The temperature for carbon reactivation typically ranges between 700°C and 900°C. This process involves passing spent carbon through a slowly-rotating horizontal kiln, where the high temperature helps to remove adsorbed contaminants and restore the carbon's adsorption capacity. The specific temperature within this range depends on the type of carbon, the nature of the contaminants, and the desired reactivation efficiency.
Key Points Explained:
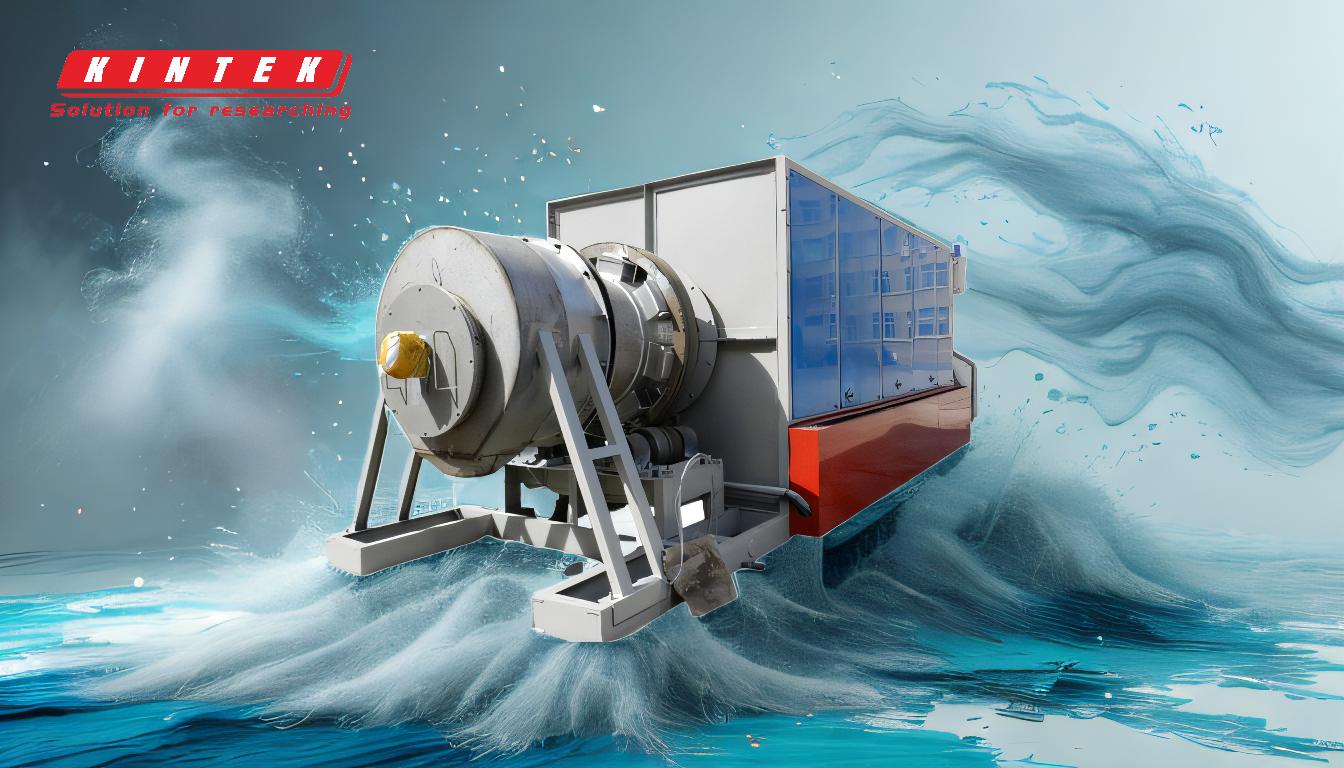
-
Temperature Range for Carbon Reactivation (700°C to 900°C)
- The reactivation process requires high temperatures to effectively remove adsorbed contaminants from the carbon surface.
- The range of 700°C to 900°C is optimal for breaking down organic compounds and volatilizing impurities without damaging the carbon structure.
- Lower temperatures may not fully regenerate the carbon, while higher temperatures could degrade the carbon's physical properties.
-
Role of the Horizontal Kiln
- A slowly-rotating horizontal kiln is commonly used for reactivation.
- The rotation ensures uniform heating and exposure of the carbon to the high temperatures.
- This setup allows for controlled reactivation, minimizing the risk of overheating or incomplete regeneration.
-
Factors Influencing the Temperature
- Type of Carbon: Different carbon types (e.g., granular activated carbon, powdered activated carbon) may require slightly varying temperatures for optimal reactivation.
- Nature of Contaminants: Organic contaminants typically require higher temperatures for complete removal compared to inorganic impurities.
- Desired Reactivation Efficiency: The temperature may be adjusted based on the level of regeneration required and the intended reuse of the carbon.
-
Importance of Temperature Control
- Precise temperature control is critical to ensure effective reactivation while preserving the carbon's structural integrity.
- Overheating can lead to excessive burn-off, reducing the carbon's adsorption capacity and lifespan.
- Insufficient heating may leave residual contaminants, compromising the carbon's performance in subsequent uses.
-
Applications of Reactivated Carbon
- Reactivated carbon is widely used in water treatment, air purification, and industrial processes.
- The reactivation process makes carbon reuse economically and environmentally sustainable, reducing the need for virgin carbon production.
By maintaining the temperature within the 700°C to 900°C range and using appropriate equipment, the carbon reactivation process ensures efficient regeneration and extends the life of activated carbon, making it a cost-effective and sustainable solution for various applications.
Summary Table:
Key Aspect | Details |
---|---|
Temperature Range | 700°C to 900°C for effective contaminant removal and carbon preservation. |
Equipment Used | Slowly-rotating horizontal kiln for uniform heating and controlled process. |
Factors Influencing Temp | Carbon type, contaminant nature, and desired reactivation efficiency. |
Applications | Water treatment, air purification, and industrial processes. |
Optimize your carbon reactivation process—contact our experts today for tailored solutions!