Bead mills and ball mills are both grinding equipment used to reduce particle size in various industries, but they differ significantly in design, operation, and application. Bead mills use small grinding media (beads) agitated by a rotor to create shear forces and collisions, making them highly efficient for fine grinding and dispersion. They are known for high production efficiency, strong continuity, and low cost. Ball mills, on the other hand, use larger grinding media (balls) and rely on tumbling or cascading motion to grind materials. While ball mills are versatile and widely used, they are generally less efficient for fine grinding compared to bead mills. The choice between the two depends on factors like desired particle size, material properties, and operational requirements.
Key Points Explained:
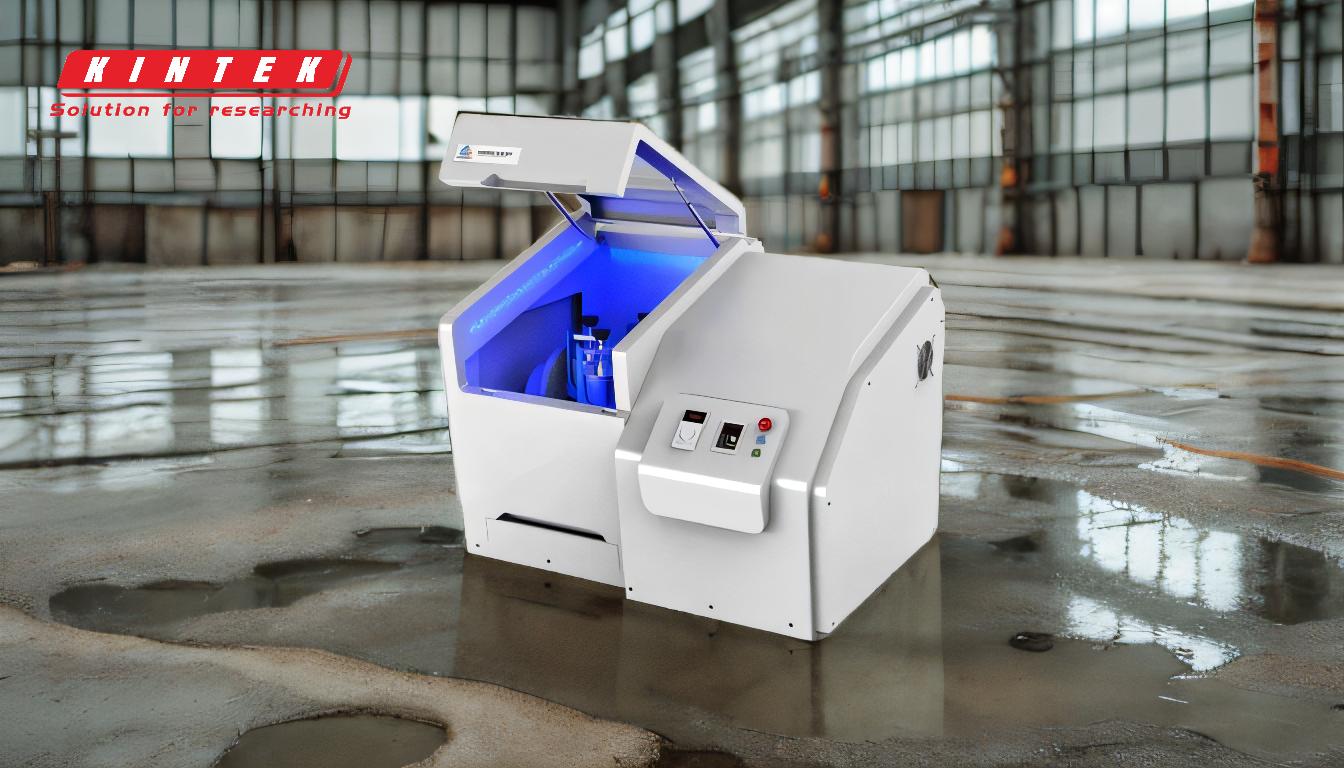
-
Grinding Mechanism:
- Bead Mill: Uses small beads as grinding media, which are agitated by a rotor. This creates intense shear forces and collisions, making it highly effective for fine grinding and dispersion.
- Ball Mill: Uses larger balls as grinding media, which tumble or cascade within a rotating drum. This method is less efficient for fine grinding but is suitable for coarser materials.
-
Efficiency and Fineness:
- Bead Mill: Known for high production efficiency and the ability to achieve very fine particle sizes. It is particularly effective for applications requiring high product fineness.
- Ball Mill: While versatile, it is generally less efficient for achieving very fine particle sizes compared to bead mills.
-
Operational Continuity:
- Bead Mill: Offers strong operational continuity, making it suitable for continuous production processes.
- Ball Mill: Typically operates in batch mode, although continuous ball mills are also available.
-
Cost and Maintenance:
- Bead Mill: Generally has lower operational costs and is easier to maintain, especially in horizontal configurations.
- Ball Mill: May have higher operational costs and maintenance requirements due to the wear and tear of larger grinding media.
-
Installation and Space Requirements:
- Bead Mill: Horizontal bead mills require more installation space but have lower startup power. Vertical bead mills require less space but have higher startup power.
- Ball Mill: Typically requires a significant amount of space and has higher startup power due to the larger size and weight of the grinding media.
-
Applications:
- Bead Mill: Ideal for applications requiring fine grinding and dispersion, such as in the pharmaceutical, chemical, and paint industries.
- Ball Mill: Suitable for a wide range of applications, including mining, ceramics, and metallurgy, where coarser grinding is acceptable.
-
Design Variations:
- Bead Mill: Comes in various designs, including horizontal, vertical, basket, double cone, and nano-level horizontal bead mills, each suited to specific applications and operational requirements.
- Ball Mill: Generally available in standard designs, with variations mainly in size and the type of grinding media used.
In summary, the choice between a bead mill and a ball mill depends on the specific requirements of the grinding process, including the desired particle size, material properties, and operational constraints. Bead mills are generally more efficient for fine grinding and dispersion, while ball mills are more versatile and suitable for coarser grinding applications.
Summary Table:
Feature | Bead Mill | Ball Mill |
---|---|---|
Grinding Mechanism | Small beads agitated by a rotor | Larger balls tumble in a rotating drum |
Efficiency | High efficiency for fine grinding | Less efficient for fine grinding |
Operational Mode | Continuous production | Batch or continuous mode |
Cost & Maintenance | Lower operational costs | Higher operational costs |
Space Requirements | Horizontal: more space, lower power | Requires significant space |
Applications | Fine grinding, dispersion | Coarser grinding, versatile |
Design Variations | Horizontal, vertical, basket, nano | Standard designs, size variations |
Still unsure which grinding equipment suits your needs? Contact our experts today for personalized advice!