A colloid mill operates on the rotor-stator principle, where a rapidly rotating cone (rotor) and a static cone (stator) create a small gap. The material is subjected to intense shearing forces in this gap, leading to the breakdown of solid particles into smaller sizes and their dispersion in a liquid medium. This process is particularly effective for creating suspensions of solids not easily moistened by the liquid. The colloid mill is versatile, capable of superfine grinding, emulsifying, homogenizing, and dispersing in a single cycle. Its design features, such as adjustable rotor-stator gaps, stainless steel construction, and low maintenance, make it suitable for various industries, including food, pharmaceuticals, and chemicals.
Key Points Explained:
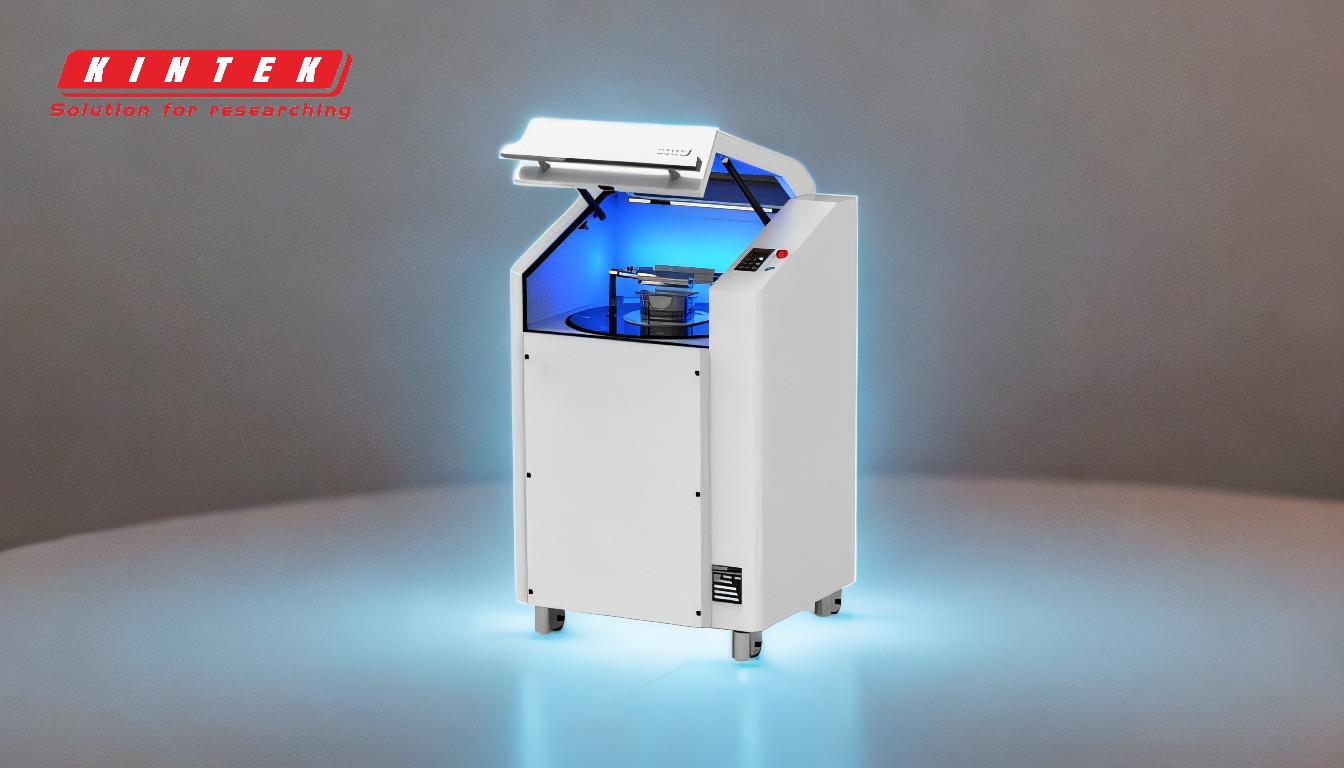
-
Rotor-Stator Principle:
- The colloid mill operates using a rotor-stator system, where the rotor is a rapidly rotating cone and the stator is a static cone.
- The small gap between the rotor and stator is critical for generating high shear forces, which break down solid particles into smaller sizes.
- This principle is effective for creating dispersions and suspensions in liquids.
-
Shearing Mechanism:
- The primary mechanism of action in a colloid mill is shearing, which occurs as the material passes through the narrow gap between the rotor and stator.
- The high-speed rotation of the rotor generates intense shear forces, leading to the comminution (size reduction) of solid particles.
- This shearing action is particularly useful for materials that are not easily wetted by the dispersion medium.
-
Applications:
- The colloid mill is commonly used for the comminution of solids and the creation of suspensions.
- It is especially effective for materials where the solid particles are not easily moistened by the liquid medium.
- The mill is versatile and can be used in various industries, including food processing, pharmaceuticals, and chemical manufacturing.
-
Superfine Grinding and Simultaneous Processes:
- The colloid mill can achieve superfine grinding results, reducing particles to very small sizes.
- In addition to grinding, the mill can simultaneously perform emulsifying, homogenizing, and dispersing processes in a single cycle.
- This multifunctionality makes the colloid mill a valuable tool in processes requiring fine particle size and uniform dispersion.
-
Design Features:
- The colloid mill is designed with a compact footprint, making it suitable for use in limited spaces.
- It is constructed with Stainless Steel 316 for all contact parts and Stainless Steel 304 for moving parts, ensuring durability and compliance with food-grade standards.
- The mill features food-grade seals to prevent contamination, making it suitable for use in the food and pharmaceutical industries.
- The rotor-stator gap can be easily adjusted, allowing for precise control over the grinding process.
- Optional features, such as overload pressure release mechanisms and castor wheels for mobility, enhance the mill's usability and safety.
-
Ease of Use and Maintenance:
- The colloid mill is designed for ease of use, with simple adjustments and low maintenance requirements.
- The use of high-quality materials and robust construction reduces the need for frequent maintenance, ensuring long-term reliability.
- The mill's design complies with cGMP (current Good Manufacturing Practices), making it suitable for use in regulated industries.
-
Versatility in Drive Systems:
- The colloid mill offers options for both horizontal and vertical drive systems, providing flexibility in installation and operation.
- This versatility allows the mill to be integrated into various production lines, depending on the specific requirements of the process.
In summary, the colloid mill's mechanism of action is based on the rotor-stator principle, where high shear forces generated in the narrow gap between the rotor and stator lead to the breakdown of solid particles and their dispersion in a liquid medium. Its design features, ease of use, and multifunctionality make it a valuable tool in various industries for achieving superfine grinding, emulsifying, homogenizing, and dispersing in a single process cycle.
Summary Table:
Key Feature | Description |
---|---|
Rotor-Stator Principle | High shear forces in a small gap break down solid particles into smaller sizes. |
Shearing Mechanism | Intense shear forces reduce particle size and disperse materials in liquids. |
Applications | Food, pharmaceuticals, chemicals—ideal for suspensions and dispersions. |
Superfine Grinding | Achieves fine particle sizes and performs multiple processes in one cycle. |
Design Features | Stainless steel construction, adjustable gaps, and food-grade seals. |
Ease of Use | Simple adjustments, low maintenance, and cGMP compliance. |
Versatility | Horizontal and vertical drive systems for flexible integration. |
Ready to enhance your production process with a colloid mill? Contact us today for expert guidance!