Sputtering is a versatile and widely used thin-film deposition technique with numerous advantages. It allows for the deposition of a wide range of materials, including those with high melting points, low vapor pressure, and poor electrical conductivity. The process ensures excellent film adhesion, high purity, and density, with minimal contamination. Sputtering offers precise control over film thickness, uniformity, and reproducibility, making it suitable for large-area coatings. Additionally, it supports the deposition of smooth, decorative, and hard coatings, and can handle both conductive and non-conductive materials. The process is environmentally friendly, with high deposition rates and the ability to clean and coat substrates in the same vacuum chamber.
Key Points Explained:
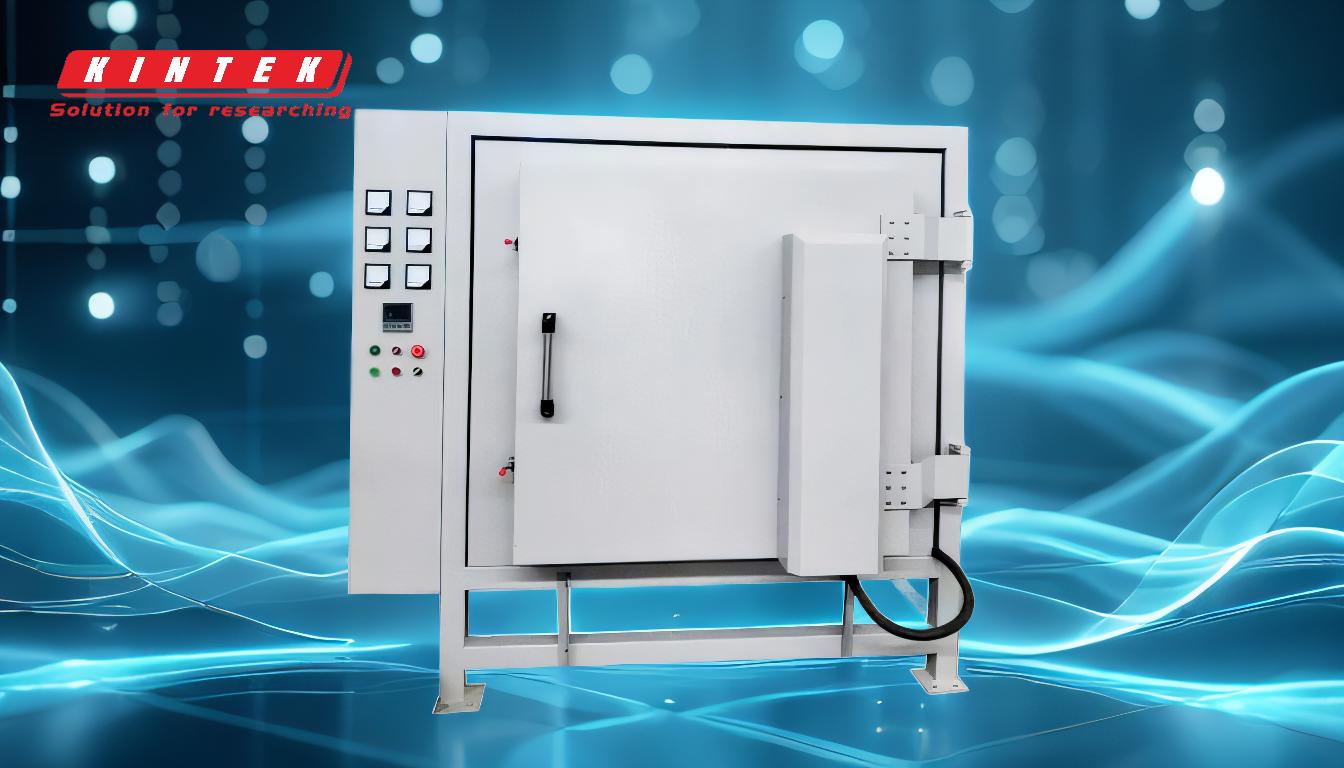
-
Versatility in Material Deposition:
- Sputtering can deposit a wide range of materials, including metals, semiconductors, insulators, compounds, and mixtures.
- It is particularly effective for materials with high melting points and low vapor pressure, which are challenging to deposit using other methods.
- Materials with low melting points and poor electrical conductivity can also be sputtered, expanding the range of usable target materials.
-
Excellent Film Adhesion:
- The high energy of sputtered atoms enhances adhesion between the film and the substrate.
- This results in the formation of a diffusion layer, improving the overall bond strength and durability of the coating.
-
High Purity and Density:
- Sputtering avoids contamination from evaporation sources, leading to high-purity films.
- The process produces dense coatings with fewer pinholes, which is crucial for applications requiring high-quality, defect-free films.
-
Precise Control Over Film Thickness:
- Film thickness can be accurately controlled by adjusting the target current.
- This ensures reproducibility and uniformity, making sputtering ideal for applications requiring consistent film properties.
-
Uniform Thickness Over Large Areas:
- Sputter coating can produce films with uniform thickness over large areas, which is essential for industrial applications such as solar panels and display technologies.
-
Smooth and Decorative Coatings:
- Sputtering produces very smooth coatings, which are desirable for decorative and functional applications.
- It can create hard coatings, such as Ti, Cr, Zr, and Carbon Nitrides, which are used in various industrial and decorative applications.
-
Flexibility in Equipment Design:
- The ability to position cathodes in various orientations allows for high flexibility in equipment design.
- This adaptability enables the coating of complex geometries and large substrates.
-
Environmentally Friendly:
- Sputtering is an environmentally friendly method, as it allows for the deposition of small quantities of oxides, metals, and alloys without significant waste.
- The process can be conducted in a vacuum, reducing the release of harmful byproducts.
-
High Deposition Rates:
- Sputtering offers high deposition rates without thickness limits, making it efficient for large-scale production.
- The process can clean substrates and deposit coatings in the same vacuum chamber, streamlining the production process.
-
Reduced Residual Stresses:
- The low or medium temperature deposition process reduces residual stresses on the substrate.
- This is beneficial for substrates that are sensitive to high temperatures, such as polymers or certain metals.
-
Capability to Coat Non-Conductive Materials:
- Sputtering can deposit non-conductive materials using radio frequency (RF) or medium frequency (MF) power.
- This capability expands the range of materials that can be coated, including insulators and ceramics.
-
Reactive Processes for Oxide Coatings:
- Sputtering can produce oxide coatings through reactive processes, which are essential for applications requiring specific optical, electrical, or mechanical properties.
In summary, sputtering is a highly advantageous thin-film deposition technique due to its versatility, precision, and ability to produce high-quality coatings. Its ability to handle a wide range of materials, ensure excellent adhesion, and provide precise control over film properties makes it a preferred choice in various industries.
Summary Table:
Advantage | Description |
---|---|
Versatility in Material Deposition | Deposits metals, semiconductors, insulators, and more, including high-melting-point materials. |
Excellent Film Adhesion | High-energy sputtered atoms enhance adhesion, forming a durable diffusion layer. |
High Purity and Density | Produces contamination-free, dense coatings with minimal pinholes. |
Precise Control Over Film Thickness | Adjust target current for accurate, reproducible, and uniform film thickness. |
Uniform Thickness Over Large Areas | Ideal for industrial applications like solar panels and displays. |
Smooth and Decorative Coatings | Creates smooth, hard coatings for decorative and functional uses. |
Flexibility in Equipment Design | Adaptable for coating complex geometries and large substrates. |
Environmentally Friendly | Minimal waste and vacuum-based process reduce environmental impact. |
High Deposition Rates | Efficient for large-scale production with no thickness limits. |
Reduced Residual Stresses | Low/medium temperature deposition is ideal for temperature-sensitive substrates. |
Coat Non-Conductive Materials | RF/MF power enables deposition on insulators and ceramics. |
Reactive Processes for Oxide Coatings | Produces oxide coatings with specific optical, electrical, or mechanical properties. |
Ready to explore how sputtering can enhance your thin-film applications? Contact our experts today for tailored solutions!