Sieve analysis is a widely used method for determining the particle size distribution of granular materials. However, several factors can affect the accuracy and reliability of the results. One significant issue is the reaction of the material to ambient conditions, such as relative humidity, which can cause fine powders to adhere to sieve components and each other due to electrostatic charges. This adherence can lead to inaccurate particle size measurements. Other potential problems include improper sieve handling, overloading, particle shape, and sieve wear. Understanding these factors is crucial for ensuring the accuracy of sieve analysis results.
Key Points Explained:
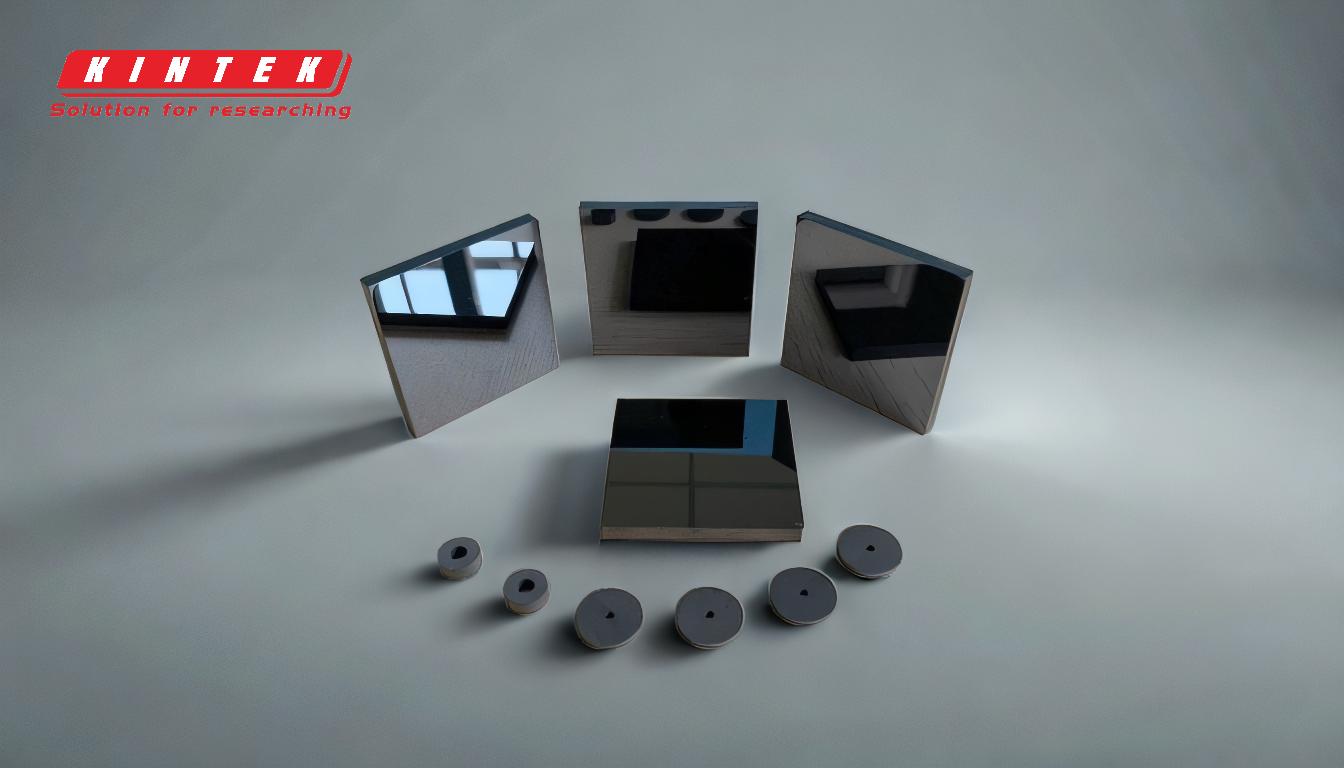
-
Ambient Conditions and Electrostatic Charges:
- Relative Humidity: Extremely dry conditions can lead to the buildup of electrostatic charges, causing fine powders to adhere to sieve components and each other. This adherence can prevent particles from passing through the sieve openings, leading to inaccurate size distribution results.
- Mitigation: Controlling the humidity in the testing environment or using anti-static agents can help reduce the impact of electrostatic charges on the sieve analysis.
-
Improper Sieve Handling:
- Sieve Cleaning: Inadequate cleaning of sieves between tests can lead to contamination and clogging, affecting the accuracy of subsequent analyses.
- Sieve Storage: Improper storage can result in damage to the sieve mesh, leading to distorted results. Sieves should be stored in a clean, dry environment to maintain their integrity.
-
Overloading the Sieve:
- Excessive Material: Overloading the sieve with too much material can prevent proper particle separation, as the particles may not have enough space to move freely through the sieve openings.
- Optimal Loading: It is essential to use the correct amount of sample material to ensure accurate and repeatable results. Following the recommended sample size for the specific sieve and material type is crucial.
-
Particle Shape:
- Non-Spherical Particles: Particles that are not spherical (e.g., elongated or flat) may not pass through the sieve openings as easily as spherical particles, leading to inaccurate size distribution measurements.
- Sieving Time: Adjusting the sieving time or using alternative methods (e.g., air jet sieving) can help improve the accuracy of results for non-spherical particles.
-
Sieve Wear and Tear:
- Mesh Damage: Over time, the sieve mesh can become worn or damaged, leading to changes in the effective opening size and affecting the accuracy of the analysis.
- Regular Inspection: Regularly inspecting sieves for wear and replacing them as needed is essential to maintain the accuracy of sieve analysis results.
-
Material Properties:
- Moisture Content: Materials with high moisture content can clump together, making it difficult for particles to pass through the sieve openings.
- Temperature Sensitivity: Some materials may change properties (e.g., become more brittle or sticky) at different temperatures, affecting their behavior during sieving.
-
Sieve Agitation:
- Insufficient Agitation: Inadequate agitation can result in incomplete separation of particles, leading to inaccurate size distribution results.
- Optimal Agitation: Ensuring that the sieve is agitated correctly (e.g., using a mechanical shaker) is crucial for achieving accurate and consistent results.
-
Sample Preparation:
- Representative Sampling: The sample used for sieve analysis must be representative of the entire batch to ensure accurate results. Inadequate sampling can lead to biased results.
- Sample Division: Properly dividing the sample to ensure uniformity is essential for accurate analysis.
By addressing these potential problems, you can improve the accuracy and reliability of sieve analysis results, ensuring that the particle size distribution data is both precise and representative of the material being tested.
Summary Table:
Factor | Impact on Sieve Analysis | Mitigation |
---|---|---|
Ambient Conditions | Electrostatic charges cause fine powders to adhere, leading to inaccurate results. | Control humidity or use anti-static agents. |
Improper Sieve Handling | Contamination or damage from improper cleaning/storage affects accuracy. | Clean sieves thoroughly and store in a dry, clean environment. |
Overloading the Sieve | Excessive material prevents proper particle separation. | Use the recommended sample size for accurate results. |
Particle Shape | Non-spherical particles may not pass through sieve openings easily. | Adjust sieving time or use alternative methods like air jet sieving. |
Sieve Wear and Tear | Damaged mesh alters opening size, affecting accuracy. | Regularly inspect and replace worn sieves. |
Material Properties | High moisture or temperature sensitivity can cause clumping or property changes. | Control moisture levels and temperature during testing. |
Sieve Agitation | Inadequate agitation results in incomplete particle separation. | Use proper mechanical agitation for consistent results. |
Sample Preparation | Non-representative or improperly divided samples lead to biased results. | Ensure representative sampling and uniform division. |
Need help optimizing your sieve analysis? Contact our experts today for tailored solutions!