Argon is widely used in magnetron sputtering due to its unique properties that make it ideal for the process. It is an inert gas, meaning it does not react with the target material or other elements, ensuring a clean and uncontaminated deposition process. Argon's relatively high atomic weight allows it to efficiently transfer kinetic energy during collisions in the plasma, which is crucial for ejecting atoms from the target material. Additionally, argon is cost-effective and readily available in high purity, making it a practical choice for industrial applications. Its inert nature also prevents unwanted chemical reactions, ensuring the integrity of the deposited thin film.
Key Points Explained:
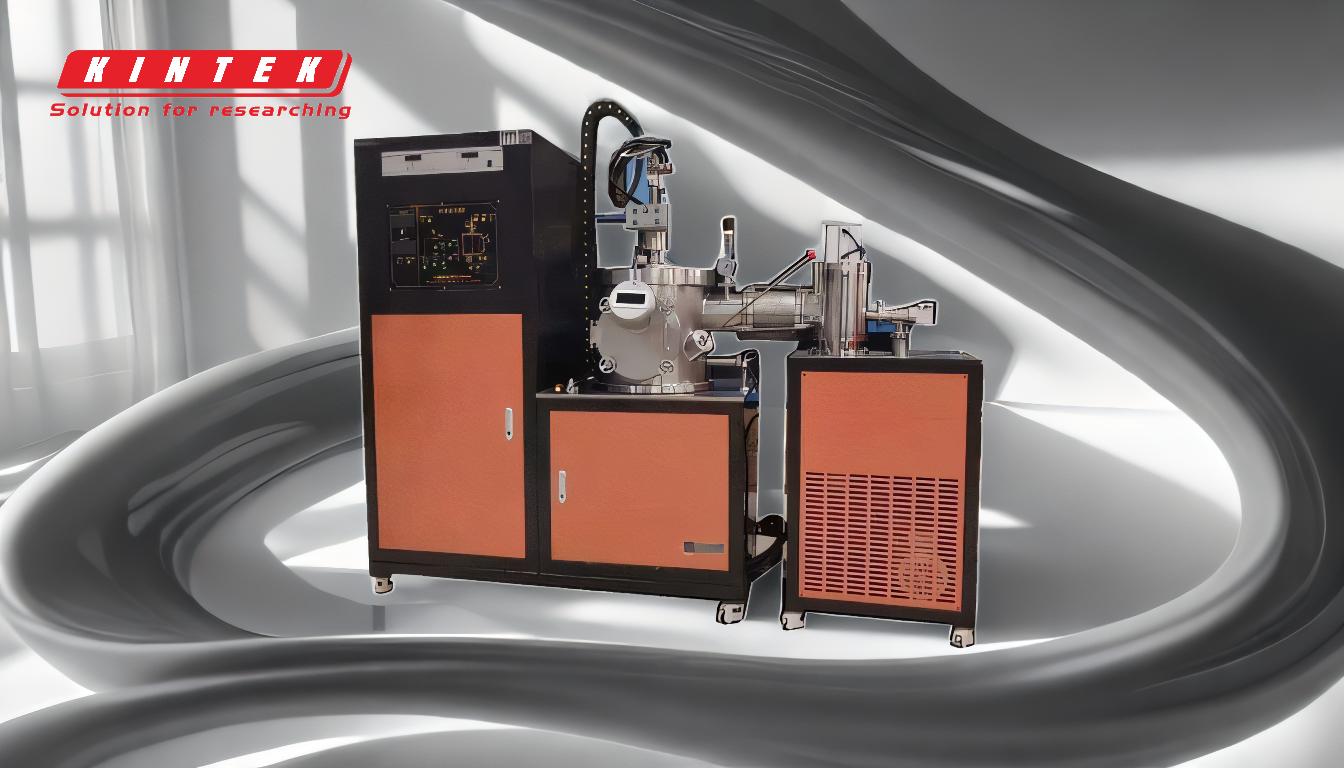
-
Inert Nature of Argon:
- Argon is a noble gas, which means it is chemically inert and does not react with the target material or other elements in the sputtering chamber.
- This inertness ensures that the deposition process remains clean and free from contamination, which is critical for producing high-quality thin films.
- Reactive gases like oxygen could cause undesired chemical reactions with the target material, altering the composition of the deposited film.
-
High Sputtering Rate:
- Argon has a relatively high atomic weight compared to other inert gases, which makes it more effective in transferring kinetic energy during high-energy collisions in the plasma.
- This high energy transfer is essential for efficiently ejecting atoms from the target material, leading to a higher sputtering rate.
- The efficiency of argon in sputtering makes it a preferred choice over other gases, even though other rare gases like Krypton (Kr) and Xenon (Xe) can also be used.
-
Cost-Effectiveness and Availability:
- Argon is relatively inexpensive compared to other inert gases, making it a cost-effective option for industrial applications.
- It is also readily available in high purity, which is important for ensuring consistent and reliable sputtering processes.
- The combination of low cost and high availability makes argon a practical choice for large-scale manufacturing processes.
-
Ionization and Plasma Formation:
- In the magnetron sputtering process, argon gas is ionized to form a plasma. The high-energy collisions in the plasma ionize the argon atoms, creating positively charged ions.
- These ions are then accelerated towards the target material, where they collide with the surface, ejecting atoms from the target.
- The ejected atoms then condense on the substrate, forming a thin film. Argon's ability to efficiently ionize and form a stable plasma is crucial for the sputtering process.
-
Prevention of Unwanted Reactions:
- The use of argon ensures that the sputtering process is free from unwanted chemical reactions that could occur if reactive gases were used.
- This is particularly important when depositing materials that are sensitive to oxidation or other chemical changes.
- By using argon, manufacturers can ensure that the deposited film retains the desired properties and composition.
-
Comparison with Other Gases:
- While other inert gases like Krypton and Xenon can also be used in sputtering, they are generally more expensive and less readily available than argon.
- Argon strikes a balance between effectiveness and cost, making it the most commonly used gas in magnetron sputtering.
- The choice of gas can also depend on the specific requirements of the deposition process, such as the need for higher energy transfer or the avoidance of certain chemical reactions.
In summary, argon's inert nature, high sputtering rate, cost-effectiveness, and availability make it the ideal choice for magnetron sputtering. Its ability to form a stable plasma and prevent unwanted chemical reactions ensures a clean and efficient deposition process, which is essential for producing high-quality thin films in various industrial applications.
Summary Table:
Key Benefits of Argon in Magnetron Sputtering |
---|
Inert Nature - Prevents unwanted chemical reactions, ensuring clean deposition. |
High Sputtering Rate - Efficient energy transfer for faster atom ejection. |
Cost-Effective - Affordable and widely available in high purity. |
Stable Plasma Formation - Ensures consistent and reliable thin film deposition. |
Prevents Contamination - Maintains film integrity by avoiding oxidation. |
Interested in optimizing your magnetron sputtering process? Contact our experts today to learn more about using argon for high-quality thin film deposition!