Sputtering is a physical vapor deposition (PVD) technique used to deposit thin films of materials onto substrates. The process involves creating a vacuum environment, introducing an inert gas (typically argon), ionizing the gas to form plasma, and bombarding a target material with the ionized gas. This bombardment ejects atoms from the target, which then travel through the vacuum and deposit onto a substrate, forming a thin film. The process is highly controlled and allows for precise manipulation of film properties such as thickness, morphology, and composition. It is widely used in industries like semiconductors, optics, and coatings due to its accuracy and versatility.
Key Points Explained:
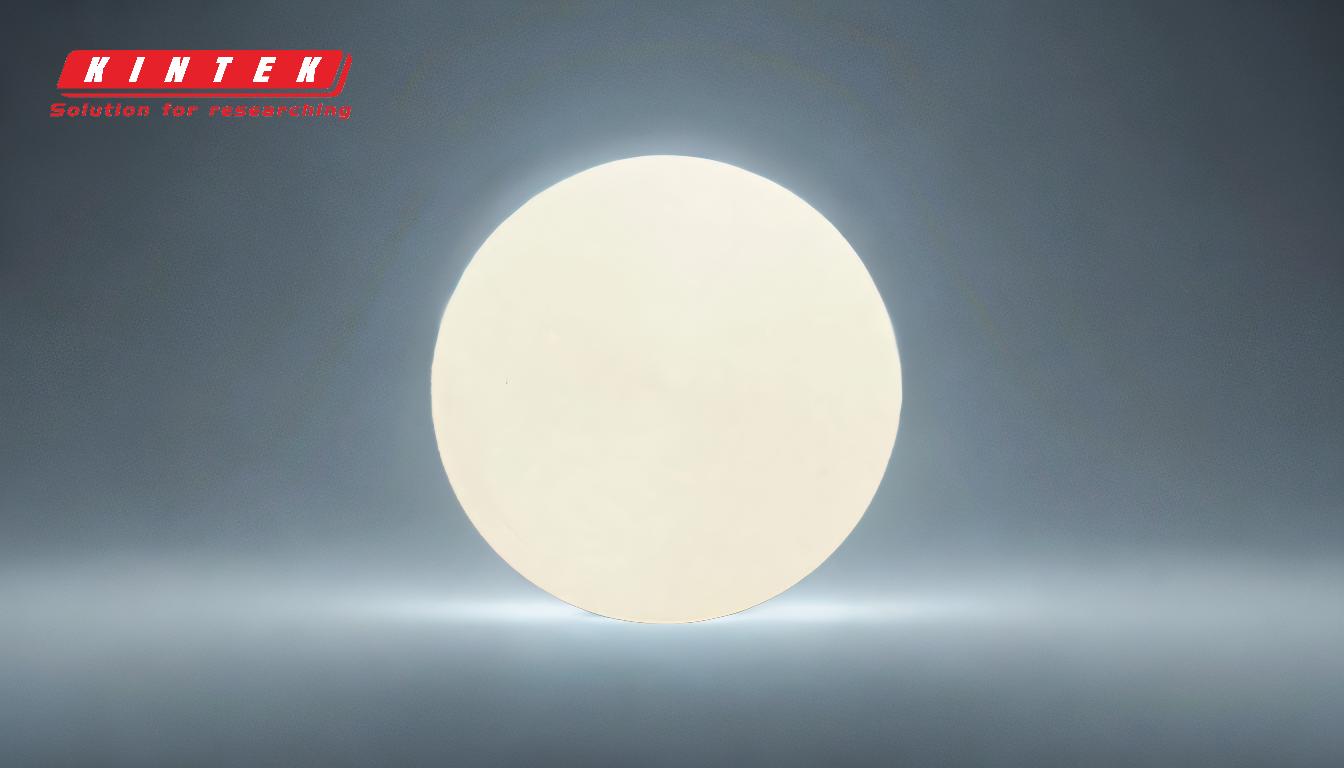
-
Vacuum Chamber Setup:
- The sputtering process begins by placing the target material (source) and the substrate (destination) inside a vacuum chamber.
- The chamber is evacuated to a low pressure (around 1 Pa or lower) to remove moisture, impurities, and other contaminants that could interfere with the deposition process.
- This vacuum environment ensures that the sputtered particles travel unimpeded to the substrate.
-
Introduction of Inert Gas:
- Once the vacuum is established, an inert gas (usually argon) is introduced into the chamber at a controlled pressure (10^-1 to 10^-3 mbar).
- Argon is preferred because it is chemically inert, reducing the risk of unwanted reactions during the sputtering process.
-
Creation of Plasma:
- A high voltage (3-5 kV) is applied between the target (cathode) and the substrate (anode), ionizing the argon gas and creating a plasma.
- The plasma consists of positively charged argon ions (Ar+) and free electrons.
- A magnetic field is often used to confine the plasma around the target, increasing the efficiency of the sputtering process.
-
Bombardment of the Target:
- The positively charged argon ions are accelerated toward the negatively charged target due to the electric field.
- When these high-energy ions collide with the target, they transfer their kinetic energy to the target atoms, ejecting them from the surface in a process called "sputtering."
- The ejected atoms are typically in a neutral state and travel through the vacuum chamber toward the substrate.
-
Deposition on the Substrate:
- The sputtered atoms travel in a line-of-sight trajectory and condense onto the substrate, forming a thin film.
- The substrate may be heated (150–750°C) to improve adhesion and film quality.
- The deposition process is highly controlled, allowing for precise manipulation of film thickness, grain size, and orientation.
-
Control Over Film Properties:
- The sputtering process enables the creation of films with specific properties, such as reflectivity, electrical resistivity, or ionic resistivity.
- By adjusting parameters like gas pressure, voltage, and substrate temperature, the morphology, density, and composition of the film can be tailored to meet specific requirements.
-
Applications of Sputtering:
- Sputtering is widely used in industries such as semiconductors, optics, and coatings.
- It is employed to produce precision products like thin-film transistors, solar cells, anti-reflective coatings, and decorative finishes.
- The process is valued for its ability to deposit a wide range of materials, including metals, alloys, and ceramics, with high accuracy and uniformity.
-
Advantages of Sputtering:
- High precision and control over film properties.
- Ability to deposit a wide variety of materials.
- Excellent adhesion and uniformity of the deposited films.
- Suitable for large-scale production and complex geometries.
By following this structured process, sputtering provides a reliable and versatile method for creating high-quality thin films with tailored properties for various industrial applications.
Summary Table:
Key Aspect | Details |
---|---|
Process | Physical vapor deposition (PVD) using ionized gas to eject target atoms. |
Key Steps | Vacuum setup, inert gas introduction, plasma creation, target bombardment. |
Applications | Semiconductors, optics, coatings, solar cells, decorative finishes. |
Advantages | High precision, material versatility, excellent adhesion, scalability. |
Discover how sputtering can enhance your industrial processes—contact our experts today!