The product size of a ball mill is influenced by a variety of factors, including the design of the mill, the properties of the material being ground, and the operational parameters. The size of the final product can range from coarse particles to fine powders, depending on the specific requirements of the application. The key factors that determine the product size include the drum diameter, the ratio of drum diameter to length, the size and density of the balls, the rotation speed, and the milling fineness. Understanding these factors is crucial for optimizing the milling process to achieve the desired product size.
Key Points Explained:
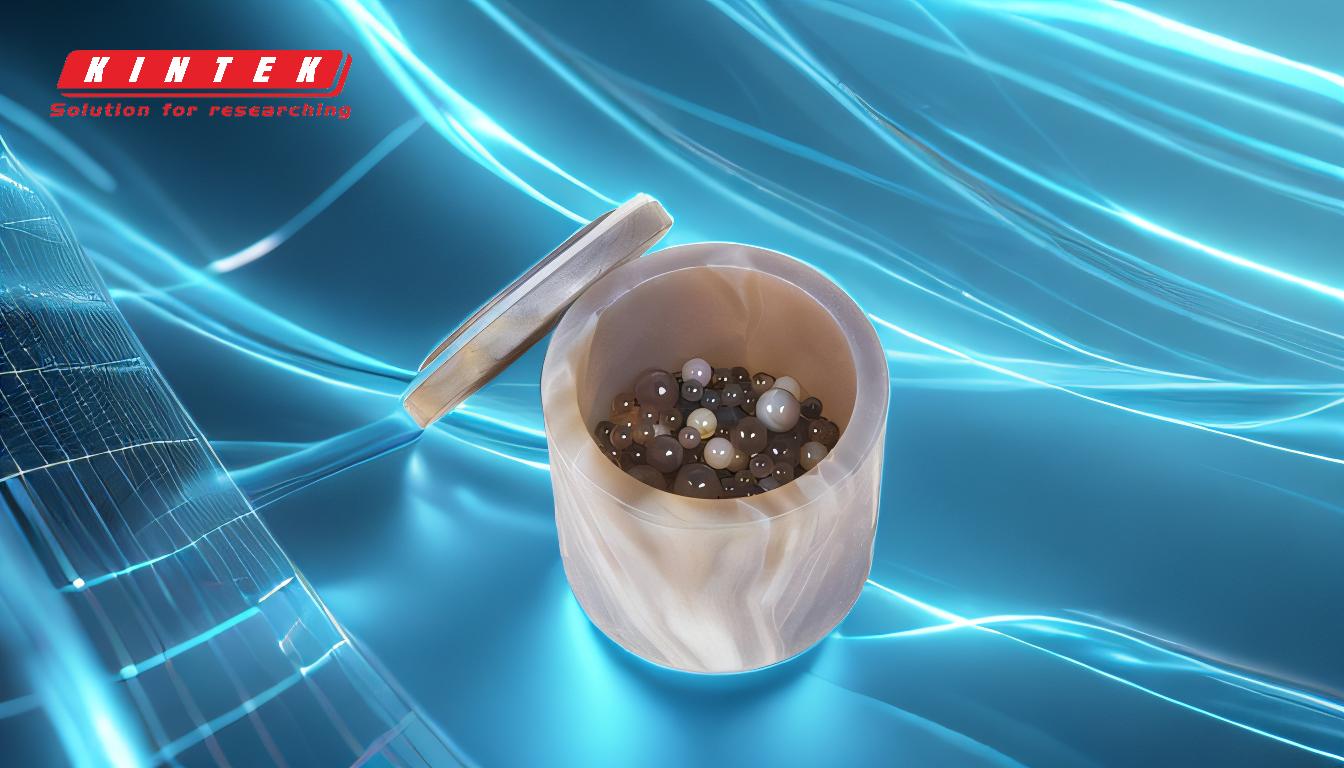
-
Drum Diameter and Length:
- The drum diameter and the ratio of drum diameter to length (L:D ratio) are critical design parameters that influence the product size. An optimal L:D ratio is typically between 1.56 and 1.64.
- A larger drum diameter generally allows for a greater volume of material to be processed, which can affect the grinding efficiency and the final product size.
- The length of the drum also plays a role in determining the residence time of the material in the mill, which in turn affects the degree of grinding.
-
Ball Size and Density:
- The size and density of the balls used in the mill are important factors that influence the grinding process. Larger balls are more effective at breaking down coarse particles, while smaller balls are better suited for fine grinding.
- The density of the balls affects the impact force and the energy transfer during the milling process, which can influence the final product size.
-
Rotation Speed:
- The rotation speed of the mill cylinder is a key operational parameter that affects the grinding efficiency and the product size. Higher rotation speeds generally result in more intense grinding, leading to finer particles.
- However, excessively high speeds can lead to over-grinding or inefficient energy use, so it is important to find an optimal speed for the specific application.
-
Milling Fineness:
- The desired fineness of the final product is a critical factor that determines the milling process parameters. Finer products require longer grinding times and may necessitate the use of smaller balls or higher rotation speeds.
- The milling fineness is also influenced by the physical-chemical properties of the feed material, such as hardness and moisture content.
-
Feed Rate and Material Properties:
- The feed rate of the material into the mill affects the residence time and the degree of grinding. A higher feed rate may result in coarser particles, while a lower feed rate can lead to finer grinding.
- The nature of the grinding material, including its hardness, brittleness, and moisture content, also plays a significant role in determining the final product size.
-
Timely Removal of Ground Product:
- The timely removal of the ground product from the mill is essential to prevent over-grinding and to maintain consistent product quality. Efficient removal mechanisms, such as screens or classifiers, help ensure that the desired product size is achieved.
-
Armor Surface Shape:
- The shape of the armor surface inside the mill can influence the grinding efficiency and the final product size. A smoother surface may result in less aggressive grinding, while a more textured surface can enhance the grinding action.
In summary, the product size of a ball mill is determined by a combination of design and operational factors. By carefully controlling these parameters, it is possible to achieve the desired product size for a wide range of applications.
Summary Table:
Factor | Influence on Product Size |
---|---|
Drum Diameter & Length | Larger diameter increases material volume; optimal L:D ratio (1.56–1.64) affects grinding efficiency. |
Ball Size & Density | Larger balls for coarse grinding; smaller balls for fine grinding. Density impacts energy transfer. |
Rotation Speed | Higher speeds yield finer particles; excessive speeds may cause over-grinding. |
Milling Fineness | Finer products require longer grinding times, smaller balls, or higher speeds. |
Feed Rate & Material Properties | Higher feed rate = coarser particles; material hardness and moisture affect grinding. |
Timely Removal of Product | Prevents over-grinding; ensures consistent product quality. |
Armor Surface Shape | Smoother surfaces = less aggressive grinding; textured surfaces enhance grinding action. |
Optimize your ball mill process for the perfect product size—contact our experts today!