Sputter coating is a physical vapor deposition (PVD) technique used to deposit thin, uniform coatings of materials onto substrates. The process involves creating a plasma by electrically charging a sputtering cathode, which bombards a target material with high-energy ions. This bombardment ejects atoms from the target, which then deposit onto the substrate to form a thin film. The process requires a vacuum environment, specialized gases like argon or oxygen, and often uses magnets to ensure uniform erosion of the target material. Sputter coating is widely used in applications such as improving secondary electron emission in Scanning Electron Microscopy (SEM) and creating durable, high-quality coatings in various industries.
Key Points Explained:
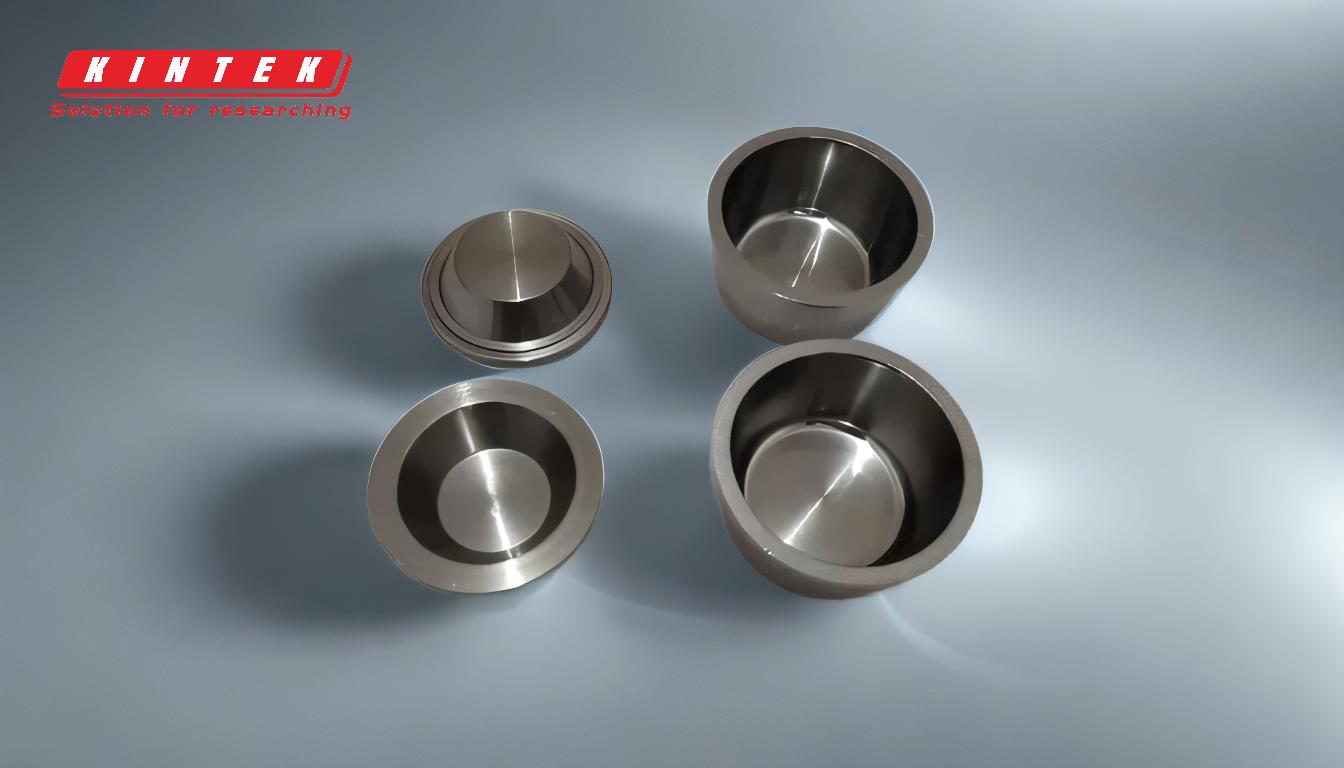
-
Overview of Sputter Coating:
- Sputter coating is a PVD process where a target material is bombarded with high-energy ions, causing atoms to be ejected and deposited onto a substrate.
- The process is used to create thin, uniform coatings that improve surface properties such as conductivity, durability, and resistance to wear.
-
Key Components of the Sputter Coating Process:
- Target Material: The material to be coated onto the substrate, often a metal or ceramic.
- Substrate: The surface onto which the coating is applied.
- Sputtering Cathode: Electrically charged to create a plasma.
- Plasma: A high-energy state of matter formed by ionizing gas, which bombards the target material.
- Vacuum Chamber: Maintains a low-pressure environment to facilitate the process.
- Process Gases: Typically argon or oxygen, used to create the plasma.
-
Step-by-Step Process of Sputter Coating:
-
Step 1: Preparation:
- The substrate is cleaned and placed in the sputtering chamber.
- The chamber is evacuated to achieve the required vacuum level.
- Process gases (argon or oxygen) are introduced and cleaned to maintain coating composition.
-
Step 2: Plasma Formation:
- A sputtering cathode is electrically charged, forming a plasma.
- The plasma bombards the target material with high-energy ions.
-
Step 3: Sputtering:
- The bombardment causes atoms to be ejected from the target material.
- Magnets are often used to ensure stable and uniform erosion of the target material.
-
Step 4: Deposition:
- Ejected atoms travel through the vacuum and deposit onto the substrate.
- A shutter may be used to control when the substrate is exposed to the free atoms.
-
Step 5: Bonding:
- High-energy target material impacts the substrate, forming a strong atomic-level bond.
-
Step 1: Preparation:
-
Advantages of Sputter Coating:
- Uniformity: The process produces thin, even coatings.
- Versatility: Can be used with a wide range of materials, including metals, ceramics, and composites.
- Strong Adhesion: The atomic-level bonding ensures durable coatings.
- Improved Surface Properties: Enhances conductivity, reduces thermal damage, and improves secondary electron emission in SEM.
-
Applications of Sputter Coating:
- Electronics: Used in the production of semiconductors, thin-film transistors, and solar cells.
- Optics: Applied to create anti-reflective coatings and mirrors.
- Automotive: Used for wear-resistant coatings on engine components.
- Medical Devices: Provides biocompatible coatings on implants.
- Research and Development: Essential for preparing samples for SEM and other analytical techniques.
-
Challenges and Considerations:
- Heat Management: The process generates significant heat, requiring specialized chilling systems.
- Vacuum Requirements: High vacuums are necessary, which can be energy-intensive.
- Material Compatibility: Not all materials are suitable for sputtering, and some may require specific conditions or pre-treatments.
- Cost: The equipment and operational costs can be high, particularly for large-scale or specialized applications.
In summary, sputter coating is a highly controlled and versatile process that leverages plasma physics to deposit thin, uniform coatings onto substrates. Its applications span multiple industries, and while it presents some challenges, its benefits in terms of coating quality and durability make it a valuable technique in modern manufacturing and research.
Summary Table:
Aspect | Details |
---|---|
Process | Physical vapor deposition (PVD) using high-energy ions to eject target atoms. |
Key Components | Target material, substrate, sputtering cathode, plasma, vacuum chamber, gases. |
Advantages | Uniform coatings, strong adhesion, improved conductivity, and durability. |
Applications | Electronics, optics, automotive, medical devices, and SEM sample preparation. |
Challenges | Heat management, vacuum requirements, material compatibility, and cost. |
Discover how sputter coating can enhance your projects—contact our experts today!