Diffusion pumps are critical components in vacuum systems, and the choice of oil significantly impacts their performance, maintenance, and longevity. Silicone oil is the most commonly used type of oil in diffusion pumps due to its high vapor point, chemical stability, and favorable safety profile. It is essential to select high-quality oil that matches the required vacuum level to avoid unnecessary costs and ensure optimal performance. Below, the key points related to the use of silicone oil in diffusion pumps are explained in detail.
Key Points Explained:
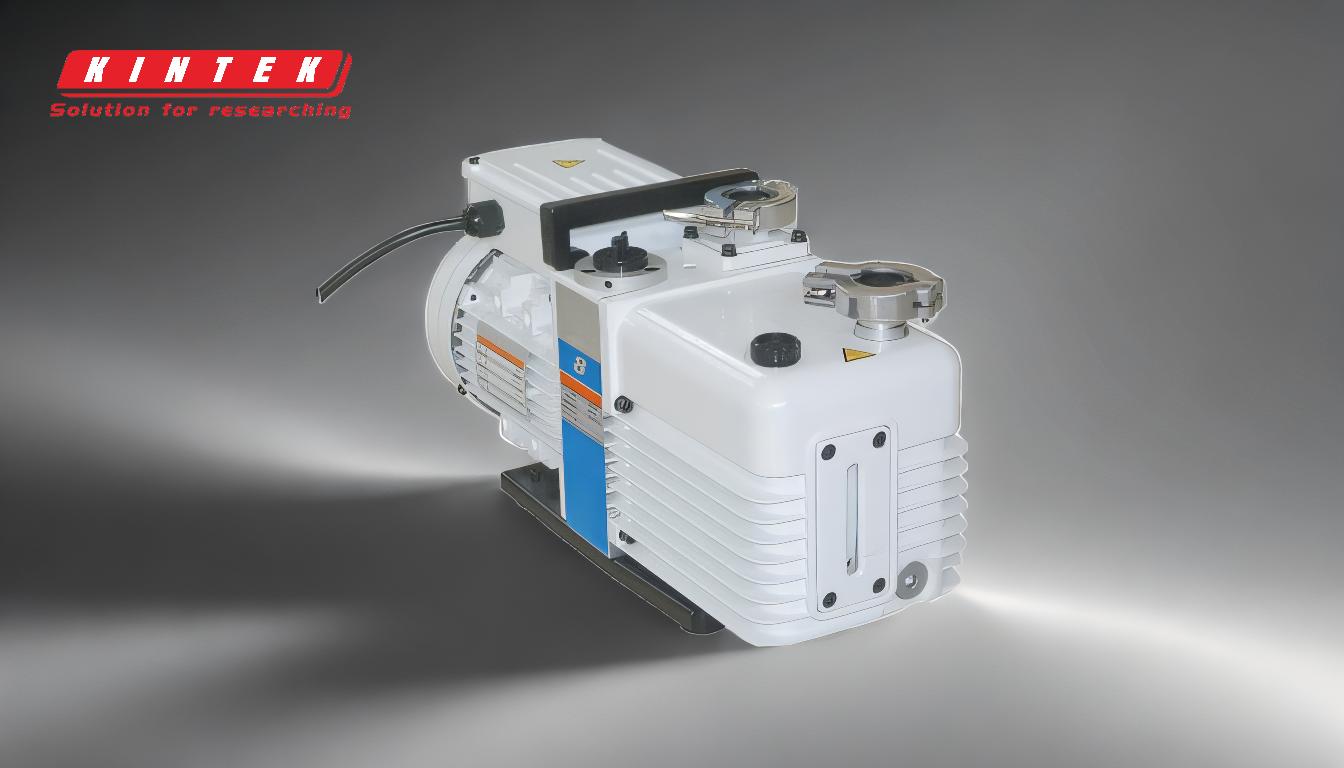
-
Silicone Oil as the Preferred Choice:
- Silicone oil is widely used in diffusion pumps because of its high vapor point, which allows it to operate effectively at the high temperatures required for diffusion pump operation.
- Its chemical stability ensures minimal degradation over time, reducing the need for frequent oil changes and maintenance.
- Silicone oil has a relatively low toxicity and flammability profile, making it safer to handle compared to other types of oils.
-
High Vapor Point and Stability:
- The high vapor point of silicone oil is crucial for maintaining consistent performance in diffusion pumps. It ensures that the oil can withstand the high temperatures generated during operation without breaking down or forming harmful byproducts.
- Stability under high temperatures also means that silicone oil can provide reliable performance over extended periods, contributing to the longevity of the pump and reducing downtime.
-
Safety Considerations:
- Silicone oil is less toxic and less flammable than many alternative oils, making it a safer option for use in laboratory and industrial settings.
- Its safety profile reduces the risk of accidents and health hazards, which is particularly important in environments where vacuum systems are used extensively.
-
Matching Oil to Vacuum Level:
- It is essential to select oil that is rated for the specific vacuum level required by the application. Using oil with a lower pressure rating than needed can lead to inefficiencies and increased costs without providing any additional benefits.
- High-quality silicone oil is available in various grades, allowing users to choose the most appropriate option for their specific vacuum requirements.
-
Cost and Maintenance Considerations:
- While high-quality silicone oil may have a higher initial cost, its long-term benefits, such as reduced maintenance and longer service life, often outweigh the initial investment.
- Regular maintenance, including monitoring oil quality and replacing it as needed, is essential to ensure the continued performance of the diffusion pump.
In summary, silicone oil is the preferred choice for diffusion pumps due to its high vapor point, stability, and safety profile. Selecting the right oil for the specific vacuum level and ensuring regular maintenance are key to maximizing the performance and longevity of the diffusion pump.
Summary Table:
Key Feature | Benefits |
---|---|
High Vapor Point | Ensures effective operation at high temperatures, reducing breakdown risks. |
Chemical Stability | Minimizes degradation, lowering maintenance needs and costs. |
Safety Profile | Low toxicity and flammability, enhancing workplace safety. |
Vacuum Level Matching | High-quality grades available for specific vacuum requirements. |
Cost Efficiency | Long-term savings through reduced maintenance and extended pump life. |
Ready to optimize your diffusion pump performance? Contact us today for expert advice and high-quality silicone oil solutions!