The principle of a vacuum system revolves around the removal of air, gases, and other molecules from a vacuum chamber to create a low-pressure environment. This is achieved through a combination of pumps, valves, and other components working together to evacuate the chamber. The system operates over a wide pressure range, with higher vacuum pumps removing molecules from the outlet side as pressure decreases. Key components include mechanical pumps, diffusion pumps, rotary vane holding pumps, and electropneumatic valves, which collectively ensure efficient and controlled evacuation of the chamber.
Key Points Explained:
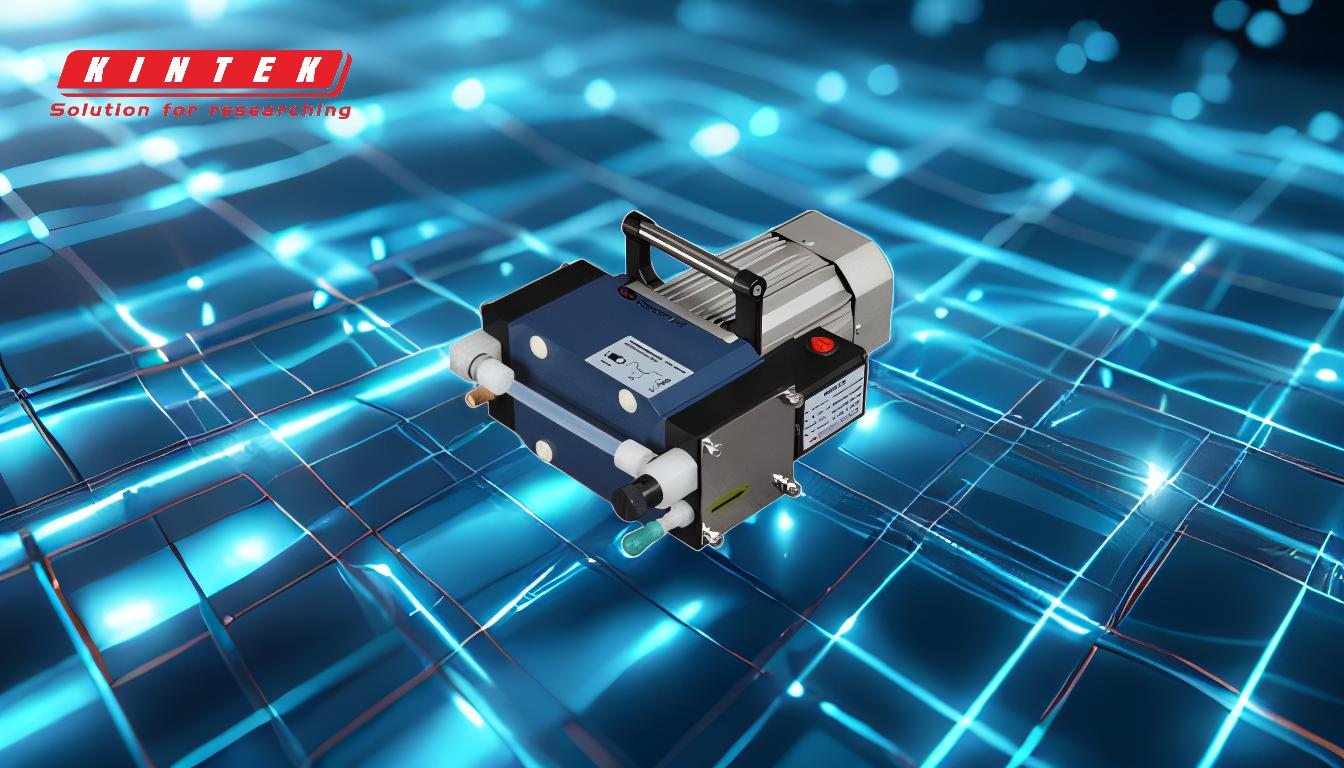
-
Basic Operating Principle:
- The fundamental principle of a vacuum system is to remove air, gases, and other molecules from a vacuum chamber to create a low-pressure environment.
- This process becomes increasingly challenging as the pressure decreases, requiring the system to operate over a wide pressure range, typically from 1.3 to 13.3 mbar.
-
Components of a Vacuum System:
- Mechanical Pumps: These are used for initial roughing and include a combination of roughing pumps and boosters. They are responsible for the initial evacuation of the chamber.
- Diffusion Pumps: These pumps use Dow Corning fluid to create a high vacuum by removing molecules from the outlet side. They are effective in achieving lower pressures.
- Rotary Vane Holding Pumps: These pumps maintain the vacuum level once it has been achieved, ensuring stability in the system.
- Right Angle Poppet Valves: These valves, operated electropneumatically, control the flow of gases and ensure the system operates efficiently.
- Partial Pressure Capabilities: The system can handle inert gases like argon or nitrogen, allowing for controlled environments when necessary.
-
Pressure Range and Challenges:
- The system must operate over a wide pressure range to effectively remove molecules from the chamber.
- As pressure decreases, removing additional molecules becomes more difficult, requiring more sophisticated pumping mechanisms and precise control.
-
Series Configuration:
- Higher vacuum pumps are often linked in a series to enhance the evacuation process. This configuration allows for the removal of molecules from the outlet side, improving the overall efficiency of the system.
-
Importance of Controlled Environments:
- The ability to handle inert gases like argon or nitrogen is crucial for applications requiring controlled environments. This feature ensures that the vacuum system can be used in a variety of industrial and scientific applications.
-
Electropneumatic Operation:
- The use of electropneumatic valves allows for precise control over the flow of gases within the system. This precision is essential for maintaining the desired vacuum level and ensuring the system operates efficiently.
In summary, the principle of a vacuum system involves the removal of air and gases from a chamber to create a low-pressure environment. This is achieved through a combination of mechanical and diffusion pumps, rotary vane holding pumps, and electropneumatic valves. The system operates over a wide pressure range and can handle inert gases, making it versatile for various applications. The series configuration of higher vacuum pumps enhances efficiency, while electropneumatic operation ensures precise control over the system.
Summary Table:
Component | Function |
---|---|
Mechanical Pumps | Initial roughing and evacuation of the chamber. |
Diffusion Pumps | Achieve high vacuum using Dow Corning fluid. |
Rotary Vane Holding Pumps | Maintain vacuum levels for system stability. |
Right Angle Poppet Valves | Electropneumatic control of gas flow for efficient operation. |
Partial Pressure Capabilities | Handle inert gases like argon or nitrogen for controlled environments. |
Discover how a vacuum system can optimize your applications—contact us today for expert guidance!