Plasma sputtering is a highly controlled thin film deposition process used to coat substrates with ultra-high purity materials. The process involves creating a plasma by ionizing a noble gas, typically Argon, within a vacuum chamber. The ions in the plasma are accelerated towards a target material, causing atoms to be ejected from the target due to momentum transfer. These ejected atoms then travel through the vacuum and deposit onto a substrate, forming a thin film. The process requires precise control of pressure, temperature, and voltage to ensure the purity and quality of the deposited film. Key steps include creating a vacuum, introducing Argon gas, ionizing the gas to form plasma, and using magnetic fields to direct the ions towards the target.
Key Points Explained:
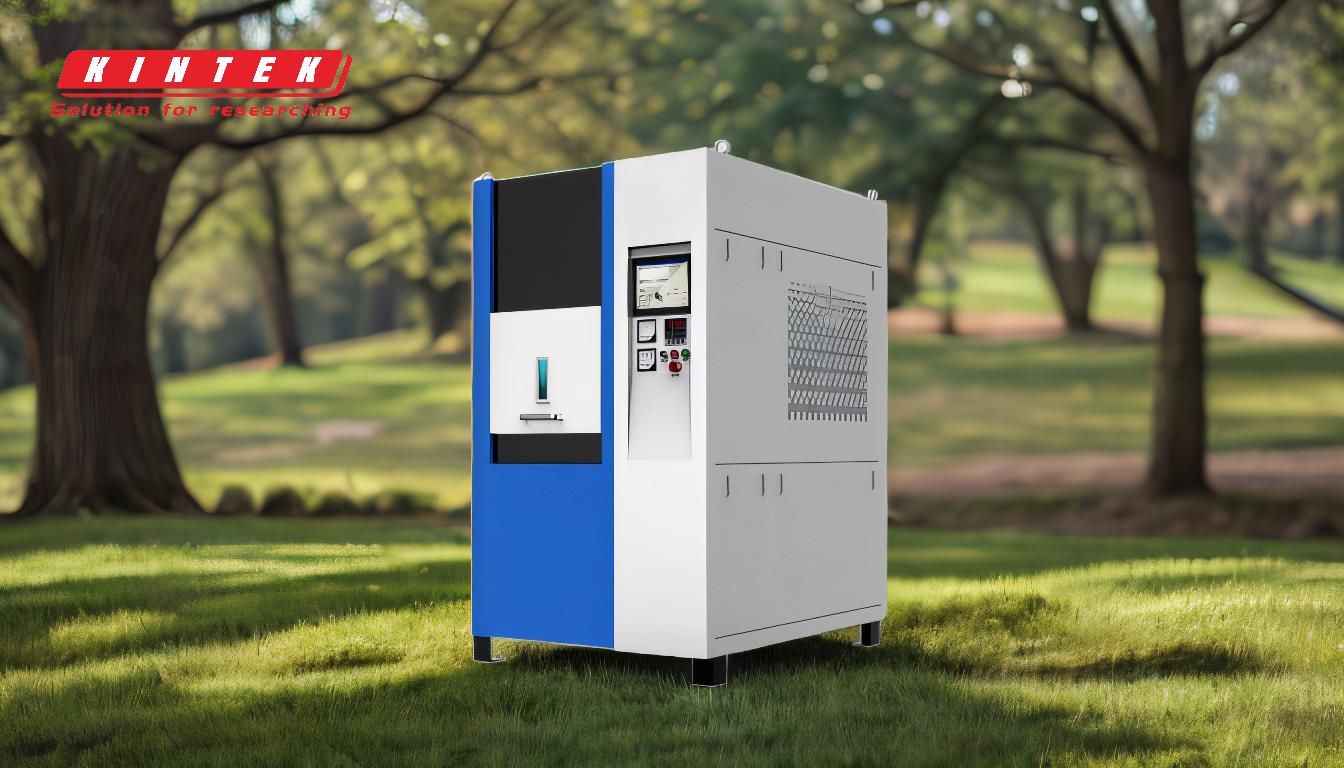
-
Creation of a Vacuum Environment:
- The first step in plasma sputtering is to evacuate the reaction chamber to a very low pressure, typically around 1 Pa (0.0000145 psi). This is crucial to remove any moisture and impurities that could contaminate the thin film.
- A high vacuum ensures that the sputtered atoms travel unimpeded to the substrate, maintaining the purity and integrity of the deposited material.
-
Introduction of Inert Gas:
- Once the vacuum is established, an inert gas, usually Argon, is introduced into the chamber. Argon is preferred because it is chemically inert and does not react with the target material or the substrate.
- The pressure of the Argon gas is carefully controlled, typically in the range of 10-1 to 10-3 mbar, to create the right conditions for plasma formation.
-
Formation of Plasma:
- Plasma is created by ionizing the Argon gas. This is achieved by applying a high voltage (3-5 kV) across the chamber, which ionizes the Argon atoms, creating a plasma composed of Ar+ ions, electrons, and neutral atoms.
- The plasma is sustained by continuously supplying energy, either through direct current (DC) or radio frequency (RF) excitation. This energy keeps the Argon atoms ionized and maintains the plasma state.
-
Ion Bombardment of the Target:
- The Ar+ ions in the plasma are accelerated towards the target material due to the applied electric field. When these high-energy ions collide with the target, they transfer their kinetic energy to the target atoms.
- This energy transfer causes a cascade of collisions within the target material, leading to the ejection of atoms from the target surface. This process is known as sputtering.
-
Transport of Sputtered Atoms:
- The ejected atoms from the target material travel through the vacuum chamber towards the substrate. The vacuum environment ensures that the atoms do not collide with other gas molecules, allowing them to deposit uniformly on the substrate.
- The distance between the target and the substrate, as well as the pressure within the chamber, are carefully controlled to optimize the deposition process.
-
Deposition on the Substrate:
- The sputtered atoms condense on the substrate, forming a thin film. The properties of the film, such as thickness, uniformity, and adhesion, depend on various factors including the energy of the sputtered atoms, the substrate temperature, and the deposition rate.
- The substrate is often heated to temperatures ranging from 150°C to 750°C to improve the quality of the deposited film, such as enhancing adhesion and reducing stress.
-
Role of Magnetic Fields:
- In some sputtering systems, a magnetic field is applied to confine the plasma and increase the density of ions near the target. This is known as magnetron sputtering and is used to enhance the sputtering rate and improve the efficiency of the process.
- The magnetic field helps to trap electrons near the target, increasing the ionization of the Argon gas and thus the number of Ar+ ions available for sputtering.
-
Control of Process Parameters:
- The success of the plasma sputtering process depends on the precise control of several parameters, including the vacuum pressure, Argon gas pressure, applied voltage, substrate temperature, and magnetic field strength.
- These parameters are carefully optimized to achieve the desired film properties, such as thickness, uniformity, and adhesion, while minimizing defects and contamination.
In summary, plasma sputtering is a complex but highly controlled process that involves creating a plasma, bombarding a target material with ions, and depositing the ejected atoms onto a substrate to form a thin film. The process requires careful management of vacuum conditions, gas pressure, temperature, and electric and magnetic fields to ensure the quality and purity of the deposited film.
Summary Table:
Step | Description |
---|---|
1. Creation of a Vacuum | Evacuate the chamber to ~1 Pa to remove impurities and ensure a clean environment. |
2. Introduction of Argon | Introduce inert Argon gas at controlled pressures (10-1 to 10-3 mbar). |
3. Formation of Plasma | Ionize Argon gas using high voltage (3-5 kV) to create a plasma. |
4. Ion Bombardment | Accelerate Ar+ ions to sputter target material atoms. |
5. Transport of Atoms | Sputtered atoms travel through vacuum to the substrate. |
6. Deposition on Substrate | Atoms condense to form a thin film with controlled thickness and adhesion. |
7. Magnetic Fields | Use magnetic fields to enhance sputtering efficiency (magnetron sputtering). |
8. Process Control | Optimize vacuum, gas pressure, temperature, and voltage for high-quality films. |
Discover how plasma sputtering can revolutionize your material coating process—contact our experts today!