The performance of a ball mill is influenced by a variety of factors, including the speed of rotation, the size and type of grinding medium, the characteristics of the material to be ground, and the filling ratio of the mill. The degree of milling is affected by the residence time of the material in the mill chamber, the size, density, and number of balls, the hardness of the grinding material, the feed rate, and the rotation speed of the cylinder. Productivity is also dependent on drum diameter, the ratio of drum diameter to length, physical-chemical properties of the feed material, ball filling and sizes, armor surface shape, rotation speed, milling fineness, and the timely removal of the ground product. Understanding these factors helps in optimizing the performance of a ball mill for specific grinding tasks.
Key Points Explained:
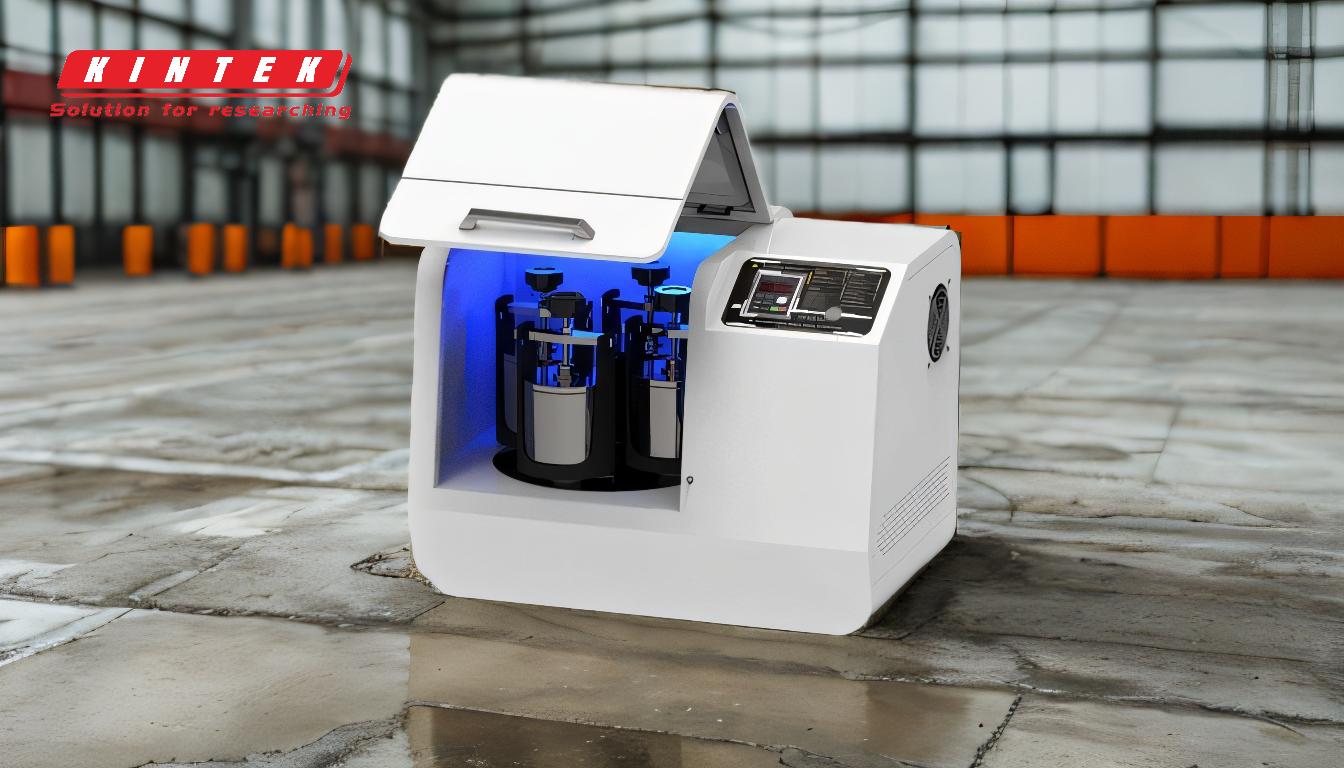
-
Speed of Rotation:
- The speed at which the ball mill rotates is crucial for its performance. If the rotation speed is too low, the balls will not be lifted high enough to generate significant impact energy, resulting in poor grinding efficiency. Conversely, if the speed is too high, the balls may centrifuge, reducing grinding effectiveness. The optimal rotation speed ensures that the balls cascade and impact the material effectively.
-
Size and Type of Grinding Medium:
- The size and type of balls used in the mill significantly affect the grinding process. Larger balls are more effective at breaking down coarse materials, while smaller balls are better suited for fine grinding. The material of the balls (e.g., steel, ceramic) also influences wear resistance and grinding efficiency.
-
Characteristics of the Material to be Ground:
- The hardness, size, and type of material being ground play a critical role in the performance of the ball mill. Harder materials require more energy to grind, while softer materials may be ground more easily. The feed size and the desired fineness of the product also determine the grinding efficiency.
-
Filling Ratio of the Mill:
- The filling ratio, or the percentage of the mill volume filled with grinding medium, affects the grinding performance. An optimal filling ratio ensures that there is enough space for the balls to move and impact the material effectively. Overfilling or underfilling the mill can lead to reduced grinding efficiency.
-
Residence Time of Material in the Mill Chamber:
- The amount of time the material spends in the mill chamber influences the degree of milling. Longer residence times allow for more thorough grinding, but excessive residence times can lead to overgrinding and energy wastage.
-
Feed Rate and Level in the Vessel:
- The rate at which material is fed into the mill and the level of material in the vessel affect the grinding process. Consistent feed rates and optimal material levels ensure steady grinding conditions and prevent overloading or underloading the mill.
-
Drum Diameter and Length-to-Diameter Ratio:
- The diameter of the drum and the ratio of its length to diameter (L:D ratio) are critical for the productivity of the ball mill. An optimal L:D ratio (typically 1.56–1.64) ensures efficient grinding by balancing the volume of material being processed with the energy input.
-
Physical-Chemical Properties of Feed Material:
- The physical and chemical properties of the feed material, such as hardness, density, and moisture content, influence the grinding process. These properties determine the energy required for grinding and the wear on the grinding medium.
-
Armor Surface Shape:
- The shape of the mill's internal armor or lining affects the movement of the grinding medium and the material. Smooth linings may reduce wear but can also reduce grinding efficiency, while ribbed or lifter linings can enhance the lifting and cascading of the balls.
-
Rotation Speed:
- The rotation speed of the mill cylinder must be carefully controlled to ensure optimal grinding conditions. The critical speed is the point at which the centrifugal force equals the gravitational force on the balls, and operating near this speed can maximize grinding efficiency.
-
Milling Fineness:
- The desired fineness of the ground product influences the grinding process. Finer products require more energy and longer grinding times, while coarser products can be achieved more quickly.
-
Timely Removal of Ground Product:
- Efficient removal of the ground product from the mill is essential to maintain optimal grinding conditions. Delayed removal can lead to overgrinding and energy inefficiency, while prompt removal ensures consistent product quality and mill performance.
By understanding and optimizing these factors, the performance of a ball mill can be significantly enhanced, leading to more efficient and effective grinding processes.
Summary Table:
Factor | Impact on Performance |
---|---|
Speed of Rotation | Ensures optimal ball cascading and impact energy for effective grinding. |
Size and Type of Grinding Medium | Larger balls for coarse grinding; smaller balls for fine grinding. Material affects wear. |
Material Characteristics | Hardness, size, and type determine grinding energy and efficiency. |
Filling Ratio of the Mill | Optimal filling ensures effective ball movement; over/underfilling reduces efficiency. |
Residence Time | Longer times improve grinding but can lead to overgrinding and energy waste. |
Feed Rate and Level | Consistent rates and levels prevent overloading and ensure steady grinding. |
Drum Diameter and L:D Ratio | Optimal ratio (1.56–1.64) balances material volume and energy input. |
Physical-Chemical Properties | Hardness, density, and moisture affect energy needs and wear. |
Armor Surface Shape | Ribbed or lifter linings enhance ball movement and grinding efficiency. |
Rotation Speed | Critical speed maximizes grinding efficiency by balancing forces. |
Milling Fineness | Finer products require more energy and longer grinding times. |
Timely Product Removal | Ensures consistent quality and prevents overgrinding. |
Ready to optimize your ball mill performance? Contact our experts today for tailored solutions!