The evaporation method is a widely used technique in material science and thin-film deposition, where a material is heated to its evaporation or sublimation point, transforming it into a vapor. This vapor is then deposited onto a substrate, forming a thin film. The process typically occurs in a vacuum environment to minimize gas collisions and ensure a clean, high-quality deposition. Various techniques, such as resistive heating, electron beam evaporation, and flash evaporation, are employed depending on the material properties and desired film characteristics. The method is highly versatile, used in applications ranging from semiconductor manufacturing to creating protective coatings.
Key Points Explained:
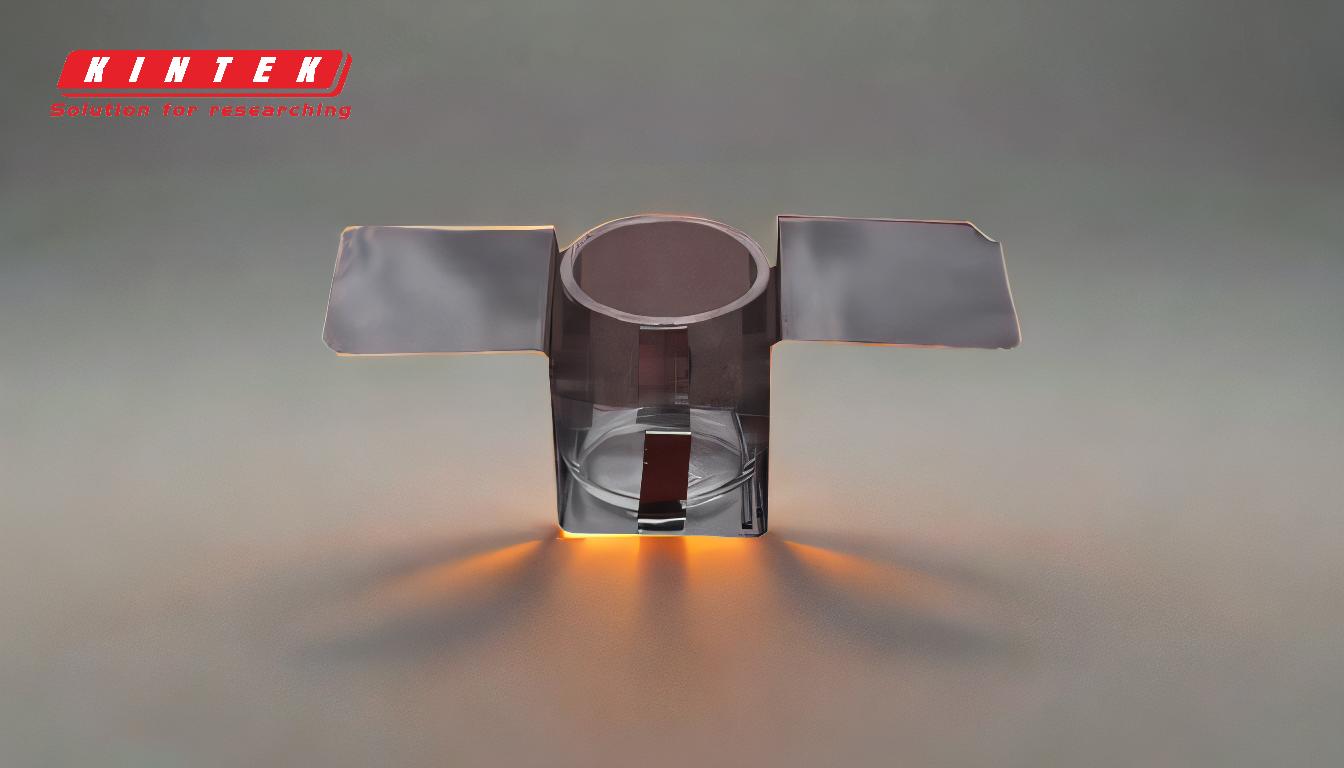
-
Definition and Basic Principle of Evaporation Method:
- The evaporation method involves heating a material until it evaporates or sublimes, transforming it into a vapor phase.
- The vapor is then condensed onto a substrate, forming a thin film.
- This process is analogous to steam condensing into water droplets on a cold surface.
-
Vacuum Environment:
- The process is typically conducted in a high-vacuum chamber to:
- Minimize gas collisions, ensuring a free path for vapor particles.
- Reduce unwanted chemical reactions and trapped gas layers.
- Control heat transfer and maintain a clean deposition environment.
- The process is typically conducted in a high-vacuum chamber to:
-
Types of Evaporation Techniques:
- Resistive Thermal Evaporation: Uses electrical resistance to heat the material.
- Electron Beam Evaporation: Employs a focused electron beam to heat and evaporate the material.
- Flash Evaporation: Rapidly heats small amounts of material to achieve quick vaporization.
- Induction Heating Evaporation: Uses electromagnetic induction to heat the material.
- Knudsen Cell Evaporation: Utilizes a controlled heating cell for precise vaporization.
-
Applications of Evaporation Methods:
- Thin-Film Deposition: Used in semiconductor manufacturing, optical coatings, and solar cell production.
- Protective Coatings: Applied to enhance durability and resistance to wear, corrosion, and oxidation.
- Laboratory Techniques: Includes rotary evaporation, nitrogen evaporation, and centrifugal evaporation for sample preparation and concentration.
-
Advantages of Evaporation Methods:
- High Purity: The vacuum environment minimizes contamination, resulting in high-quality films.
- Versatility: Suitable for a wide range of materials, including metals, ceramics, and polymers.
- Precision: Allows for precise control over film thickness and uniformity.
-
Challenges and Considerations:
- Material Limitations: Some materials may decompose or react at high temperatures.
- Line-of-Sight Deposition: The method coats only surfaces within the direct line of sight of the vapor source.
- Equipment Complexity: Requires specialized vacuum systems and heating mechanisms, increasing costs.
-
Comparison with Other Deposition Methods:
- Physical Vapor Deposition (PVD): Evaporation is a subset of PVD, focusing on heating materials to a gas phase.
- Chemical Vapor Deposition (CVD): Unlike evaporation, CVD involves chemical reactions to deposit materials.
-
Future Trends and Innovations:
- Nanotechnology: Evaporation methods are being adapted for the fabrication of nanostructures and nanoparticles.
- Energy Efficiency: Development of more energy-efficient heating techniques to reduce operational costs.
- Automation: Integration of automated systems for improved process control and reproducibility.
By understanding these key points, equipment and consumable purchasers can make informed decisions about the suitability of evaporation methods for their specific applications, ensuring optimal performance and cost-effectiveness.
Summary Table:
Aspect | Details |
---|---|
Definition | Heating a material to its evaporation point, forming a thin film on a substrate. |
Vacuum Environment | Ensures minimal gas collisions, clean deposition, and controlled heat transfer. |
Techniques | Resistive heating, electron beam evaporation, flash evaporation, and more. |
Applications | Semiconductor manufacturing, protective coatings, and laboratory techniques. |
Advantages | High purity, versatility, and precise control over film thickness. |
Challenges | Material limitations, line-of-sight deposition, and equipment complexity. |
Discover how the evaporation method can enhance your material science projects—contact us today for expert guidance!