The minimum speed of a ball mill is determined by the point at which the grinding balls begin to cascade, ensuring effective grinding. If the speed is too low, the balls slide or roll over each other, resulting in minimal size reduction. The critical speed, where centrifugal force equals gravitational force, is the theoretical minimum speed for grinding. However, practical operation requires a speed slightly higher than the critical speed to ensure the balls cascade and grind effectively. Factors like ball size, material properties, and mill dimensions influence the optimal speed.
Key Points Explained:
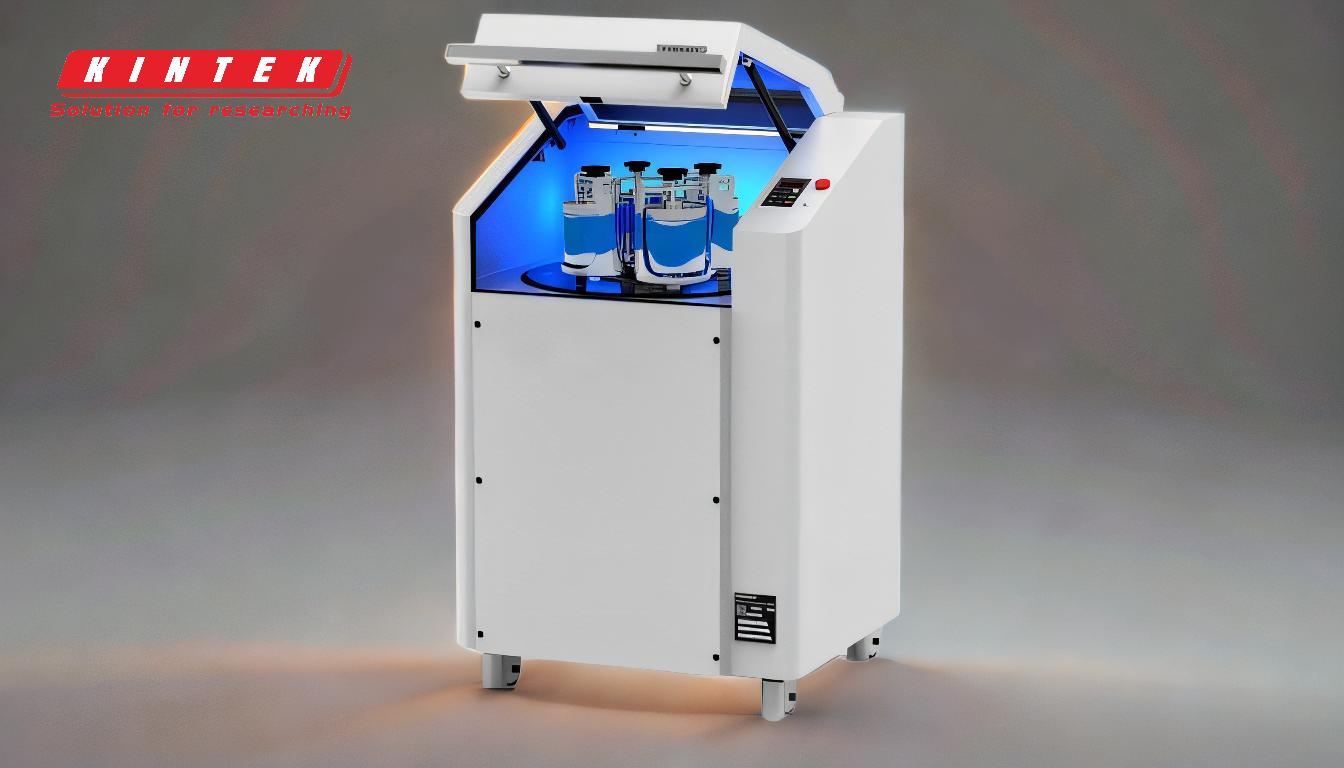
-
Critical Speed Concept:
- The critical speed of a ball mill is the speed at which the grinding balls begin to centrifuge, meaning they stick to the mill's inner wall due to centrifugal force. At this speed, grinding ceases because the balls are no longer cascading.
- Formula for critical speed:
[ N_c = \frac{42.3}{\sqrt{D}} ]
Where ( N_c ) is the critical speed in revolutions per minute (rpm), and ( D ) is the mill diameter in meters.
-
Minimum Operational Speed:
- The minimum operational speed of a ball mill is slightly higher than the critical speed. This ensures that the balls cascade and grind the material effectively.
- If the speed is too low (below critical speed), the balls slide or roll over each other, resulting in inefficient grinding and minimal size reduction.
-
Factors Influencing Minimum Speed:
- Mill Diameter: Larger mills require lower speeds to achieve the same cascading effect.
- Ball Size and Density: Heavier or larger balls may require higher speeds to cascade effectively.
- Material Properties: Harder or denser materials may require higher speeds for effective grinding.
- Filling Ratio: The percentage of the mill volume filled with grinding medium affects the cascading motion. Higher filling ratios may require adjustments to speed.
-
Practical Considerations:
- Operating a ball mill at or near the critical speed is impractical because grinding efficiency drops significantly.
- A common practice is to operate at 65-75% of the critical speed, ensuring a balance between grinding efficiency and energy consumption.
-
Impact of Speed on Grinding Efficiency:
- Low Speed: Balls slide or roll, leading to minimal size reduction and inefficient grinding.
- Optimal Speed: Balls cascade, creating impact and friction that maximize size reduction.
- High Speed: Balls centrifuge, sticking to the mill wall and preventing grinding.
-
Role of Other Factors:
- Residence Time: Longer residence times can compensate for lower speeds but may reduce throughput.
- Feed Rate and Level: Consistent feed rates and levels ensure steady grinding conditions.
- Mill Design: The ratio of drum diameter to length (L:D ratio) and the shape of the armor surface influence the optimal speed.
By understanding these factors, operators can determine the minimum speed required for effective grinding while balancing energy efficiency and productivity.
Summary Table:
Key Factor | Description |
---|---|
Critical Speed | Speed where centrifugal force equals gravitational force; grinding ceases. |
Minimum Operational Speed | Slightly higher than critical speed to ensure effective cascading and grinding. |
Factors Influencing Speed | Mill diameter, ball size, material properties, filling ratio, and mill design. |
Optimal Speed Range | 65-75% of critical speed for balanced grinding efficiency and energy use. |
Impact of Speed | Low speed: sliding/rolling; optimal speed: cascading; high speed: centrifuging. |
Need help optimizing your ball mill's performance? Contact our experts today for tailored solutions!