The opening sequence of a 3-plate mold involves a series of controlled movements to separate the mold plates and eject the molded product along with the runner system. This process is critical for ensuring proper part ejection and efficient mold operation. The sequence typically includes three main stages: the runner opening, the runner stripper plate opening, and the product opening. Each stage is carefully timed and coordinated to allow the mold to release the runner system and the final product without causing damage or deformation. The design of the 3-plate mold incorporates separation lines that facilitate these movements, ensuring smooth operation and high-quality part production.
Key Points Explained:
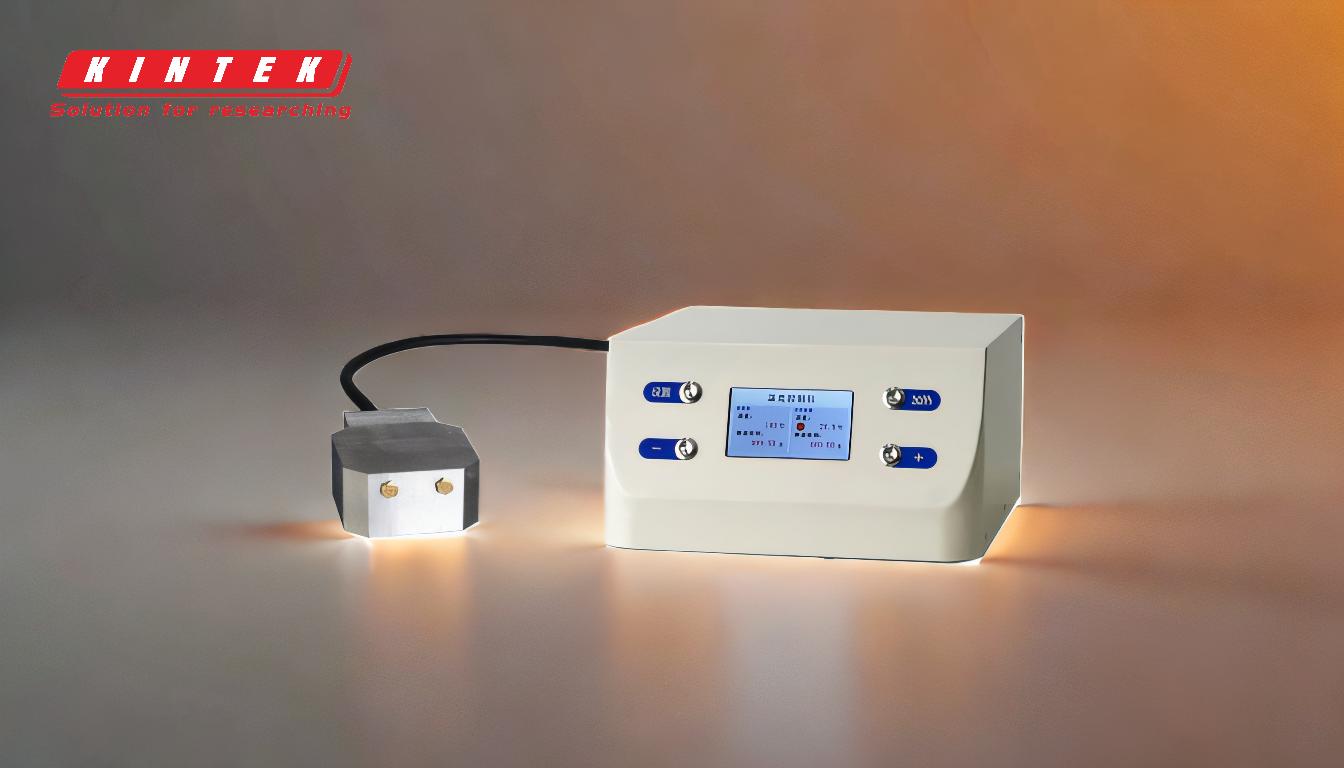
-
Runner Opening:
- The first stage in the opening sequence involves the separation of the runner system from the mold.
- This step ensures that the runner, which channels molten plastic into the mold cavity, is detached cleanly and prepared for ejection.
- The runner opening is typically achieved by the movement of the mold plates, allowing the runner to be released from the stationary side of the mold.
-
Runner Stripper Plate Opening:
- After the runner is separated, the runner stripper plate comes into action.
- The stripper plate is designed to push the runner system out of the mold, ensuring it is fully ejected and does not interfere with the next cycle.
- This step is crucial for maintaining the efficiency of the mold and preventing any residual runner material from causing issues in subsequent injections.
-
Product Opening:
- The final stage involves the separation of the molded product from the mold cavity.
- This step ensures that the product is ejected cleanly and without damage, ready for further processing or packaging.
- The product opening is typically coordinated with the movement of ejector pins or other ejection mechanisms to ensure smooth and consistent part release.
-
Separation Lines:
- The design of the 3-plate mold includes specific separation lines that facilitate the controlled movement of the mold plates.
- These separation lines are strategically placed to allow for the sequential opening of the mold, ensuring that each stage of the opening sequence is executed smoothly and without interference.
- The separation lines also play a role in maintaining the alignment of the mold plates, which is critical for the precision and quality of the molded parts.
-
Importance of Timing and Coordination:
- The opening sequence of a 3-plate mold requires precise timing and coordination to ensure that each stage is executed correctly.
- Any misalignment or delay in the sequence can result in incomplete ejection, part damage, or mold wear, which can negatively impact the overall efficiency and quality of the molding process.
- Proper maintenance and adjustment of the mold are essential to ensure that the opening sequence remains consistent and reliable over time.
By understanding and optimizing the opening sequence of a 3-plate mold, manufacturers can achieve higher production efficiency, better part quality, and reduced downtime, making it a critical aspect of injection molding operations.
Summary Table:
Stage | Description |
---|---|
Runner Opening | Separates the runner system from the mold for clean ejection. |
Runner Stripper Plate | Pushes the runner system out to prevent interference in the next cycle. |
Product Opening | Ejects the molded product cleanly using ejector pins or mechanisms. |
Separation Lines | Facilitates controlled plate movement and ensures alignment for precision. |
Timing & Coordination | Ensures smooth execution of each stage to avoid damage or inefficiency. |
Optimize your 3-plate mold operation for better efficiency and quality—contact our experts today!