The primary difference between two-plate and three-plate injection molds lies in their design, gating systems, and applications. Two-plate molds are simpler, typically using side gates for feeding material from the outer side of the cavity, making them suitable for straightforward designs. Three-plate molds, on the other hand, allow for more flexibility in gating, enabling pinpoint gates to be placed anywhere in the cavity, which is ideal for complex or multi-cavity designs. Additionally, three-plate molds can separate the runner system from the part, reducing waste and improving efficiency. The choice between the two depends on the product's design, complexity, and production requirements.
Key Points Explained:
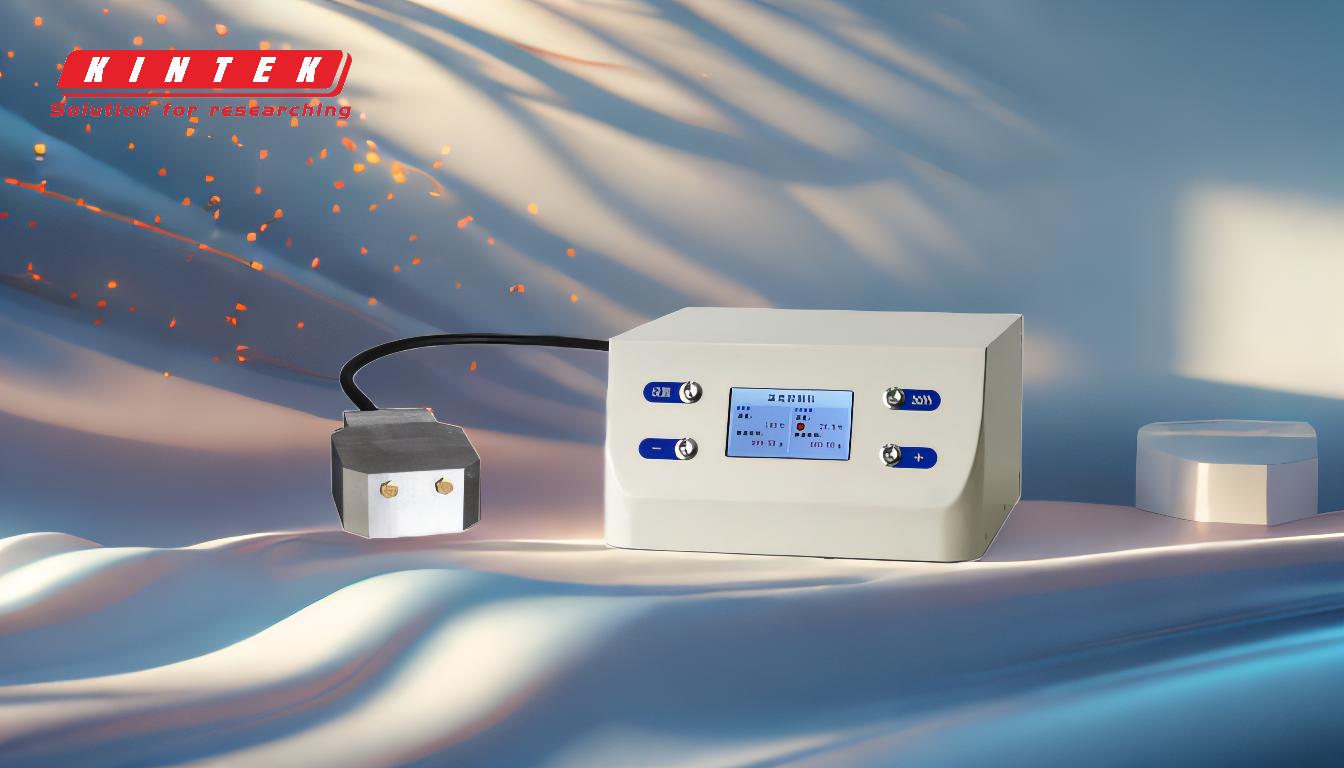
-
Design and Structure:
- Two-Plate Mold: Consists of two main plates (cavity and core plates). It is simpler in design and more cost-effective for basic applications.
- Three-Plate Mold: Includes an additional plate (runner plate) between the cavity and core plates. This design allows for more complex gating systems and separation of the runner system from the part.
-
Gating Systems:
- Two-Plate Mold: Typically uses side gates, which feed material from the outer side of the cavity. This is suitable for simpler designs where the gate location is not critical.
- Three-Plate Mold: Allows for pinpoint gates, which can be placed anywhere in the cavity. This flexibility is beneficial for complex designs or when multiple gates are needed.
-
Applications:
- Two-Plate Mold: Best suited for straightforward designs and single-cavity molds. It is commonly used for products where the gate location is not a critical factor.
- Three-Plate Mold: Ideal for complex designs, multi-cavity molds, and products requiring precise gate placement. It is also used when the runner system needs to be separated from the part to reduce waste.
-
Efficiency and Waste Reduction:
- Two-Plate Mold: The runner system is often attached to the part, which can lead to more material waste.
- Three-Plate Mold: The additional plate allows the runner system to be separated from the part, reducing material waste and improving overall efficiency.
-
Cost Considerations:
- Two-Plate Mold: Generally less expensive to produce and maintain due to its simpler design.
- Three-Plate Mold: More expensive due to the additional plate and complexity in design and maintenance.
-
Product Requirements:
- Two-Plate Mold: Suitable for larger products or those with large holes in the middle, where feeding from the inner side is feasible.
- Three-Plate Mold: Better for products requiring precise gate placement or those with complex geometries that benefit from multiple gate locations.
In summary, the choice between a two-plate and three-plate injection mold depends on the specific requirements of the product, including its design complexity, gate placement needs, and production efficiency goals. Two-plate molds are simpler and more cost-effective for basic applications, while three-plate molds offer greater flexibility and efficiency for complex designs.
Summary Table:
Aspect | Two-Plate Mold | Three-Plate Mold |
---|---|---|
Design | Simpler, with two main plates (cavity and core plates). | Includes an additional runner plate, allowing for more complex gating systems. |
Gating System | Uses side gates, feeding material from the outer side of the cavity. | Allows pinpoint gates, enabling placement anywhere in the cavity for flexibility. |
Applications | Best for straightforward designs and single-cavity molds. | Ideal for complex designs, multi-cavity molds, and precise gate placement. |
Efficiency | Runner system attached to the part, leading to more material waste. | Separates the runner system from the part, reducing waste and improving efficiency. |
Cost | Less expensive due to simpler design and maintenance. | More expensive due to additional plate and complexity. |
Product Requirements | Suitable for larger products or those with large holes in the middle. | Better for products requiring precise gate placement or complex geometries. |
Need help choosing the right injection mold for your project? Contact our experts today for tailored solutions!