Powder coating and PVD (Physical Vapor Deposition) coating are two distinct surface treatment methods used in various industries, each with unique properties, applications, and advantages. Powder coating involves applying a dry polymer powder electrostatically, which is then cured under heat to form a durable, colorful finish. PVD coating, on the other hand, is a vacuum-based process that deposits thin layers of metals, alloys, or ceramics onto a substrate, resulting in a highly durable and environmentally friendly coating. While powder coating is more cost-effective and offers a wide range of colors, PVD coating provides superior durability, precision, and material versatility.
Key Points Explained:
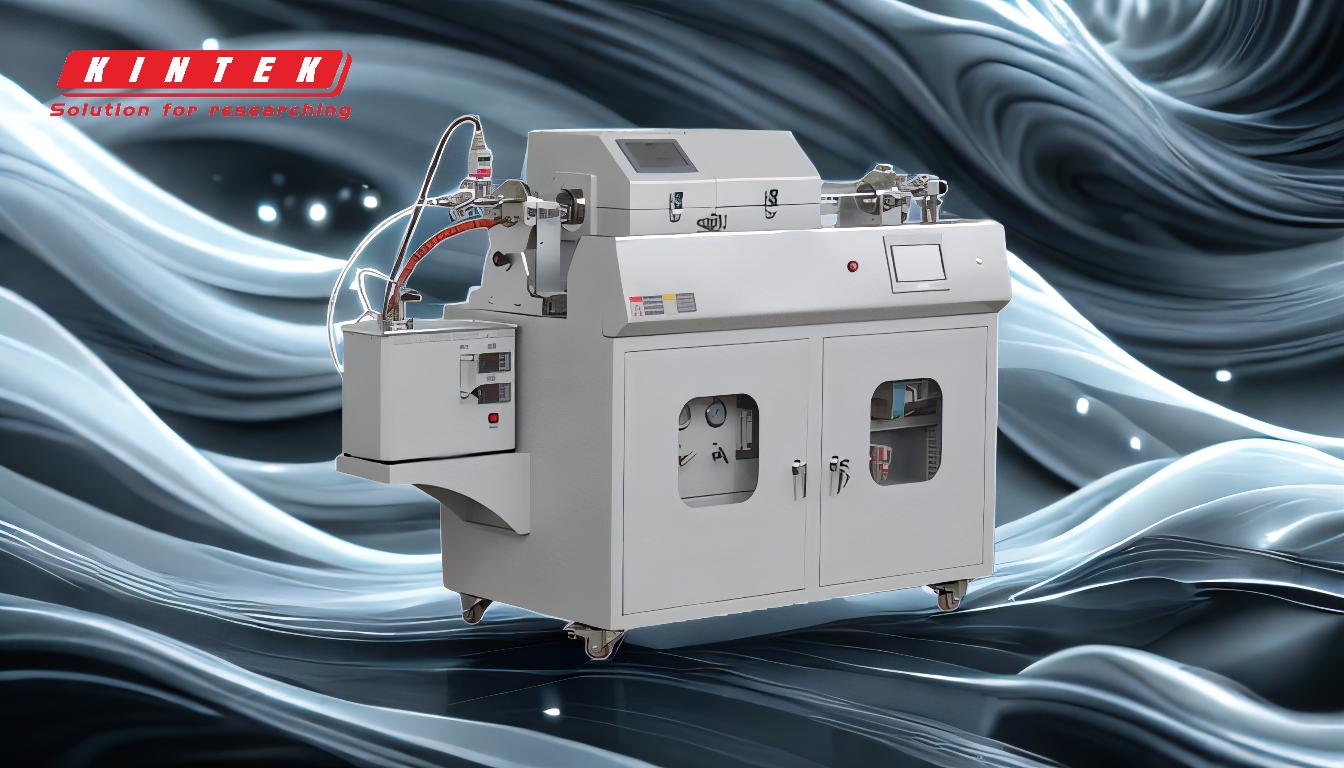
-
Process and Equipment:
- Powder Coating: This process involves applying a dry polymer powder to a surface using an electrostatic charge. The coated object is then cured in an oven, where the powder melts and forms a smooth, durable finish. The equipment required is relatively simple, including a spray gun, curing oven, and powder recovery system.
- PVD Coating: PVD requires specialized equipment, including a vacuum chamber and high-temperature sources. The process involves vaporizing a solid material in a vacuum and depositing it onto the substrate. This method is more complex and requires precise control over temperature and pressure.
-
Coating Thickness and Durability:
- Powder Coating: The coating thickness typically ranges from 25 to 125 microns, making it thicker than PVD coatings. While it provides good durability and resistance to corrosion, it is generally less dense and less wear-resistant compared to PVD coatings.
- PVD Coating: PVD coatings are extremely thin, ranging from 0.5 to 5 microns. Despite their thinness, they are denser and more durable, offering superior resistance to wear, corrosion, and environmental factors.
-
Material Versatility:
- Powder Coating: Limited to organic polymers, powder coating is primarily used for decorative and protective finishes on metals. It offers a wide range of colors and finishes but lacks the material versatility of PVD.
- PVD Coating: PVD can deposit a broad range of materials, including metals, alloys, and ceramics. This versatility makes it suitable for applications requiring specific mechanical, electrical, or optical properties.
-
Environmental Impact:
- Powder Coating: While powder coating is generally considered environmentally friendly due to the absence of solvents, it can produce waste in the form of overspray and requires proper disposal of unused powder.
- PVD Coating: PVD is more environmentally friendly, as it produces no waste or harmful gases. The process is conducted in a vacuum, minimizing environmental impact.
-
Cost and Application:
- Powder Coating: More cost-effective for large-scale applications, powder coating is widely used in industries such as automotive, appliances, and furniture. It is easier to apply and offers a broader range of aesthetic options.
- PVD Coating: PVD is more expensive due to the specialized equipment and process complexity. It is commonly used in high-precision industries such as aerospace, medical devices, and electronics, where durability and performance are critical.
-
Aesthetic and Functional Properties:
- Powder Coating: Offers a wide variety of colors, textures, and finishes, making it ideal for decorative applications. However, it may not provide the same level of functional performance as PVD coatings.
- PVD Coating: While limited in color options, PVD coatings provide exceptional functional properties, including high hardness, low friction, and excellent adhesion. These properties make PVD coatings suitable for demanding applications where performance is paramount.
In summary, the choice between powder coating and PVD coating depends on the specific requirements of the application, including durability, material compatibility, environmental considerations, and budget constraints. Powder coating is ideal for decorative and cost-effective solutions, while PVD coating excels in high-performance, precision applications.
Summary Table:
Feature | Powder Coating | PVD Coating |
---|---|---|
Process | Electrostatic application of dry polymer powder, cured under heat. | Vacuum-based deposition of metals, alloys, or ceramics. |
Coating Thickness | 25–125 microns | 0.5–5 microns |
Durability | Good resistance to corrosion, less wear-resistant. | Superior resistance to wear, corrosion, and environmental factors. |
Material Versatility | Limited to organic polymers. | Broad range of materials (metals, alloys, ceramics). |
Environmental Impact | Environmentally friendly but produces overspray waste. | No waste or harmful gases, minimal environmental impact. |
Cost | Cost-effective for large-scale applications. | More expensive due to specialized equipment and process complexity. |
Applications | Automotive, appliances, furniture (decorative and protective finishes). | Aerospace, medical devices, electronics (high-performance, precision coatings). |
Still unsure which coating method is right for you? Contact our experts today for personalized advice!