A diffusion pump is a specialized vacuum pump designed to achieve extremely low pressures, far below what mechanical pumps can accomplish alone. It operates by heating diffusion pump oil to create a high-speed vapor stream that captures and removes air molecules from a vacuum chamber. This process relies on the vapor's ability to entrap gas molecules and direct them downward, where they are expelled at the base of the pump. The pump's design, which includes a heater, condensing coils, and a vertically tapered stack with jet openings, ensures efficient operation without any moving parts. Diffusion pumps are essential in applications requiring high vacuum levels, such as in laboratories, industrial processes, and scientific research, where maintaining a clean, low-pressure environment is critical.
Key Points Explained:
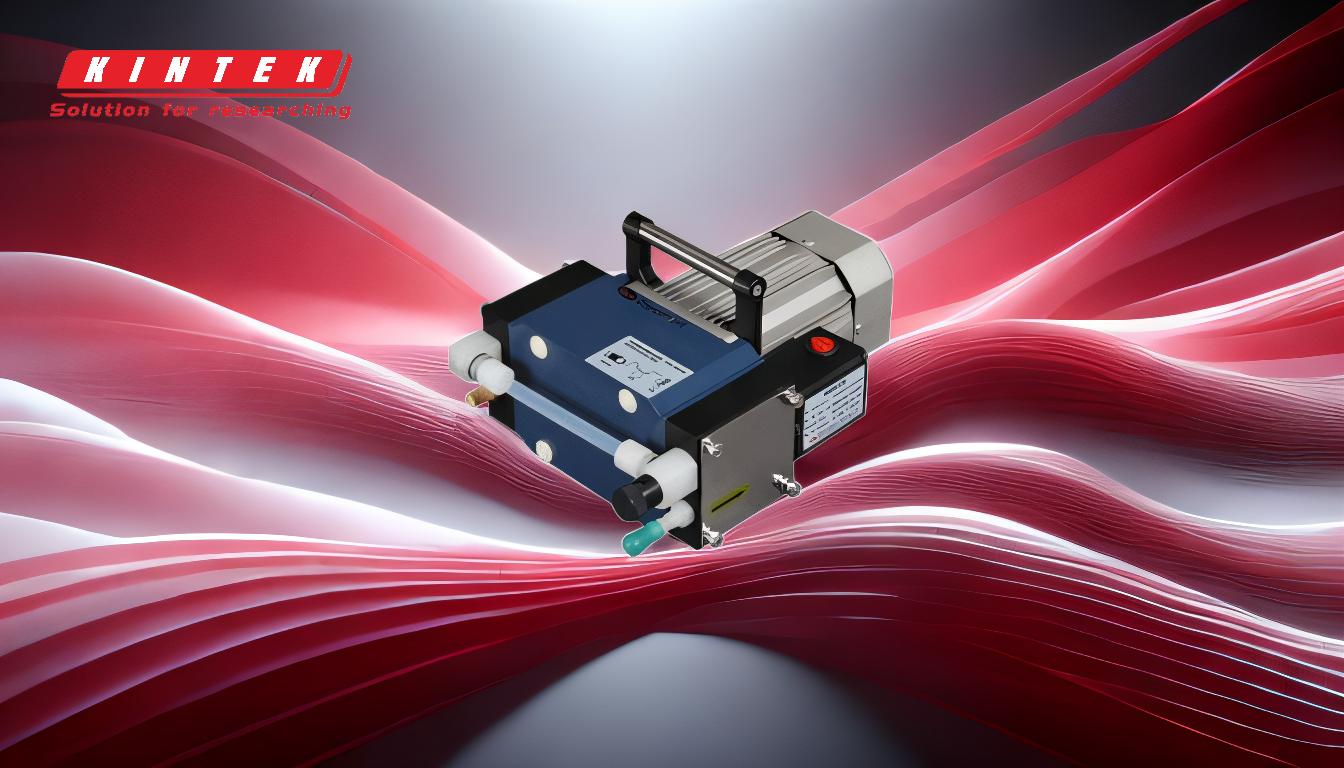
-
Primary Function of a Diffusion Pump:
- A diffusion pump is used to achieve high vacuum levels that cannot be reached by mechanical pumps alone. It is particularly necessary when the desired vacuum level is below 10^-2 Pa, as mechanical pumps have limited pumping speed at such low pressures.
- It works by creating a differential pressure between the top (connected to the vacuum chamber) and the bottom of the pump, enabling the removal of air molecules from the chamber.
-
Operating Principle:
- The pump operates using diffusion pump oil and a heater. The heater heats the boilerplate, causing the oil to boil and produce oil vapor.
- The rising oil vapor is compressed in a vertically tapered stack with jet openings, forming an umbrella of vapor that captures air molecules.
- The vapor stream moves downward, guided by cool condensing coils on the pump’s exterior, which help the oil condense and return to the reservoir.
- The captured air is released at the base of the pump, while the condensed oil is recycled for reuse.
-
Key Components:
- Heater: Heats the diffusion pump oil to generate the necessary vapor.
- Boilerplate: The area where the oil is heated and vaporized.
- Jet Openings: Direct the oil vapor upward and then downward, creating the vapor stream that entraps air molecules.
- Condensing Coils: Cool the oil vapor, causing it to condense and return to the reservoir.
- Reservoir: Collects the condensed oil for reuse in the cycle.
-
Advantages of Diffusion Pumps:
- No Moving Parts: Unlike mechanical pumps, diffusion pumps operate without any moving parts, reducing wear and tear and ensuring long-term reliability.
- High Pumping Speed: They can achieve very high pumping speeds, making them ideal for applications requiring rapid evacuation of large volumes of gas.
- High Vacuum Levels: Capable of reaching vacuum levels as low as 10^-7 Pa, which is essential for applications like electron microscopy, semiconductor manufacturing, and space simulation.
-
Applications:
- Laboratory Use: Diffusion pumps are used in laboratories for tasks such as filtration, aspiration of liquid samples, and controlling solvent evaporation by reducing vapor pressure.
- Scientific Research: They are essential in research environments where high vacuum levels are required, such as in particle physics experiments or material science studies.
- Industrial Processes: Used in industries like semiconductor manufacturing and thin-film coating, where maintaining a clean, low-pressure environment is critical.
- Hazardous Material Containment: They help create a negative pressure environment to prevent the escape of hazardous materials.
-
Comparison with Mechanical Pumps:
- Limitations of Mechanical Pumps: Mechanical pumps alone cannot achieve the ultra-high vacuum levels required for many advanced applications. Their pumping speed decreases significantly at pressures below 10^-2 Pa.
- Complementary Role of Diffusion Pumps: Diffusion pumps are often used in conjunction with mechanical pumps. The mechanical pump provides the initial rough vacuum, while the diffusion pump takes over to achieve the final high vacuum.
-
Maintenance and Considerations:
- Oil Quality: The performance of a diffusion pump depends heavily on the quality of the diffusion pump oil. Contaminated or degraded oil can reduce efficiency and lead to pump failure.
- Cooling System: Proper functioning of the condensing coils is crucial. Any issues with the cooling system can disrupt the condensation process and reduce the pump’s effectiveness.
- Backstreaming: A small amount of oil molecules may remain in the vacuum chamber, which can be a concern in sensitive applications. Using cold traps or baffles can mitigate this issue.
-
Environmental and Safety Considerations:
- Oil Handling: Proper handling and disposal of diffusion pump oil are essential to prevent environmental contamination.
- Heat Management: The heater generates significant heat, so adequate ventilation and cooling are necessary to ensure safe operation.
By understanding these key points, purchasers and users of diffusion pumps can make informed decisions about their selection, operation, and maintenance, ensuring optimal performance and longevity in their specific applications.
Summary Table:
Aspect | Details |
---|---|
Primary Function | Achieves high vacuum levels below 10^-2 Pa, surpassing mechanical pumps. |
Operating Principle | Uses heated oil vapor to capture and remove air molecules from a vacuum. |
Key Components | Heater, boilerplate, jet openings, condensing coils, and reservoir. |
Advantages | No moving parts, high pumping speed, and vacuum levels as low as 10^-7 Pa. |
Applications | Labs, scientific research, semiconductor manufacturing, and hazardous material containment. |
Maintenance Tips | Ensure oil quality, proper cooling system function, and prevent backstreaming. |
Discover how a diffusion pump can optimize your vacuum processes—contact us today for expert advice!