Sputtering and Pulsed Laser Deposition (PLD) are both Physical Vapor Deposition (PVD) techniques used to create thin films, but they differ significantly in their mechanisms, applications, and outcomes. Sputtering involves the use of energetic ions to physically eject atoms from a target material, which then deposit onto a substrate. This method does not rely on heat, making it suitable for low-temperature applications and a wide range of materials, including plastics and organics. PLD, on the other hand, uses a high-energy laser pulse to ablate material from a target, creating a plasma plume that deposits onto the substrate. PLD is known for its ability to retain the stoichiometry of the target material, making it ideal for complex materials like oxides and enabling precise control over film microstructure. Both techniques offer unique advantages depending on the specific requirements of the thin film application.
Key Points Explained:
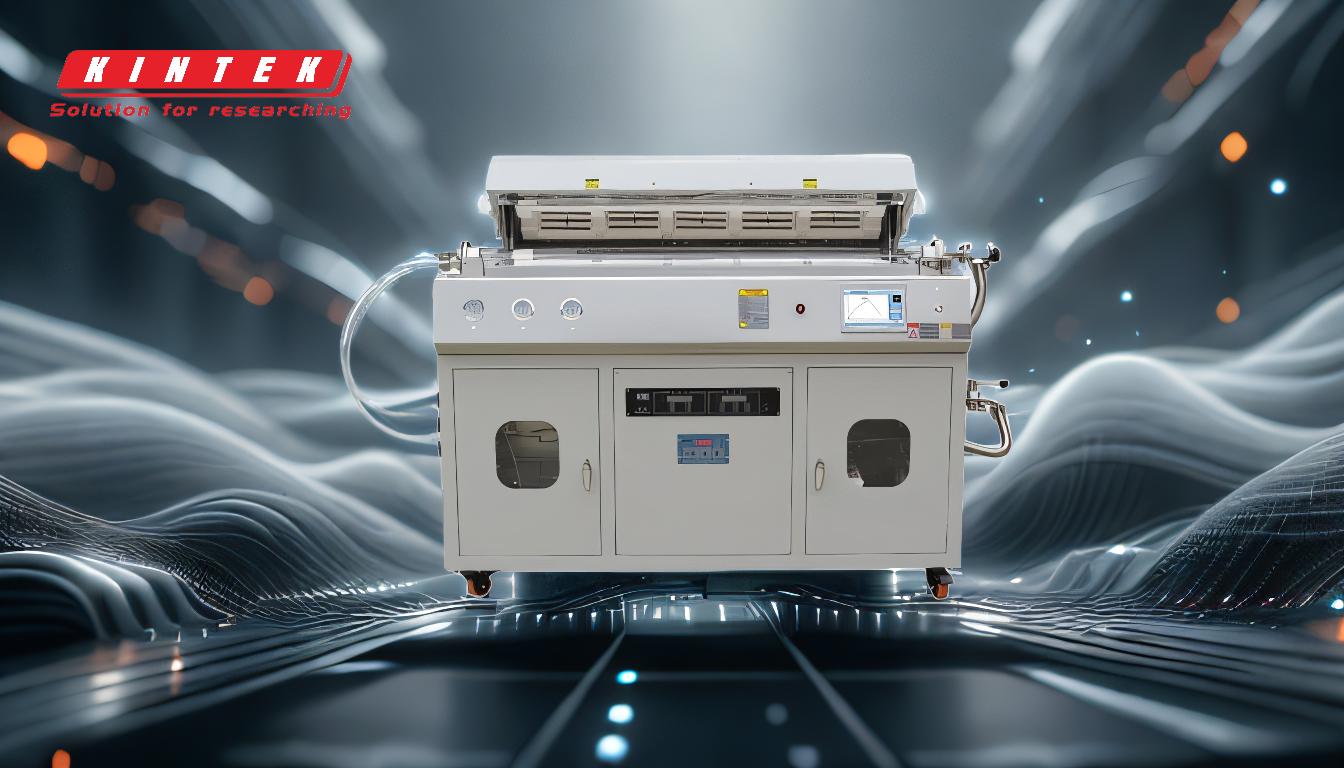
-
Mechanism of Material Ejection:
- Sputtering: In sputtering, a plasma is generated between the target material and the substrate. Energetic ions from the plasma bombard the target, causing atoms to be ejected through momentum transfer. This process does not involve melting the target material, making it suitable for materials that are sensitive to high temperatures.
- PLD: PLD uses a high-energy laser pulse to ablate material from the target. The laser pulse creates a plasma plume consisting of ions, atoms, and molecules from the target, which then condenses onto the substrate. This method is highly precise and can be controlled to achieve specific film properties.
-
Temperature Requirements:
- Sputtering: Sputtering can be performed at relatively low temperatures, which is advantageous for coating temperature-sensitive materials like plastics and organics. The process does not rely on thermal evaporation, reducing the risk of thermal damage to the substrate.
- PLD: PLD also allows for deposition at low substrate temperatures, but the laser ablation process itself can generate localized high temperatures. However, the overall substrate temperature remains low, making it suitable for delicate materials.
-
Stoichiometry and Film Composition:
- Sputtering: While sputtering can produce high-quality films, maintaining the exact stoichiometry of complex materials (e.g., multi-component oxides) can be challenging. The process may lead to slight deviations in composition due to differences in the sputtering yields of different elements.
- PLD: One of the key advantages of PLD is its ability to retain the stoichiometry of the target material in the deposited film. This is particularly important for complex materials where precise composition control is required. PLD is often used for depositing oxides, nitrides, and other multi-component materials.
-
Film Microstructure and Grain Size:
- Sputtering: Sputtering typically produces films with smaller grain sizes and more uniform microstructures. The process allows for good control over film homogeneity and adhesion, making it suitable for applications requiring dense, well-adhered films.
- PLD: PLD offers excellent control over grain size and microstructure, enabling the deposition of films with specific structural properties. This makes PLD ideal for research applications where studying microstructure–property relationships is important.
-
Deposition Rate and Efficiency:
- Sputtering: The deposition rate in sputtering can vary depending on the target material and process conditions. For pure metals, the rate can be relatively high, but for complex materials, it may be lower. Sputtering is generally efficient for large-area coatings and industrial applications.
- PLD: PLD typically has a lower deposition rate compared to sputtering, especially for large-area coatings. However, it excels in precision and control, making it more suitable for research and small-scale applications where film quality is paramount.
-
Applications and Material Compatibility:
- Sputtering: Sputtering is widely used in industries for coating a variety of materials, including metals, semiconductors, and insulators. It is particularly effective for applications requiring good adhesion and uniformity, such as in the production of optical coatings, hard coatings, and electronic devices.
- PLD: PLD is often used in research settings and for specialized applications where precise control over film composition and microstructure is required. It is particularly well-suited for depositing complex materials like high-temperature superconductors, ferroelectric films, and multi-component oxides.
-
Vacuum Requirements:
- Sputtering: Sputtering typically operates at lower vacuum levels compared to other PVD techniques like e-beam evaporation. This can be advantageous for certain applications where maintaining a high vacuum is challenging.
- PLD: PLD usually requires a higher vacuum environment to ensure the purity and quality of the deposited films. The high vacuum helps to minimize contamination and allows for better control over the deposition process.
In summary, while both sputtering and PLD are PVD techniques used for thin film deposition, they differ in their mechanisms, temperature requirements, ability to maintain stoichiometry, control over microstructure, deposition rates, and applications. Sputtering is more versatile for industrial applications and large-area coatings, whereas PLD offers superior precision and control, making it ideal for research and specialized applications.
Summary Table:
Aspect | Sputtering | PLD |
---|---|---|
Mechanism | Energetic ions eject atoms from a target via momentum transfer. | High-energy laser pulse ablates material, creating a plasma plume. |
Temperature | Low-temperature process, suitable for heat-sensitive materials. | Low substrate temperature, but localized high temps during ablation. |
Stoichiometry | Challenging for complex materials; slight deviations may occur. | Retains target material stoichiometry, ideal for complex oxides. |
Microstructure | Smaller grain sizes, uniform films, good adhesion. | Precise control over grain size and microstructure. |
Deposition Rate | High for metals, lower for complex materials; efficient for large areas. | Lower deposition rate, better suited for precision and small-scale use. |
Applications | Industrial coatings, optical films, electronics. | Research, high-temperature superconductors, ferroelectric films. |
Vacuum Requirements | Lower vacuum levels, easier to maintain. | Higher vacuum for purity and quality control. |
Need help choosing the right thin film deposition technique? Contact our experts today for tailored advice!