Thin film deposition is a critical process in various industries, requiring specific materials and techniques to achieve desired properties such as improved tribological behavior, enhanced optics, and better aesthetics. The materials used in thin film deposition typically include metals, oxides, and compounds, each chosen for their unique properties. Common techniques like Physical Vapour Deposition (PVD), Chemical Vapour Deposition (CVD), Atomic Layer Deposition (ALD), and Spray Pyrolysis are employed to deposit these materials onto substrates. The process involves selecting a pure material source, transporting it to the substrate, depositing it to form a thin film, and optionally annealing or heat-treating the film. The choice of materials and techniques depends on the specific application and desired film properties.
Key Points Explained:
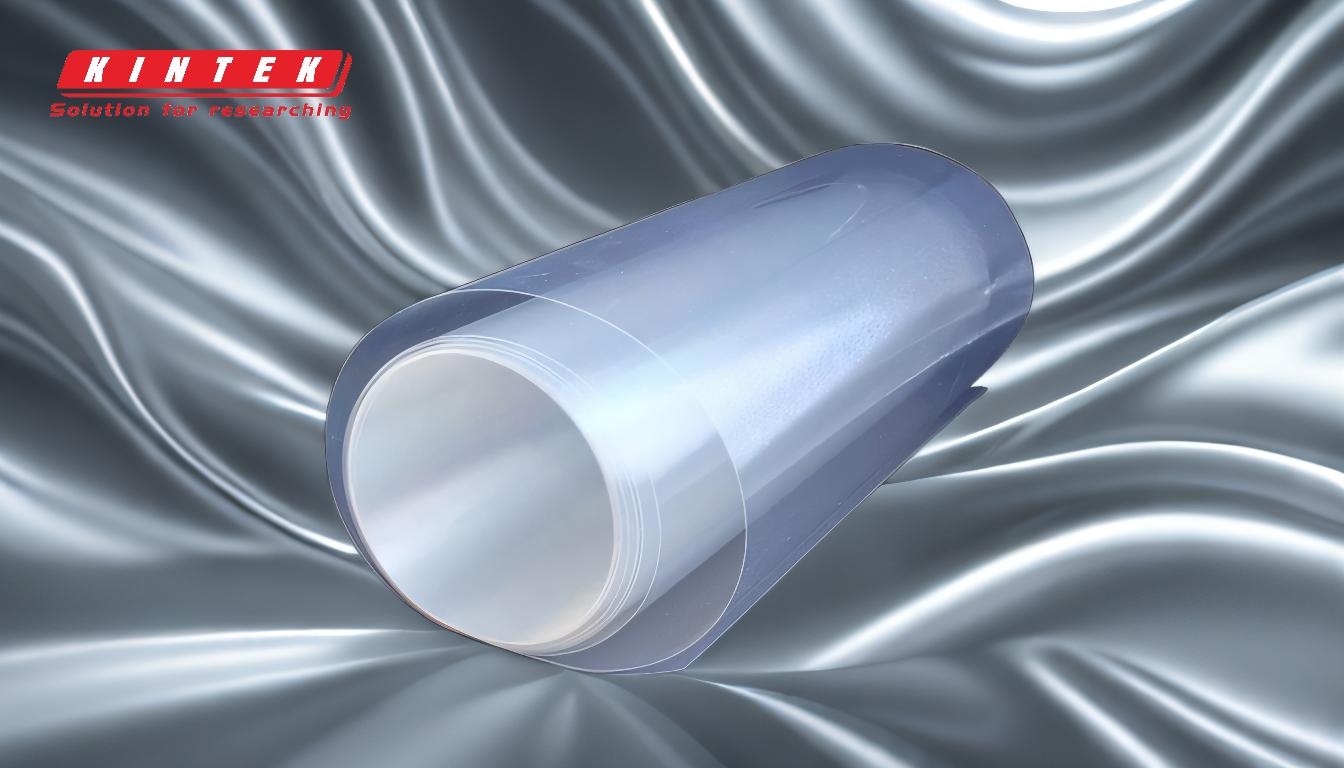
-
Materials Used in Thin Film Deposition:
- Metals: Metals like copper, aluminum, and gold are commonly used due to their excellent electrical conductivity and reflectivity. They are often used in electronic and optical applications.
- Oxides: Oxides such as copper oxide (CuO) and indium tin oxide (ITO) are widely used in thin-film technology. ITO, for example, is popular in transparent conductive coatings for displays and solar cells.
- Compounds: Compounds like copper indium gallium diselenide (CIGS) are used in photovoltaic applications due to their high efficiency in converting sunlight to electricity.
-
Techniques for Thin Film Deposition:
- Physical Vapour Deposition (PVD): This technique involves evaporating or sputtering the source material in a vacuum, allowing it to condense on the substrate. PVD is known for producing high-purity films with excellent adhesion.
- Chemical Vapour Deposition (CVD): CVD uses chemical reactions to deposit a thin coating on the substrate. It is suitable for depositing complex materials and can produce films with excellent uniformity.
- Atomic Layer Deposition (ALD): ALD deposits films one atomic layer at a time, allowing for precise control over film thickness and composition. This technique is ideal for applications requiring ultra-thin, uniform films.
- Spray Pyrolysis: This method involves spraying a material solution onto the substrate and thermally degrading it to form a thin film. It is a cost-effective technique suitable for large-area coatings.
-
Process of Thin Film Deposition:
- Material Selection: The process begins with selecting a pure material source (target) based on the desired film properties.
- Transportation: The target material is transported to the prepared substrate through a medium, which could be a fluid or a vacuum, depending on the deposition technique.
- Deposition: The target material is deposited onto the substrate to form a thin film. This step may involve various techniques like evaporation, sputtering, or chemical reactions.
- Post-Deposition Treatment: The deposited film may undergo annealing or heat treatment to improve its properties, such as adhesion, crystallinity, and electrical conductivity.
- Analysis and Modification: The film's properties are analyzed, and the deposition process may be modified to achieve the desired results.
-
Applications of Thin Film Deposition:
- Tribological Behavior: Thin films are used to improve the wear resistance and friction properties of surfaces, making them ideal for applications in automotive and aerospace industries.
- Optics: Thin films enhance the optical properties of materials, used in lenses, mirrors, and optical coatings.
- Aesthetics: Thin films are applied to improve the appearance of products, such as decorative coatings on consumer electronics.
- Electronics: Thin films are crucial in the manufacturing of semiconductors, displays, and solar cells, where precise control over material properties is essential.
In summary, the materials and techniques used in thin film deposition are carefully selected based on the application's requirements. The process involves several steps, from material selection to post-deposition treatment, ensuring the final film meets the desired specifications. The versatility of thin film technology makes it indispensable in various industries, from electronics to optics and beyond.
Summary Table:
Category | Materials | Techniques | Applications |
---|---|---|---|
Metals | Copper, Aluminum, Gold | PVD, CVD | Electronics, Optics |
Oxides | Copper Oxide (CuO), ITO | CVD, ALD | Solar Cells, Displays |
Compounds | CIGS | Spray Pyrolysis | Photovoltaics |
Need expert guidance on thin film deposition? Contact us today to find the perfect solution for your application!