Zirconium production involves several key steps, starting from the extraction of zirconium-containing minerals to the final refinement into pure zirconium or zirconium compounds like zirconium dioxide (ZrO2). The process typically begins with mining zirconium-rich ores, such as zircon (ZrSiO4), followed by purification and chemical processing to isolate zirconium. The final stages involve refining zirconium into its metallic form or converting it into zirconium dioxide through calcination. The production process is complex and requires precise control over chemical and thermal conditions to achieve high-purity zirconium or zirconia.
Key Points Explained:
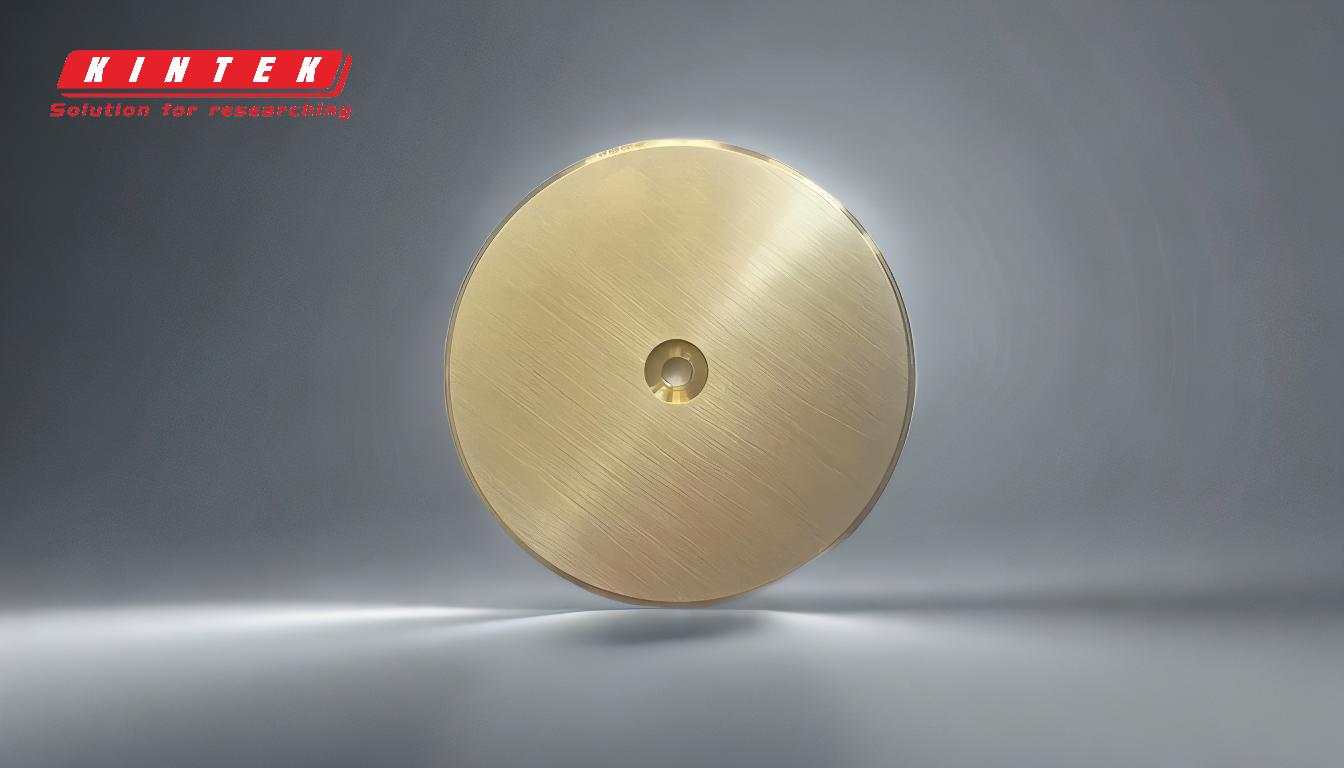
-
Mining and Extraction of Zirconium Ores:
- Zirconium is primarily extracted from zircon (ZrSiO4), a mineral found in heavy mineral sands.
- Mining involves dredging or dry mining techniques to separate zircon from other minerals like ilmenite and rutile.
- The extracted zircon is then concentrated through physical processes such as gravity separation and magnetic separation.
-
Purification of Zirconium Compounds:
- The concentrated zircon is chemically treated to remove impurities and isolate zirconium compounds.
- One common method involves chlorination, where zircon is reacted with chlorine and carbon at high temperatures to form zirconium tetrachloride (ZrCl4).
- Zirconium tetrachloride is then purified through distillation or sublimation to remove impurities.
-
Reduction to Metallic Zirconium:
- To produce metallic zirconium, zirconium tetrachloride is reduced using a reducing agent such as magnesium in the Kroll process.
- The reaction takes place in an inert atmosphere at high temperatures, yielding zirconium sponge, a porous form of zirconium.
- The zirconium sponge is further refined through vacuum arc melting or electron beam melting to produce high-purity zirconium metal.
-
Production of Zirconium Dioxide (Zirconia):
- Zirconium dioxide (ZrO2) is produced by calcining zirconium compounds, such as zirconium hydroxide or zirconium carbonate, at high temperatures.
- The calcination process drives off volatile components and converts the compound into zirconia.
- Zirconia exists in three crystalline forms: monoclinic, tetragonal, and cubic, with the tetragonal and cubic forms stabilized by the addition of dopants like yttria (Y2O3).
-
Applications and Importance of Zirconium and Zirconia:
- Zirconium metal is valued for its corrosion resistance and is used in nuclear reactors, chemical processing equipment, and biomedical implants.
- Zirconia is widely used in ceramics, refractories, and as a material for dental crowns and implants due to its high strength and biocompatibility.
- The production process is tailored to meet the specific requirements of these applications, ensuring high purity and controlled properties.
By understanding these steps, a purchaser of zirconium or zirconia can better evaluate the quality and suitability of the material for their specific needs. The production process highlights the importance of precise chemical and thermal control, as well as the need for high-purity raw materials to achieve the desired properties in the final product.
Summary Table:
Step | Details |
---|---|
Mining and Extraction | Zirconium is extracted from zircon (ZrSiO4) through dredging or dry mining. |
Purification | Zircon is chemically treated to form zirconium tetrachloride (ZrCl4). |
Reduction to Metal | ZrCl4 is reduced using magnesium in the Kroll process to produce zirconium sponge. |
Zirconia Production | Zirconium compounds are calcined to produce zirconium dioxide (ZrO2). |
Applications | Used in nuclear reactors, ceramics, dental implants, and more. |
Need high-purity zirconium or zirconia for your applications? Contact us today to learn more!