Vulcanization is a chemical process that converts natural rubber or related polymers into more durable materials by adding cross-links between polymer chains. The most commonly used vulcanizing agent is sulfur, which is widely employed due to its effectiveness and cost-efficiency. Sulfur-based vulcanization is the standard method for natural rubber and many synthetic rubbers, although it has limitations with certain synthetic polyolefins. The process typically involves heating the rubber with sulfur and accelerators to form cross-links, enhancing the material's strength, elasticity, and resistance to wear and temperature. Other vulcanization methods, such as press mold and injection moulding, are also used depending on the application and material requirements.
Key Points Explained:
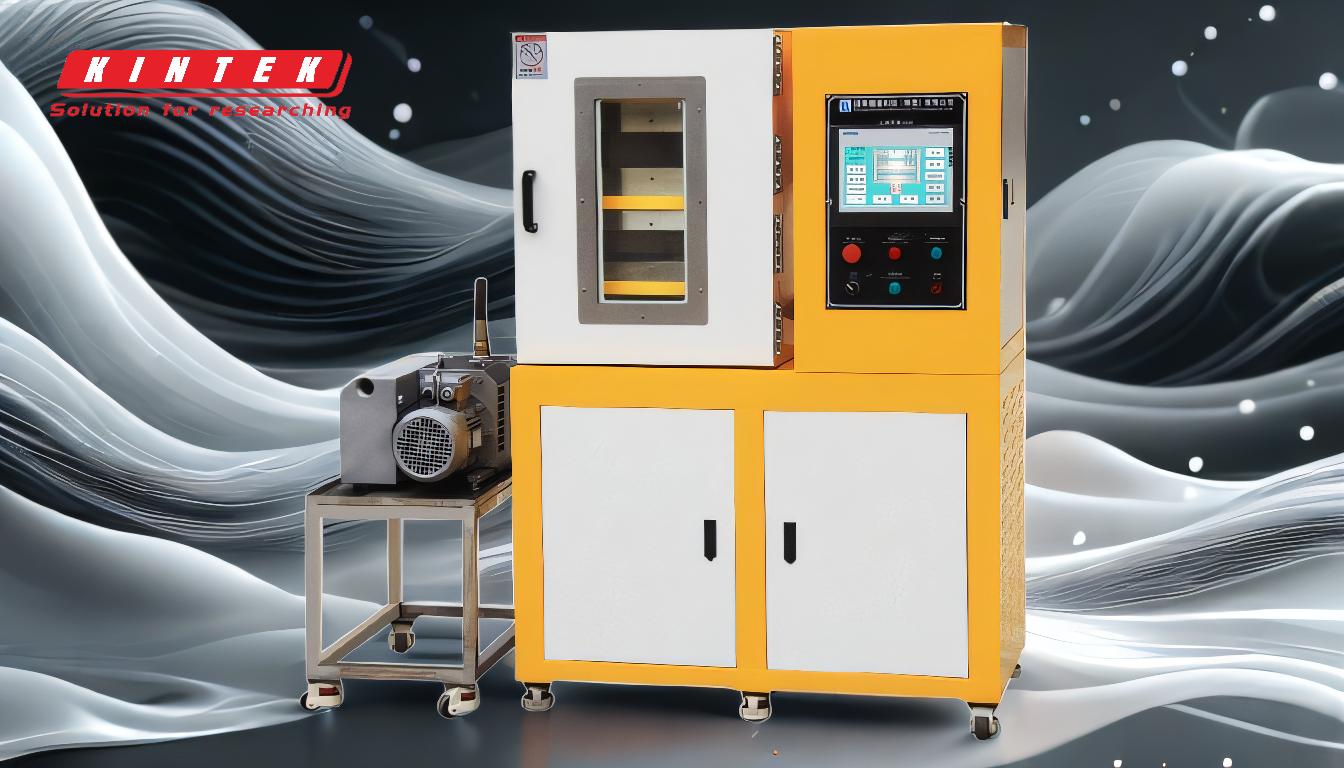
-
Sulfur as the Primary Vulcanizing Agent
- Sulfur is the most commonly used vulcanizing agent due to its ability to form strong cross-links between polymer chains in rubber.
- It is cost-effective and widely available, making it the standard choice for natural rubber and many synthetic rubbers.
- However, sulfur alone is a slow vulcanizing agent and often requires accelerators to speed up the process.
-
Limitations of Sulfur in Vulcanization
- Sulfur is not effective for vulcanizing synthetic polyolefins, as these materials lack the necessary reactive sites for sulfur to form cross-links.
- This limitation necessitates the use of alternative vulcanizing agents or methods for certain synthetic rubbers.
-
Vulcanization Methods
-
Compression Moulding:
- Involves placing uncured rubber between heated moulds and applying pressure to shape and vulcanize the material simultaneously.
- Suitable for producing large, simple-shaped rubber components.
-
Injection Moulding:
- Preheated rubber is forced into a mould cavity using a rotating screw, allowing for precise shaping and vulcanization.
- Ideal for complex geometries and high-volume production.
-
Compression Moulding:
-
Role of Accelerators in Sulfur Vulcanization
- Accelerators are added to sulfur-based vulcanization to reduce curing time and improve the efficiency of cross-linking.
- Common accelerators include thiazoles, sulfenamides, and guanidines, which enhance the vulcanization process without compromising the material's properties.
-
Applications of Vulcanized Rubber
- Vulcanized rubber is used in a wide range of industries, including automotive (tires, seals), construction (gaskets, hoses), and consumer goods (footwear, sporting equipment).
- The enhanced durability and elasticity of vulcanized rubber make it suitable for demanding applications.
-
Alternative Vulcanizing Agents
- For materials where sulfur is ineffective, alternative vulcanizing agents such as peroxides, metal oxides, or radiation-based methods are used.
- These methods are tailored to specific polymer types and application requirements.
-
Environmental and Safety Considerations
- Sulfur vulcanization is generally safe but requires proper handling to avoid exposure to harmful by-products like hydrogen sulfide.
- Efforts are ongoing to develop more environmentally friendly vulcanization methods, such as using bio-based accelerators or reducing sulfur content.
By understanding these key points, a purchaser of equipment or consumables can make informed decisions about the appropriate vulcanizing methods and materials for their specific needs.
Summary Table:
Key Aspect | Details |
---|---|
Primary Vulcanizing Agent | Sulfur, cost-effective and widely used for natural and synthetic rubbers. |
Limitations of Sulfur | Ineffective for synthetic polyolefins; requires alternative methods. |
Vulcanization Methods | Compression moulding for large parts; injection moulding for complex shapes. |
Role of Accelerators | Speed up curing and improve cross-linking efficiency. |
Applications | Automotive, construction, and consumer goods industries. |
Alternative Agents | Peroxides, metal oxides, or radiation for sulfur-incompatible materials. |
Environmental Considerations | Safe with proper handling; eco-friendly methods in development. |
Discover the best vulcanization solutions for your needs— contact our experts today !