Ball mills are versatile grinding machines used in various industries, and their size can vary significantly depending on the application, capacity, and design requirements. The size of a ball mill is typically described by its internal diameter and length, which determine its grinding capacity and efficiency. Smaller ball mills are used in laboratories for research purposes, while larger industrial ball mills are used in mining, cement production, and other heavy industries. The size of a ball mill is crucial for optimizing grinding performance and ensuring it meets the specific needs of the operation.
Key Points Explained:
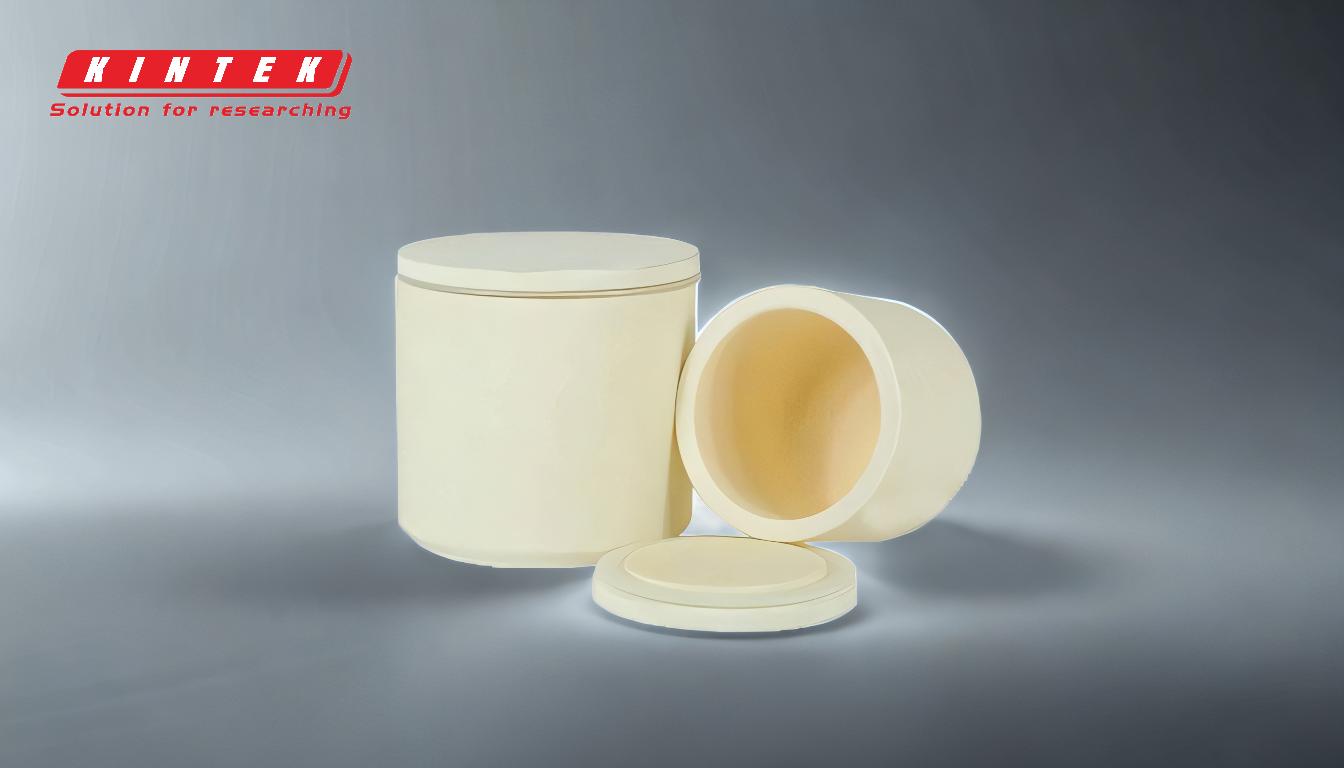
-
Definition of Ball Mill Size:
- The size of a ball mill is generally defined by its internal diameter and length. These dimensions are critical because they determine the volume of the grinding chamber, which directly affects the mill's capacity and efficiency.
- For example, a ball mill with a diameter of 2 meters and a length of 3 meters would be referred to as a 2x3 meter ball mill.
-
Range of Ball Mill Sizes:
- Laboratory Ball Mills: These are small-scale ball mills used for research and development. They typically have diameters ranging from a few centimeters to about 0.5 meters.
- Industrial Ball Mills: These are much larger and are used in industries such as mining, cement production, and chemical processing. Industrial ball mills can have diameters ranging from 1 meter to over 5 meters and lengths up to 15 meters or more.
- Custom Sizes: Ball mills can be custom-designed to meet specific operational requirements, which may result in non-standard sizes.
-
Factors Influencing Ball Mill Size:
- Capacity Requirements: The size of the ball mill is often determined by the required throughput or grinding capacity. Larger mills are needed for higher production rates.
- Material Characteristics: The hardness, density, and size of the material being ground influence the size of the ball mill. Harder materials may require larger mills with more powerful motors.
- Grinding Media: The size and type of grinding media (balls) used in the mill also affect the mill's size. Larger grinding media may require a larger mill to achieve the desired grinding efficiency.
- Operational Parameters: Factors such as rotational speed, filling ratio, and the type of grinding circuit (open or closed) can influence the optimal size of the ball mill.
-
Importance of Correct Sizing:
- Efficiency: Properly sizing a ball mill ensures that it operates at peak efficiency, minimizing energy consumption and maximizing grinding performance.
- Cost-Effectiveness: An appropriately sized ball mill reduces operational costs by avoiding over-sizing (which leads to unnecessary energy use) or under-sizing (which can result in insufficient grinding capacity).
- Product Quality: The size of the ball mill affects the fineness and consistency of the ground product. A correctly sized mill ensures that the desired product specifications are met.
-
Examples of Ball Mill Sizes in Different Applications:
- Mining Industry: In the mining industry, ball mills used for grinding ore can be very large, with diameters exceeding 5 meters and lengths of 10 meters or more. These mills are designed to handle large volumes of material and operate continuously.
- Cement Industry: Ball mills in the cement industry are also large, typically ranging from 3 to 5 meters in diameter and 10 to 15 meters in length. They are used to grind clinker and other raw materials to produce cement.
- Laboratory Use: Laboratory ball mills are much smaller, with diameters ranging from 0.1 to 0.5 meters. These mills are used for small-scale grinding and testing of materials.
-
Considerations for Purchasing a Ball Mill:
- Application: Determine the specific application (e.g., mining, cement, laboratory) to guide the selection of the appropriate size.
- Capacity: Assess the required throughput and grinding capacity to ensure the mill can handle the expected workload.
- Material Properties: Consider the properties of the material to be ground, such as hardness and particle size, to select a mill that can effectively process the material.
- Operational Environment: Evaluate the operational environment, including space constraints and power availability, to ensure the selected mill size is feasible.
- Budget: Balance the cost of the mill with the expected performance and operational savings to make a cost-effective purchase decision.
In summary, the size of a ball mill is a critical factor that influences its performance, efficiency, and suitability for specific applications. By understanding the key factors that determine ball mill size and considering the specific needs of the operation, purchasers can select the right ball mill to meet their requirements.
Summary Table:
Aspect | Details |
---|---|
Definition | Size defined by internal diameter and length. |
Range of Sizes | - Lab mills: 0.1–0.5m diameter |
- Industrial mills: 1–5m+ diameter, up to 15m+ length | |
Key Influencing Factors | - Capacity requirements |
- Material characteristics
- Grinding media
- Operational parameters | | Importance of Sizing | - Efficiency
- Cost-effectiveness
- Product quality | | Applications | - Mining: 5m+ diameter, 10m+ length
- Cement: 3–5m diameter, 10–15m length
- Lab: 0.1–0.5m diameter |
Need help selecting the right ball mill size for your application? Contact our experts today for personalized guidance!