The energy required for sputtering is determined by the minimum energy threshold needed to overcome the surface binding energy of the target material. This threshold typically ranges from ten to a hundred electron volts (eV) and is influenced by factors such as the incident ion energy, the mass of the ions and target atoms, and the angle of incidence. The sputtering yield, which is the number of target atoms ejected per incident ion, depends on these factors and varies for different target materials and sputtering conditions. The sputtering rate, which is crucial for uniform thin film deposition, is influenced by the energy of the ions, the mass of the target atoms, and other parameters such as chamber pressure and the type of power source used (DC or RF).
Key Points Explained:
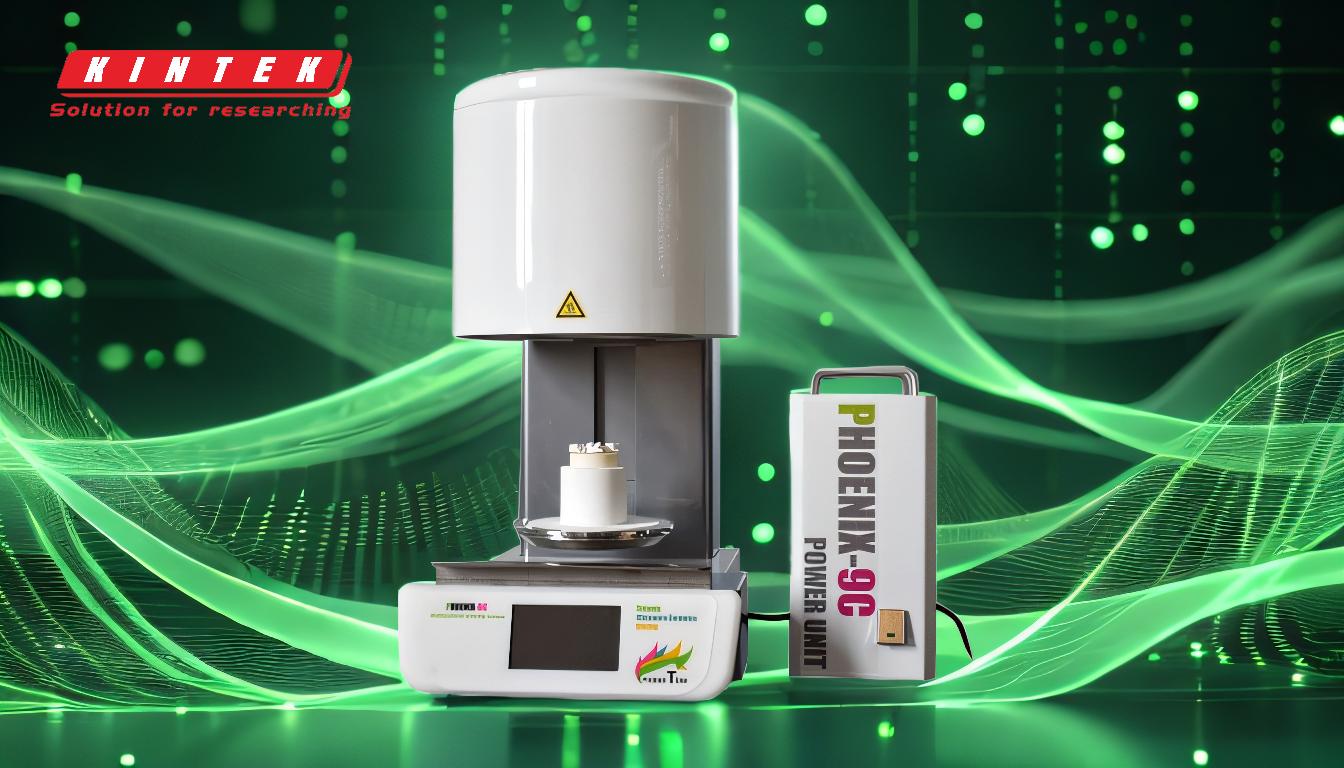
-
Minimum Energy Threshold for Sputtering:
- The minimum energy required for sputtering is the energy needed to transfer enough energy to a target atom to overcome its surface binding energy.
- This threshold typically ranges from 10 to 100 eV.
- The primary energy, which is the minimum energy required to remove an atom from the target material's surface, is typically 3 to 4 times greater than the binding energy of the surface target atoms.
-
Factors Influencing Sputtering Energy:
- Incident Ion Energy: The energy of the ions hitting the target material plays a crucial role in determining whether sputtering will occur. Higher ion energy increases the likelihood of sputtering.
- Mass of Ions and Target Atoms: The mass ratio between the incident ions and the target atoms affects the energy transfer efficiency. Heavier ions can transfer more energy to the target atoms, facilitating sputtering.
- Angle of Incidence: The angle at which ions strike the target surface can influence the sputtering yield. Typically, a more direct angle (closer to perpendicular) results in higher sputtering yields.
-
Sputtering Yield:
- The sputtering yield is defined as the number of target atoms ejected per incident ion.
- It depends on the incident ion energy, the mass of the ions and target atoms, and the angle of incidence.
- The yield varies for different target materials and sputtering conditions, making it a critical parameter in thin film deposition processes.
-
Sputtering Rate:
- The sputtering rate is the number of monolayers per second sputtered from a target's surface.
- It is influenced by the sputter yield (S), the molar weight of the target (M), the material density (p), and the ion current density (j).
- The sputtering rate can be calculated using the equation: Sputtering rate = (MSj)/(pNAe), where NA is the Avogadro number and e is the electron charge.
-
Role of Chamber Pressure and Power Source:
- Chamber Pressure: The pressure within the sputtering chamber can affect the coverage and uniformity of the deposited film. Optimal pressure conditions can improve the quality of the thin film.
- Type of Power Source: The choice between DC and RF power sources affects the deposition rate, material compatibility, and cost. DC sputtering is typically used for conductive materials, while RF sputtering is suitable for insulating materials.
-
Excess Energy and Surface Mobility:
- The excess energy of metal ions can increase surface mobility during the sputtering process, which impacts the quality of the deposited film.
- Higher surface mobility can lead to better film uniformity and fewer defects, which is crucial for applications requiring high-quality thin films.
By understanding these key points, one can better control the sputtering process to achieve desired outcomes in thin film deposition, ensuring uniformity, quality, and efficiency.
Summary Table:
Key Factor | Description |
---|---|
Minimum Energy Threshold | Energy needed to overcome surface binding energy, typically 10–100 eV. |
Incident Ion Energy | Higher ion energy increases sputtering likelihood. |
Mass of Ions & Target Atoms | Heavier ions transfer more energy, facilitating sputtering. |
Angle of Incidence | Direct angles (closer to perpendicular) yield higher sputtering rates. |
Sputtering Yield | Number of target atoms ejected per incident ion, varies by material & conditions. |
Sputtering Rate | Influenced by sputter yield, molar weight, material density, and ion current. |
Chamber Pressure | Affects film uniformity; optimal pressure improves quality. |
Power Source (DC/RF) | DC for conductive materials, RF for insulating materials. |
Excess Energy & Mobility | Increases surface mobility, improving film uniformity and reducing defects. |
Optimize your sputtering process for high-quality thin films—contact our experts today!