Vibration shakers, also known as electrodynamic shakers, are devices used to simulate vibration environments for testing purposes. They operate based on the principle of electromagnetic induction, where an alternating current (AC) passes through a coil within a magnetic field, generating a force that causes the shaker's table to vibrate. This vibration can be precisely controlled in terms of frequency, amplitude, and waveform, making it ideal for testing the durability, performance, and reliability of various components and systems. The shaker's design includes a moving coil, a stationary magnet, and a table where the test specimen is mounted. By adjusting the input signal, the shaker can replicate real-world vibration conditions, such as those experienced during transportation or operation, ensuring that products meet stringent quality and safety standards.
Key Points Explained:
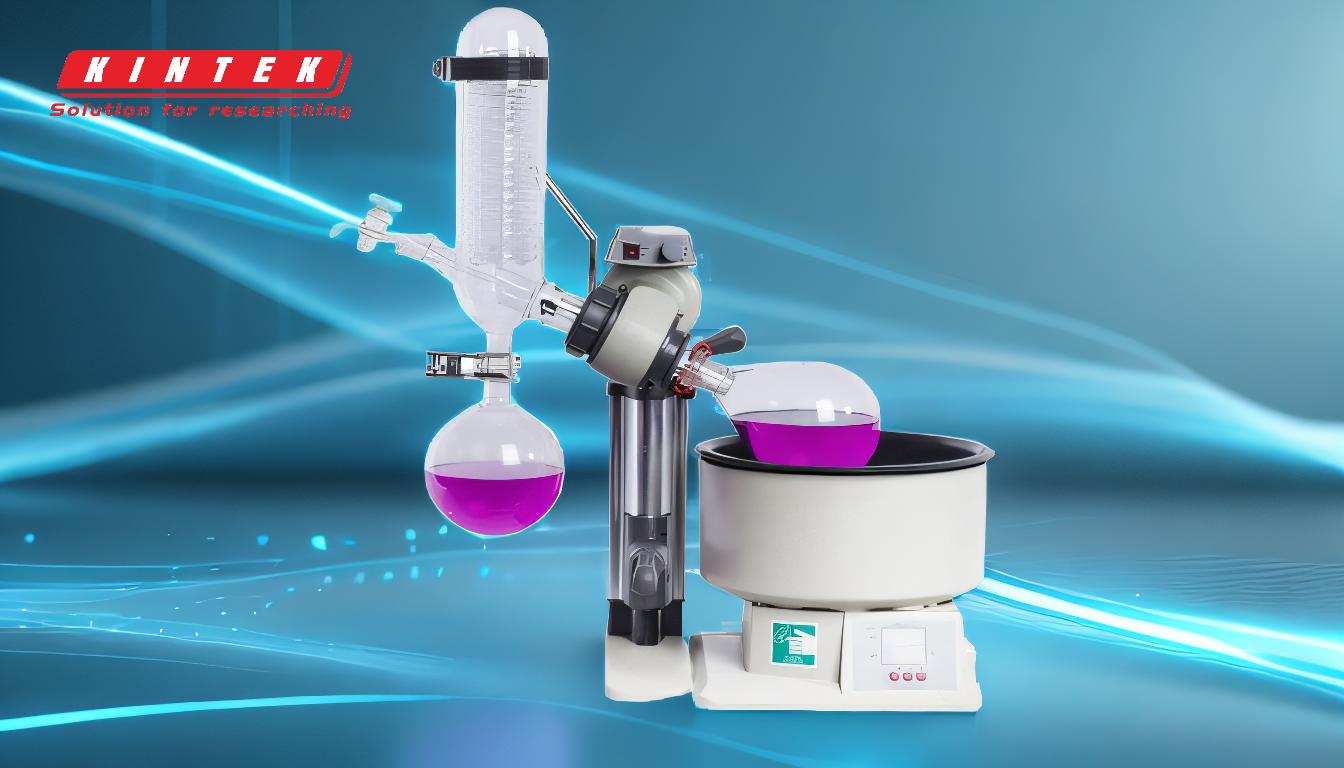
-
Electromagnetic Induction Principle:
- Vibration shakers operate on the principle of electromagnetic induction. When an alternating current (AC) flows through a coil placed within a magnetic field, it generates a force (Lorentz force) that causes the coil to move. This movement is transferred to the shaker's table, creating vibration.
- The magnetic field is typically provided by a permanent magnet or an electromagnet, and the coil is attached to the shaker's moving element (armature).
-
Components of a Vibration Shaker:
- Moving Coil: The coil is the primary moving part of the shaker. It is attached to the armature and moves within the magnetic field when current flows through it.
- Stationary Magnet: This provides the necessary magnetic field for the coil to interact with. It is usually made of high-strength materials like neodymium or ferrite.
- Table (Armature): The table is where the test specimen is mounted. It moves in response to the coil's motion, creating the desired vibration.
- Suspension System: This system supports the moving components and ensures that they move freely within the magnetic field without mechanical interference.
- Control System: This includes the electronics and software that control the input signal to the coil, allowing precise control over the vibration's frequency, amplitude, and waveform.
-
Control of Vibration Parameters:
- Frequency: The frequency of the vibration is determined by the frequency of the AC signal applied to the coil. Higher frequencies result in faster vibrations, while lower frequencies produce slower vibrations.
- Amplitude: The amplitude of the vibration is controlled by the strength of the current flowing through the coil. Increasing the current increases the force applied to the coil, resulting in larger vibrations.
- Waveform: The waveform of the vibration (e.g., sinusoidal, random, or shock) is determined by the shape of the input signal. Different waveforms are used to simulate different types of real-world vibration conditions.
-
Applications of Vibration Shakers:
- Product Testing: Vibration shakers are widely used in industries such as aerospace, automotive, electronics, and consumer goods to test the durability and reliability of products under various vibration conditions.
- Research and Development: They are used in R&D to study the effects of vibration on materials, components, and systems, helping engineers design more robust products.
- Quality Assurance: Vibration testing is a critical part of quality assurance processes, ensuring that products meet industry standards and regulatory requirements before they are released to the market.
-
Advantages of Vibration Shakers:
- Precision: Vibration shakers offer precise control over vibration parameters, allowing for accurate simulation of real-world conditions.
- Versatility: They can generate a wide range of vibration frequencies and amplitudes, making them suitable for testing a variety of products and materials.
- Repeatability: Vibration tests can be repeated with high consistency, ensuring reliable and comparable results over time.
-
Limitations and Considerations:
- Size and Weight: Vibration shakers can be large and heavy, especially those designed for high-force applications. This can limit their portability and require significant space for installation.
- Heat Generation: The coil and other components can generate heat during operation, which may require cooling systems to prevent overheating.
- Cost: High-quality vibration shakers can be expensive, particularly those designed for specialized applications or high-performance requirements.
In summary, vibration shakers are essential tools in the field of vibration testing, offering precise control over vibration parameters to simulate real-world conditions. Their operation is based on the principle of electromagnetic induction, and they consist of key components like the moving coil, stationary magnet, and table. These devices are widely used in product testing, R&D, and quality assurance, providing valuable insights into the durability and reliability of various products and materials. However, considerations such as size, heat generation, and cost must be taken into account when selecting and using vibration shakers.
Summary Table:
Key Aspect | Details |
---|---|
Principle | Electromagnetic induction: AC current in a coil generates Lorentz force. |
Components | Moving coil, stationary magnet, table, suspension system, control system. |
Controlled Parameters | Frequency, amplitude, waveform (sinusoidal, random, shock). |
Applications | Product testing, R&D, quality assurance in aerospace, automotive, etc. |
Advantages | Precision, versatility, repeatability. |
Limitations | Size/weight, heat generation, cost. |
Discover how vibration shakers can enhance your testing processes—contact our experts today!