Ball mills are versatile grinding machines used across various industries, including mining, cement, ceramics, and scientific research. Their range of applications is broad, encompassing tasks like particle size reduction, mechanical alloying, and material mixing. The performance and productivity of ball mills depend on several factors, such as drum dimensions, ball size and density, rotation speed, and material properties. The optimal length-to-diameter ratio for ball mills is typically between 1.56 and 1.64, ensuring efficient grinding. Additionally, factors like feed rate, residence time, and timely removal of ground material significantly influence the milling process. Understanding these variables is crucial for selecting and operating ball mills effectively.
Key Points Explained:
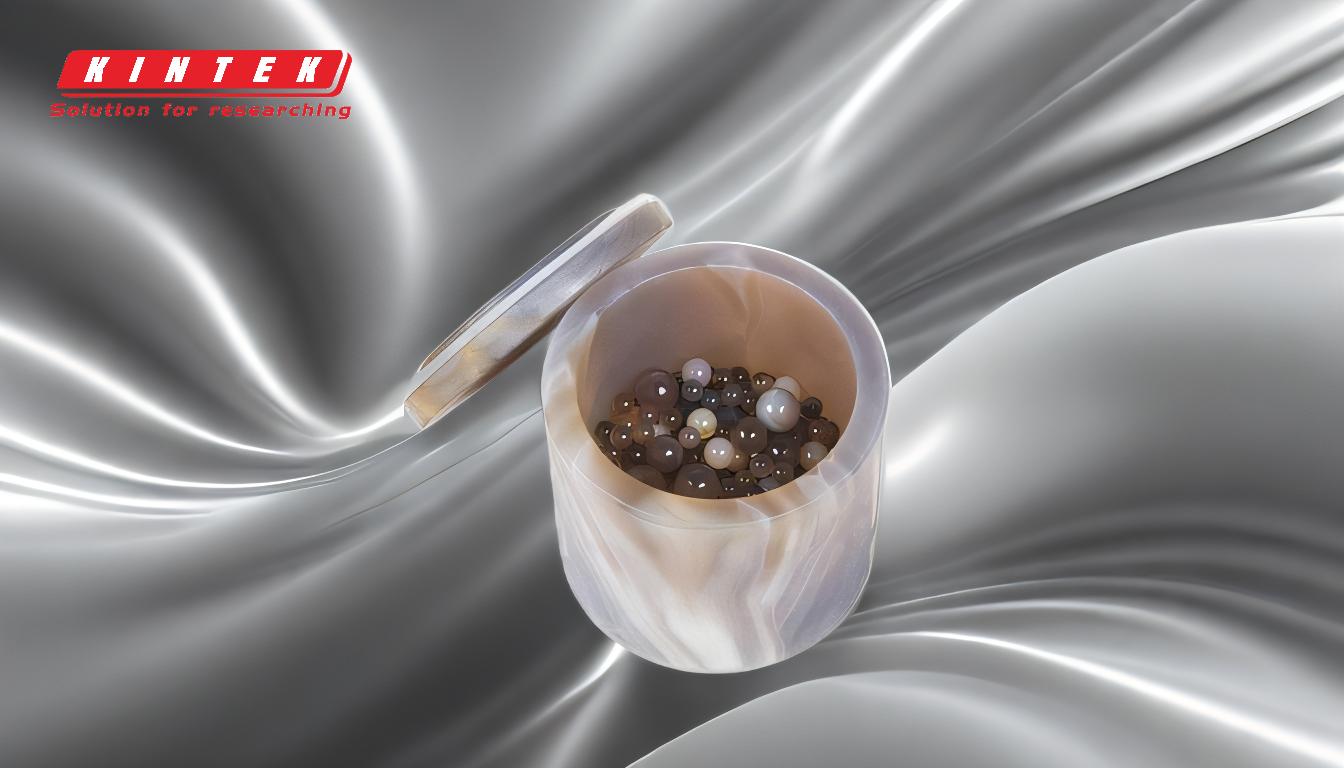
-
Applications of Ball Mills:
- Ball mills are used in industries such as mining, cement, ceramics, and scientific research.
- They perform tasks like grinding ores, coal, pigments, and feldspar, as well as reducing particle size, eliminating agglomeration, and producing powders.
- They are also used for mechanical alloying, mixing materials, and altering material properties.
-
Factors Influencing Milling Efficiency:
- Residence Time: The duration material spends in the mill chamber affects the degree of grinding.
- Ball Characteristics: The size, density, and number of balls impact grinding efficiency.
- Material Properties: The nature of the grinding material (e.g., hardness, moisture content) influences the milling process.
- Feed Rate and Level: The amount and consistency of material fed into the mill affect productivity.
- Rotation Speed: The speed at which the cylinder rotates determines the grinding action and energy transfer.
-
Optimal Design Parameters:
- Drum Dimensions: The diameter and length of the drum are critical. The optimal length-to-diameter (L:D) ratio is between 1.56 and 1.64.
- Ball Filling and Sizes: Proper filling of balls and their sizes ensure efficient grinding and energy utilization.
- Armor Surface Shape: The design of the mill's interior surface affects the grinding process and material flow.
-
Productivity Considerations:
- Physical-Chemical Properties of Feed Material: Properties like hardness, brittleness, and moisture content influence grinding efficiency.
- Milling Fineness: The desired particle size affects the grinding time and energy consumption.
- Timely Removal of Ground Product: Efficient removal of processed material prevents over-grinding and maintains productivity.
-
Industrial Importance:
- Ball mills are essential in industries like cement production, silicate manufacturing, and glass ceramics.
- They play a crucial role in producing high-quality powders and materials with specific properties.
By understanding these key points, purchasers and operators can make informed decisions about selecting and optimizing ball mills for their specific applications.
Summary Table:
Key Factor | Description |
---|---|
Applications | Mining, cement, ceramics, scientific research, particle size reduction, alloying, mixing. |
Drum Dimensions | Optimal length-to-diameter ratio: 1.56–1.64 for efficient grinding. |
Ball Characteristics | Size, density, and number of balls impact grinding efficiency. |
Rotation Speed | Determines grinding action and energy transfer. |
Material Properties | Hardness, moisture content, and brittleness influence grinding efficiency. |
Productivity Factors | Feed rate, residence time, and timely removal of ground material are crucial. |
Optimize your ball mill performance today—contact our experts for tailored solutions!