The sputtering process is a physical vapor deposition (PVD) technique used to deposit thin films onto substrates. It involves bombarding a target material with high-energy ions, typically from an inert gas like argon, which causes atoms to be ejected from the target's surface. These ejected atoms then travel through a vacuum and deposit onto a substrate, forming a thin, uniform film. The process is highly precise and is widely used in industries such as semiconductors, optics, and coatings due to its ability to produce high-quality, durable films with excellent adhesion and uniformity.
Key Points Explained:
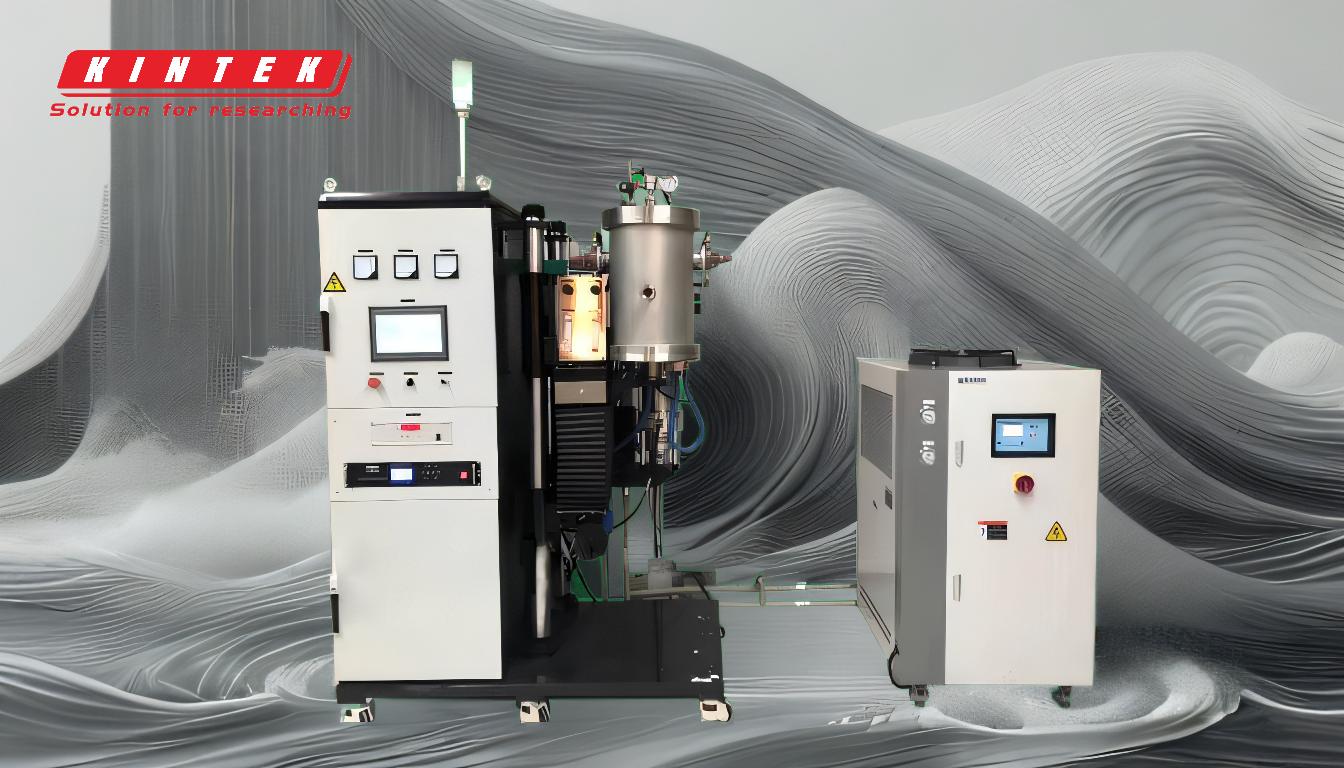
-
Ion Bombardment:
- The sputtering process begins with the generation of a plasma, typically using an inert gas like argon. This gas is ionized to produce positively charged ions.
- These ions are then accelerated toward the target material, which is negatively charged, creating a strong electric field that drives the ions to the target surface.
- The impact of these high-energy ions on the target surface transfers kinetic energy to the target atoms, causing them to be ejected from the surface.
-
Ejection of Target Atoms:
- When the ions strike the target surface, they transfer enough energy to dislodge atoms from the target material. This process is known as sputtering.
- The ejected atoms are neutral and travel through the vacuum chamber toward the substrate.
- The energy of the ions and the angle of impact determine the efficiency and rate of sputtering.
-
Deposition onto Substrate:
- The ejected atoms travel through the vacuum and deposit onto the substrate, where they condense to form a thin film.
- The substrate can be positioned at various angles and distances from the target to control the thickness and uniformity of the deposited film.
- The adhesion and quality of the film depend on factors such as the energy of the deposited atoms, the cleanliness of the substrate, and the vacuum conditions.
-
Magnetron Sputtering:
- In magnetron sputtering, a magnetic field is used to enhance the ionization of the gas and increase the density of the plasma.
- The magnetic field traps electrons near the target surface, increasing the likelihood of collisions between electrons and gas atoms, which in turn increases the ion density.
- This results in a more efficient sputtering process, allowing for higher deposition rates and better film quality.
-
Applications of Sputtering:
- The sputtering process is used in a wide range of applications, including the production of thin films for semiconductors, optical coatings, and protective coatings.
- It is particularly valued for its ability to deposit a wide variety of materials, including metals, alloys, and ceramics, with high precision and uniformity.
- The process is also used in the production of hard coatings, such as those used in cutting tools, to improve wear resistance and durability.
-
Advantages of Sputtering:
- Sputtering offers several advantages over other thin film deposition techniques, including excellent film uniformity, high adhesion, and the ability to deposit complex materials.
- The process can be performed at relatively low temperatures, making it suitable for temperature-sensitive substrates.
- Sputtering is also highly scalable, making it suitable for both small-scale laboratory research and large-scale industrial production.
-
Challenges and Considerations:
- One of the main challenges of sputtering is the need for a high vacuum, which can increase the complexity and cost of the equipment.
- The process can also be relatively slow compared to other deposition techniques, particularly for thick films.
- Careful control of process parameters, such as gas pressure, power, and substrate temperature, is required to achieve the desired film properties.
In summary, the sputtering process is a versatile and precise method for depositing thin films, with applications ranging from electronics to optical coatings. Its ability to produce high-quality, uniform films with excellent adhesion makes it a valuable tool in modern manufacturing and research.
Summary Table:
Key Aspect | Details |
---|---|
Process | Physical vapor deposition (PVD) using high-energy ions to eject target atoms. |
Main Steps | Ion bombardment, ejection of target atoms, and deposition onto substrate. |
Applications | Semiconductors, optical coatings, protective coatings, and hard coatings. |
Advantages | High film uniformity, excellent adhesion, and low-temperature processing. |
Challenges | Requires high vacuum, can be slow for thick films, and needs precise control. |
Discover how sputtering can enhance your manufacturing process—contact our experts today!