Biocompatibility is a critical factor when selecting materials for implants, as it determines how well the material interacts with the human body without causing adverse reactions. The most biocompatible materials for implants are those that exhibit excellent compatibility with biological tissues, resist corrosion, and minimize immune responses. Titanium and its alloys, such as Ti-6Al-4V, are widely regarded as the gold standard due to their exceptional biocompatibility, mechanical properties, and ability to osseointegrate. Other materials, including stainless steel, cobalt-chromium alloys, and certain ceramics like zirconia, also demonstrate good biocompatibility but may have limitations in specific applications. Polymers such as ultra-high-molecular-weight polyethylene (UHMWPE) and PEEK (polyether ether ketone) are also used for their flexibility and compatibility in non-load-bearing applications. The choice of material depends on the type of implant, its intended function, and the specific requirements of the patient.
Key Points Explained:
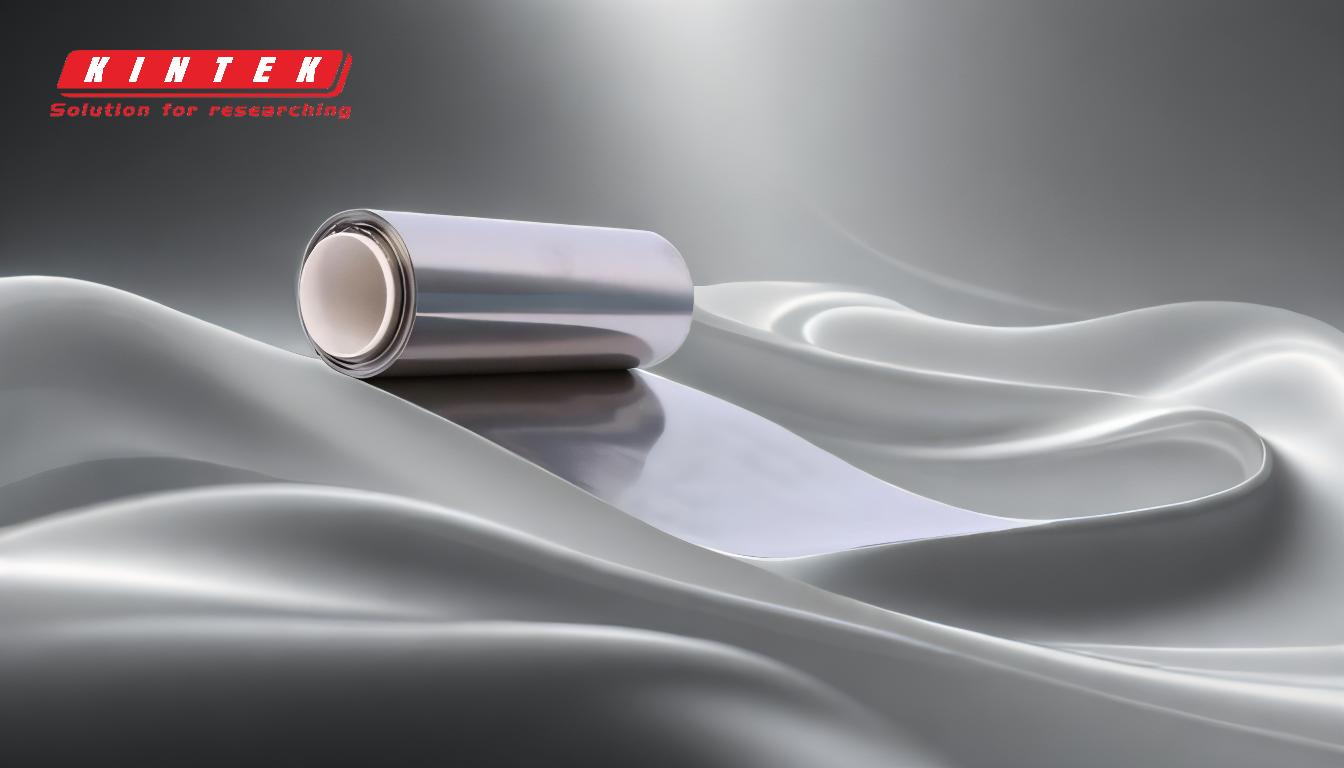
-
Definition of Biocompatibility:
- Biocompatibility refers to the ability of a material to perform with an appropriate host response in a specific application. For implants, this means the material should not elicit toxic, inflammatory, or immunogenic reactions and should support the intended function of the implant.
- The material must also resist degradation in the biological environment, ensuring long-term stability and performance.
-
Titanium and Its Alloys:
- Titanium is the most commonly used material for implants due to its excellent biocompatibility, corrosion resistance, and ability to integrate with bone (osseointegration).
- The alloy Ti-6Al-4V (titanium with 6% aluminum and 4% vanadium) is particularly popular for orthopedic and dental implants because of its high strength-to-weight ratio and fatigue resistance.
- Titanium's surface can be modified to enhance osseointegration, such as through roughening or coating with hydroxyapatite.
-
Stainless Steel and Cobalt-Chromium Alloys:
- Stainless steel (e.g., 316L) and cobalt-chromium alloys are also used in implants, particularly for their mechanical strength and wear resistance.
- However, these materials may release metal ions over time, which can lead to adverse reactions in some patients. They are often used in temporary implants or in applications where high strength is required.
-
Ceramics:
- Ceramics like zirconia and alumina are highly biocompatible and are often used in dental implants and joint replacements due to their excellent wear resistance and low friction.
- Zirconia, in particular, is valued for its aesthetic properties in dental applications and its ability to mimic the natural appearance of teeth.
-
Polymers:
- Polymers such as UHMWPE and PEEK are used in implants where flexibility and low weight are important. UHMWPE is commonly used in joint replacements, while PEEK is used in spinal implants and craniofacial reconstruction.
- These materials are less rigid than metals and ceramics, making them suitable for applications where mechanical stress is lower.
-
Considerations for Material Selection:
- The choice of material depends on the specific application and the patient's needs. For example, load-bearing implants like hip replacements require materials with high strength and wear resistance, while dental implants may prioritize aesthetics and osseointegration.
- Patient-specific factors, such as allergies or sensitivities to certain materials, must also be considered to ensure the best outcomes.
-
Future Trends in Biocompatible Materials:
- Research is ongoing to develop new materials with improved biocompatibility and functionality. For example, bioresorbable materials that gradually dissolve and are replaced by natural tissue are being explored for temporary implants.
- Surface modifications and nanotechnology are also being investigated to enhance the performance of existing materials and reduce the risk of complications.
In conclusion, titanium and its alloys remain the most biocompatible materials for implants due to their exceptional properties and proven track record in clinical applications. However, the choice of material should always be tailored to the specific requirements of the implant and the patient, with careful consideration of mechanical, biological, and aesthetic factors.
Summary Table:
Material Type | Key Features | Common Applications |
---|---|---|
Titanium & Alloys | Excellent biocompatibility, corrosion resistance, osseointegration | Orthopedic, dental implants |
Stainless Steel | High strength, wear resistance; may release metal ions over time | Temporary implants, high-strength |
Cobalt-Chromium | Mechanical strength, wear resistance; potential for adverse reactions | Joint replacements, dental |
Ceramics | High biocompatibility, wear resistance, low friction | Dental implants, joint replacements |
Polymers (e.g., UHMWPE, PEEK) | Flexibility, lightweight, low mechanical stress | Spinal implants, joint replacements |
Need help selecting the best biocompatible material for your implant? Contact our experts today for personalized guidance!