A mixer is a complex piece of equipment designed to blend, homogenize, or mix materials efficiently. Its internal structure consists of several critical components that work together to ensure optimal performance. These components include the mixing chamber, rotor, upper and lower bolts, cooling system, lubrication system, sealing device, and transmission device. Each part plays a specific role in the mixing process, contributing to the overall functionality and durability of the mixer. Understanding the internal structure is essential for equipment purchasers to evaluate the suitability of a mixer for their specific applications and to ensure proper maintenance and operation.
Key Points Explained:
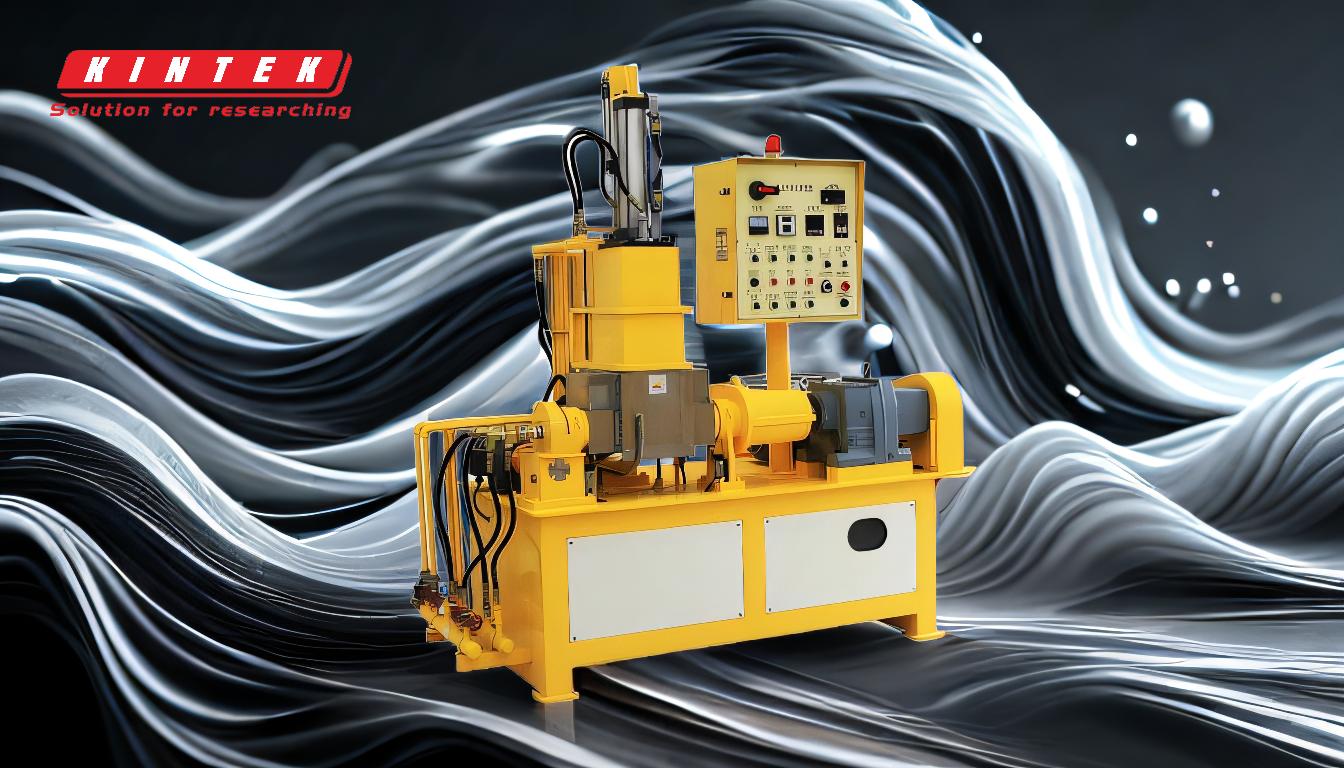
-
Mixing Chamber:
- The mixing chamber is the central part of the mixer where the actual blending of materials occurs.
- It is designed to withstand high pressures and temperatures, ensuring efficient mixing without compromising the integrity of the materials.
- The chamber's size and shape can vary depending on the type of mixer and the materials being processed.
-
Rotor:
- The rotor is a rotating component inside the mixing chamber that facilitates the movement and blending of materials.
- It is typically equipped with blades or paddles that create shear forces, ensuring thorough mixing.
- The design of the rotor is crucial for achieving the desired mixing efficiency and consistency.
-
Upper and Lower Bolts:
- These bolts are used to secure the mixing chamber and other components in place.
- The upper bolt is usually located at the top of the mixing chamber, while the lower bolt is positioned at the bottom.
- Proper tightening of these bolts is essential to prevent leaks and ensure the stability of the mixer during operation.
-
Cooling System:
- The cooling system is designed to regulate the temperature inside the mixing chamber.
- It prevents overheating, which can degrade the quality of the materials being mixed and damage the mixer's components.
- The cooling system may use water, air, or other cooling mediums, depending on the mixer's design and application.
-
Lubrication System:
- The lubrication system ensures that all moving parts of the mixer, such as the rotor and transmission device, are properly lubricated.
- This reduces friction and wear, extending the lifespan of the mixer and maintaining its efficiency.
- Regular maintenance of the lubrication system is crucial to prevent breakdowns and ensure smooth operation.
-
Sealing Device:
- The sealing device is used to prevent leaks and contamination of the materials being mixed.
- It is typically located at the joints and openings of the mixing chamber.
- High-quality seals are essential for maintaining the integrity of the mixing process and ensuring the safety of the operators.
-
Transmission Device:
- The transmission device is responsible for transferring power from the motor to the rotor.
- It includes components such as gears, belts, and shafts that work together to ensure smooth and efficient operation.
- The design and quality of the transmission device are critical for the overall performance and reliability of the mixer.
Understanding these key components and their functions is essential for anyone involved in the purchase, operation, or maintenance of mixers. Each component plays a vital role in ensuring the mixer's performance, durability, and safety, making it crucial to consider these factors when selecting a mixer for specific applications.
Summary Table:
Component | Function | Importance |
---|---|---|
Mixing Chamber | Central area for blending materials | Ensures efficient mixing and withstands high pressures/temperatures |
Rotor | Rotates to facilitate material movement and blending | Crucial for achieving consistent mixing efficiency |
Upper and Lower Bolts | Secures the mixing chamber and components | Prevents leaks and ensures stability during operation |
Cooling System | Regulates temperature to prevent overheating | Protects materials and components from heat damage |
Lubrication System | Lubricates moving parts to reduce friction and wear | Extends equipment lifespan and maintains efficiency |
Sealing Device | Prevents leaks and contamination | Ensures process integrity and operator safety |
Transmission Device | Transfers power from the motor to the rotor | Critical for smooth and reliable operation |
Ready to find the perfect mixer for your needs? Contact our experts today for personalized advice!