisms:
- Wet Vacuum Pumps: Use oil or water for lubrication and sealing. The fluid reduces friction between moving parts, ensuring smooth operation and maintaining vacuum efficiency. This design is particularly useful in applications where contamination from the lubricant is not a concern.
- Dry Vacuum Pumps: Operate without any fluid in the pumping chamber. They rely on tight mechanical tolerances and advanced materials to minimize friction and wear. This design is ideal for applications where contamination from lubricants must be avoided, such as in cleanroom environments or sensitive manufacturing processes.
-
Maintenance Requirements:
- Wet Vacuum Pumps: Require regular maintenance to replace or replenish the lubricating fluid. The presence of fluids can also lead to potential issues such as fluid contamination, leaks, or the need for fluid disposal, which can increase operational costs.
- Dry Vacuum Pumps: Generally require less maintenance since there is no fluid to replace or manage. The absence of fluids reduces the risk of leaks and contamination, making dry pumps more durable and cost-effective over time.
-
Versatility and Application:
- Wet Vacuum Pumps: Typically used in applications where the presence of a lubricating fluid is acceptable or even beneficial. Examples include certain industrial processes, laboratories, and environments where the pump's performance is not adversely affected by the fluid.
- Dry Vacuum Pumps: Highly versatile and can be used in a wide range of applications, including those requiring a clean, oil-free environment. They are easy to detach and reattach to different equipment, making them suitable for use in various industries such as semiconductor manufacturing, food processing, and pharmaceuticals.
-
Durability and Corrosion Resistance:
- Wet Vacuum Pumps: May be prone to corrosion over time due to the presence of fluids, especially if the fluid is not properly maintained or if the pump is exposed to harsh environments. This can lead to reduced lifespan and increased maintenance costs.
- Dry Vacuum Pumps: More durable and resistant to corrosion since they do not rely on fluids. The absence of fluids eliminates the risk of corrosion caused by fluid substances, leading to a longer operational life and reduced maintenance needs.
-
Operational Efficiency:
- Wet Vacuum Pumps: Can achieve high levels of vacuum efficiency due to the effective lubrication provided by the fluid. However, the efficiency may degrade over time if the fluid becomes contaminated or if maintenance is neglected.
- Dry Vacuum Pumps: Operate with very tight tolerances, which allows them to maintain high levels of efficiency without the need for lubrication. The absence of fluids also means there is no risk of efficiency loss due to fluid contamination or degradation.
In summary, the choice between wet and dry vacuum pumps depends on the specific requirements of the application, including the need for lubrication, maintenance considerations, and the potential for contamination. Wet pumps are suitable for environments where fluid lubrication is acceptable, while dry pumps offer advantages in terms of versatility, durability, and maintenance simplicity, making them ideal for clean and sensitive applications.
Summary Table:
Feature | Wet Vacuum Pumps | Dry Vacuum Pumps |
---|---|---|
Lubrication | Uses oil or water for lubrication and sealing. | Operates without fluids, relying on tight tolerances and advanced materials. |
Maintenance | Requires regular fluid replacement and maintenance. | Minimal maintenance due to no fluid use, reducing leaks and contamination risks. |
Versatility | Suitable for applications where fluid presence is acceptable. | Ideal for clean, oil-free environments like semiconductors, food, and pharma. |
Durability | Prone to corrosion if fluids are not maintained properly. | Resistant to corrosion, offering longer operational life. |
Operational Efficiency | High efficiency but may degrade with fluid contamination. | Maintains high efficiency without fluid-related risks. |
Need help choosing the right vacuum pump for your application? Contact our experts today!