The feed and product size of a ball mill are critical factors in determining its efficiency and suitability for specific grinding tasks. The feed size refers to the initial size of the material entering the mill, while the product size is the final particle size after grinding. Smaller feed sizes and longer grinding times generally result in finer product sizes. The productivity of a ball mill is influenced by several factors, including drum diameter, the ratio of drum diameter to length, physical-chemical properties of the feed material, ball filling and sizes, armor surface shape, rotation speed, milling fineness, and timely removal of the ground product. Understanding these factors helps in optimizing the grinding process to achieve desired particle sizes efficiently.
Key Points Explained:
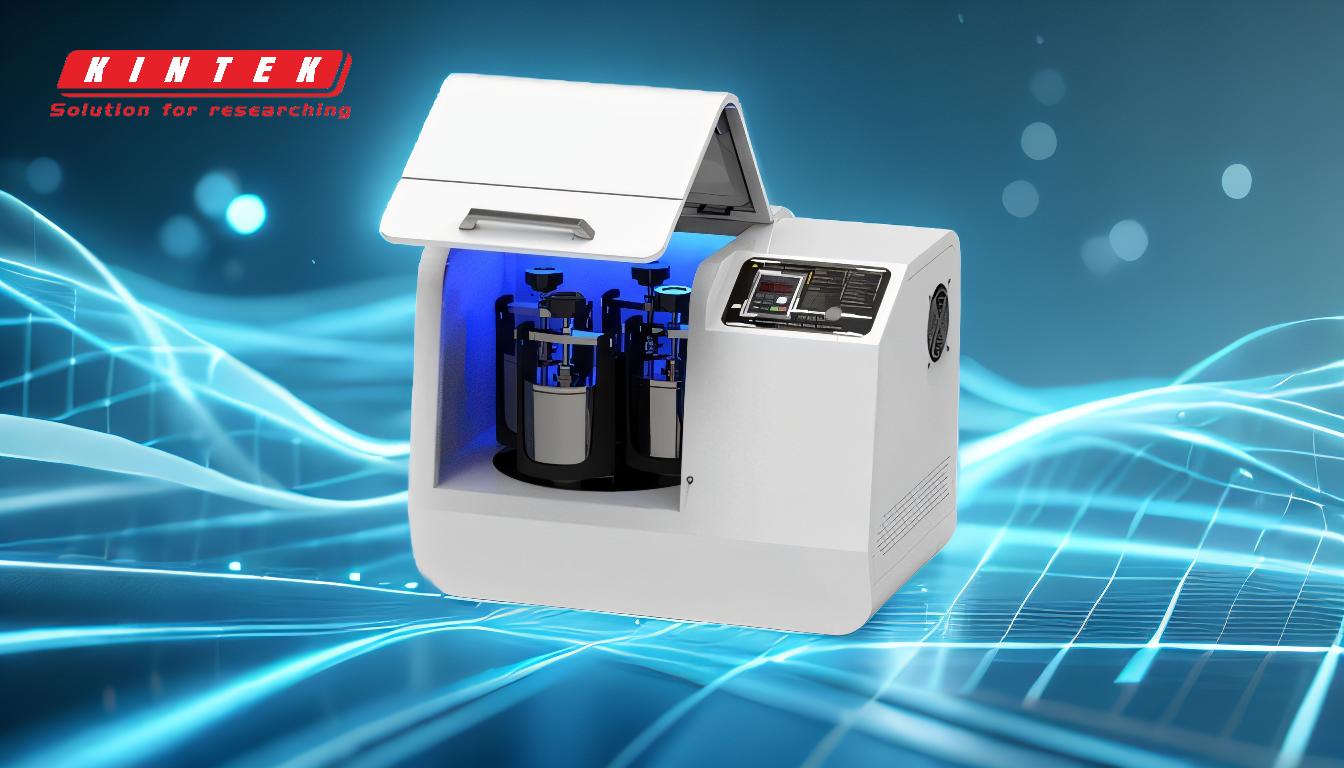
-
Feed Size:
- The feed size is the initial size of the material that is introduced into the ball mill. It is a crucial parameter because it directly affects the grinding efficiency and the final product size.
- Smaller feed sizes are generally easier to grind and can result in finer product sizes. Larger feed sizes may require more energy and time to achieve the desired fineness.
-
Product Size:
- The product size is the final particle size achieved after the grinding process. It is determined by the grinding time, the size of the grinding media (balls), and the operational parameters of the mill.
- Producing smaller particles typically requires smaller grinding balls and longer grinding times. The relationship between grinding time and particle size is often logarithmic, meaning that achieving very fine particles can require significantly more time.
-
Influence of Drum Diameter and Length:
- The drum diameter and the ratio of drum diameter to length (L:D ratio) are important design parameters that affect the grinding efficiency. An optimal L:D ratio is typically between 1.56 and 1.64.
- A larger drum diameter can increase the capacity of the mill, while the L:D ratio influences the residence time of the material inside the mill, affecting the grinding efficiency and product size.
-
Physical-Chemical Properties of Feed Material:
- The hardness, brittleness, and moisture content of the feed material can significantly influence the grinding process. Harder materials may require more energy and time to grind, while brittle materials may break more easily.
- The chemical properties, such as reactivity, can also affect the grinding process, especially if the material interacts with the grinding media or the mill lining.
-
Ball Filling and Sizes:
- The amount of grinding media (balls) and their sizes are critical factors. A higher ball filling can increase the grinding efficiency but may also increase energy consumption.
- Smaller balls are generally used for finer grinding, while larger balls are used for coarser grinding. The size distribution of the balls should be optimized to achieve the desired product size.
-
Armor Surface Shape:
- The shape and design of the mill's internal lining (armor) can influence the grinding process. A smoother surface may reduce wear and tear but could also affect the grinding efficiency.
- The armor surface shape can also impact the movement of the grinding media and the material inside the mill, affecting the grinding kinetics.
-
Rotation Speed:
- The rotation speed of the mill determines the centrifugal force acting on the grinding media and the material. An optimal rotation speed ensures that the grinding media cascade and impact the material effectively.
- Too high a speed can cause the grinding media to centrifuge, reducing grinding efficiency, while too low a speed may not provide enough impact force.
-
Milling Fineness:
- The desired fineness of the product is a key parameter that influences the grinding process. Achieving finer particles may require adjustments in grinding time, ball size, and rotation speed.
- The milling fineness is often specified based on the application requirements, such as in mineral processing or chemical manufacturing.
-
Timely Removal of Ground Product:
- Efficient removal of the ground product from the mill is essential to prevent over-grinding and to maintain consistent product quality.
- Over-grinding can lead to excessive energy consumption and may degrade the quality of the product. Timely removal ensures that the grinding process is optimized for both efficiency and product quality.
In summary, the feed and product size of a ball mill are influenced by a combination of factors, including the initial feed size, grinding time, ball size, drum dimensions, material properties, and operational parameters. Understanding and optimizing these factors is essential for achieving the desired grinding efficiency and product quality.
Summary Table:
Factor | Impact on Grinding Efficiency |
---|---|
Feed Size | Smaller feed sizes result in finer product sizes; larger sizes require more energy and time. |
Product Size | Determined by grinding time, ball size, and operational parameters; finer particles take longer. |
Drum Diameter & L:D Ratio | Larger diameter increases capacity; optimal L:D ratio (1.56–1.64) improves efficiency. |
Material Properties | Hardness, brittleness, and moisture affect grinding energy and time. |
Ball Filling & Sizes | Higher filling increases efficiency; smaller balls for finer grinding. |
Armor Surface Shape | Influences grinding kinetics; smoother surfaces reduce wear but may affect efficiency. |
Rotation Speed | Optimal speed ensures effective grinding; too high or low speeds reduce efficiency. |
Milling Fineness | Desired fineness requires adjustments in time, ball size, and speed. |
Product Removal | Timely removal prevents over-grinding and maintains product quality. |
Optimize your ball mill efficiency—contact our experts today for tailored solutions!