The feed size of a ball mill is a critical parameter that determines the efficiency and effectiveness of the grinding process. It refers to the maximum size of the material that can be fed into the mill for grinding. The optimal feed size depends on factors such as the type of material, the size of the grinding media, and the desired final product size. Generally, the feed size should be smaller than the diameter of the grinding media to ensure effective grinding. Larger feed sizes may require pre-crushing to achieve the desired particle size distribution.
Key Points Explained:
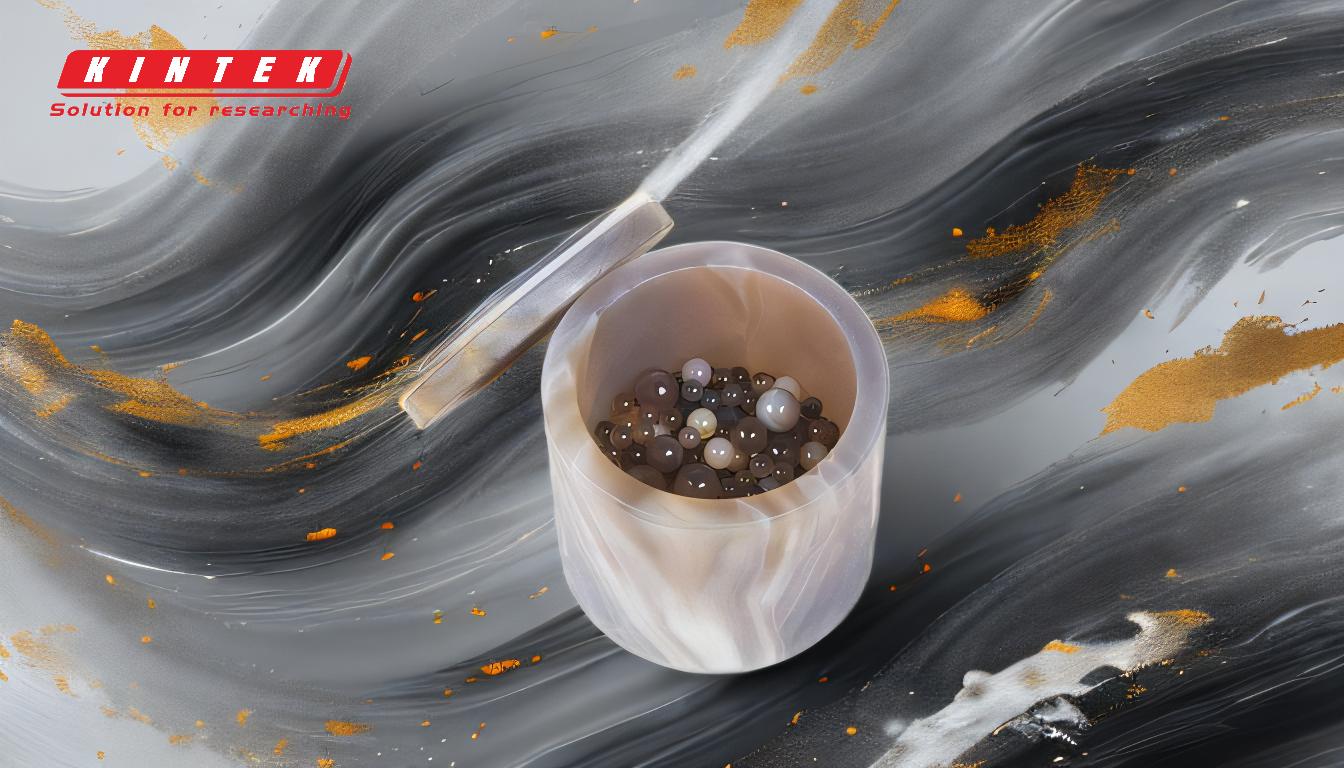
-
Definition of Feed Size:
- The feed size of a ball mill refers to the maximum size of the material that can be introduced into the mill for grinding.
- It is a crucial parameter that affects the efficiency of the grinding process and the quality of the final product.
-
Factors Influencing Feed Size:
- Material Type: Different materials have different hardness and brittleness, which affect the optimal feed size.
- Grinding Media Size: The size of the grinding balls or rods used in the mill plays a significant role in determining the appropriate feed size.
- Desired Final Product Size: The target particle size distribution of the final product influences the required feed size.
-
Optimal Feed Size:
- The feed size should generally be smaller than the diameter of the grinding media to ensure effective grinding.
- For example, if the grinding media has a diameter of 25 mm, the feed size should be less than 25 mm to achieve efficient grinding.
-
Pre-Crushing for Larger Feed Sizes:
- If the material to be ground has a larger initial size, pre-crushing may be necessary to reduce the feed size to an appropriate level.
- Pre-crushing can be done using jaw crushers, cone crushers, or other size reduction equipment.
-
Impact of Feed Size on Grinding Efficiency:
- Too Large Feed Size: If the feed size is too large, it can lead to inefficient grinding, increased energy consumption, and potential damage to the mill.
- Too Small Feed Size: If the feed size is too small, it may result in over-grinding, which can lead to excessive wear on the grinding media and mill liners.
-
Practical Considerations:
- Material Hardness: Harder materials may require smaller feed sizes to achieve the desired grinding efficiency.
- Mill Design: The design of the ball mill, including the length-to-diameter ratio and the type of liner, can influence the optimal feed size.
- Operational Parameters: Factors such as mill speed, ball charge, and slurry density also play a role in determining the appropriate feed size.
-
Case Studies and Examples:
- In the cement industry, the feed size for ball mills typically ranges from 15 mm to 25 mm, depending on the type of raw material and the desired fineness of the final product.
- In the mining industry, the feed size for ball mills can vary widely, from a few millimeters to several centimeters, depending on the ore type and the grinding circuit design.
-
Measurement and Control:
- The feed size can be measured using sieves or particle size analyzers.
- Proper control of the feed size is essential to maintain consistent grinding performance and product quality.
In conclusion, the feed size of a ball mill is a critical parameter that must be carefully considered to ensure efficient and effective grinding. It depends on various factors, including the type of material, the size of the grinding media, and the desired final product size. Proper control and optimization of the feed size can lead to improved grinding efficiency, reduced energy consumption, and higher-quality final products.
Summary Table:
Key Aspect | Details |
---|---|
Definition of Feed Size | Maximum material size fed into the ball mill for grinding. |
Factors Influencing Feed Size | Material type, grinding media size, and desired final product size. |
Optimal Feed Size | Should be smaller than grinding media diameter (e.g., <25 mm for 25 mm media). |
Pre-Crushing for Larger Sizes | Required for materials exceeding optimal feed size. |
Impact on Efficiency | Too large: inefficient grinding. Too small: over-grinding and wear. |
Practical Considerations | Material hardness, mill design, and operational parameters. |
Case Studies | Cement industry: 15-25 mm. Mining: varies widely based on ore type. |
Measurement & Control | Use sieves or particle size analyzers for consistent performance. |
Optimize your ball mill's performance—contact our experts today for tailored solutions!