Evaporation is faster in a vacuum due to the reduced pressure, which lowers the boiling point of the liquid, allowing it to evaporate at lower temperatures. Additionally, the absence of air molecules in a vacuum minimizes collisions between the evaporating particles and the surrounding gas, enabling the particles to travel directly to the target without interference. This results in a more efficient and faster evaporation process, often used in applications like thin-film deposition and rotary evaporation to ensure high-quality outcomes.
Key Points Explained:
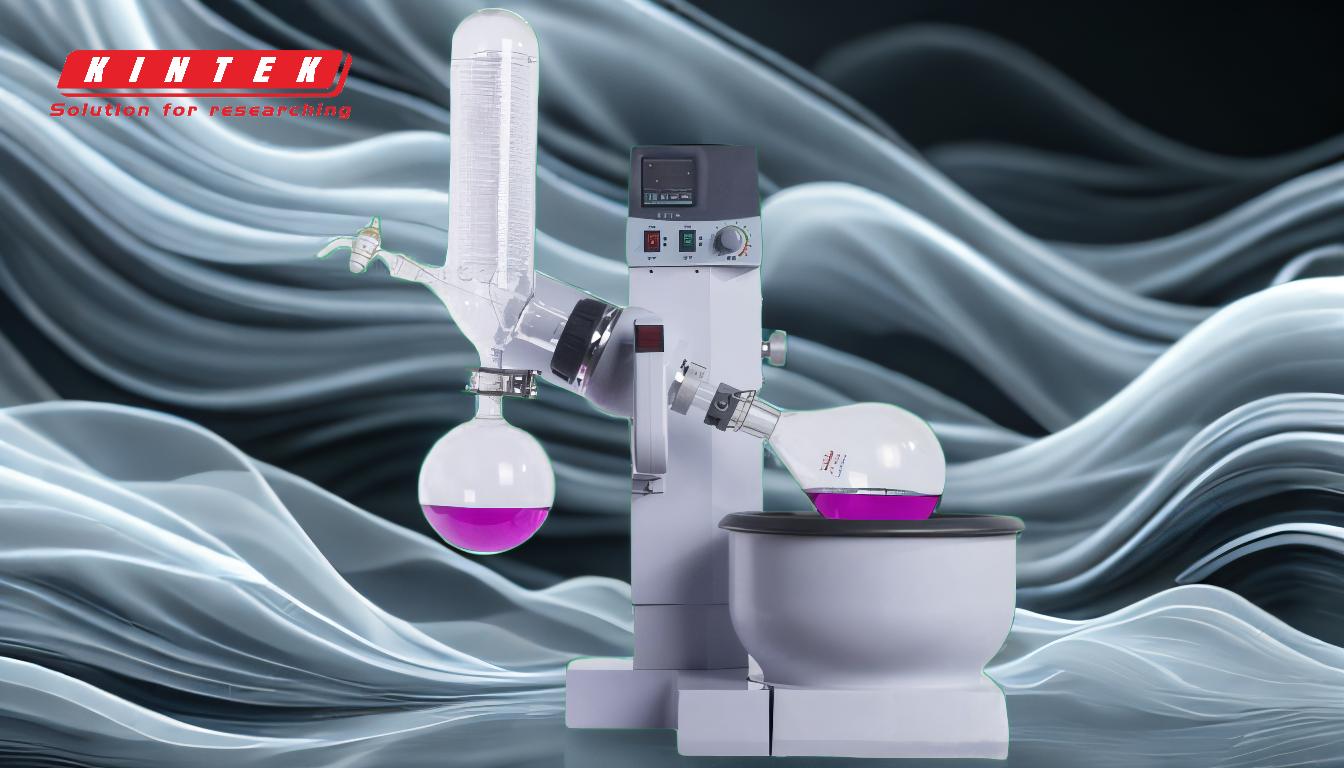
-
Reduced Pressure Lowers Boiling Point:
- In a vacuum, the pressure is significantly lower than atmospheric pressure. This reduction in pressure lowers the boiling point of the liquid, meaning it requires less heat to reach its boiling point and begin evaporating. For example, water boils at 100°C at standard atmospheric pressure but can boil at much lower temperatures in a vacuum.
- This principle is crucial in processes like rotary evaporation, where solvents need to be evaporated at lower temperatures to avoid damaging heat-sensitive materials.
-
Minimized Collisions with Gas Molecules:
- In a vacuum, the number of air molecules is drastically reduced. This means that when a liquid evaporates, the escaping molecules are less likely to collide with gas molecules in the surrounding environment.
- Fewer collisions allow the evaporated particles to travel more directly and quickly to their target, whether it's a condenser in a rotary evaporator or a substrate in thin-film deposition. This direct path enhances the efficiency and speed of the evaporation process.
-
Prevention of Contamination:
- Operating in a vacuum ensures that the environment is free from unwanted particles and gases that could contaminate the process. For instance, in thin-film deposition, any foreign particles could degrade the quality of the film.
- By maintaining a vacuum, only the source material is allowed to evaporate and deposit, ensuring a clean and high-quality result. This is particularly important in industries like semiconductor manufacturing, where purity is critical.
-
Enhanced Control Over Evaporation Parameters:
- In a vacuum, parameters such as temperature and pressure can be more precisely controlled. For example, in a rotary evaporator, adjusting the vacuum level allows for fine-tuning the evaporation rate to match the specific requirements of the solvent being evaporated.
- This control is essential for optimizing the process, especially when dealing with volatile or heat-sensitive substances that require careful handling to prevent degradation.
-
Application in Specific Processes:
- Rotary Evaporation: In this process, a vacuum is applied to lower the boiling point of the solvent, allowing it to evaporate at a lower temperature. The rotation of the flask increases the surface area of the liquid, further enhancing the evaporation rate.
- Thin-Film Deposition: Here, evaporation in a vacuum ensures that the material is deposited uniformly and without contamination, which is crucial for creating high-quality thin films used in electronics and optics.
By understanding these key points, it becomes clear why evaporation is faster and more efficient in a vacuum. The combination of reduced pressure, minimized collisions, and enhanced control over environmental factors makes vacuum evaporation a preferred method in many scientific and industrial applications.
Summary Table:
Key Factor | Explanation |
---|---|
Reduced Pressure | Lowers boiling point, enabling evaporation at lower temperatures. |
Minimized Collisions | Fewer air molecules allow particles to travel directly, speeding up evaporation. |
Prevention of Contamination | Ensures a clean environment, critical for high-quality outcomes. |
Enhanced Control | Precise adjustment of temperature and pressure for optimized evaporation. |
Applications | Rotary evaporation, thin-film deposition, and more. |
Want to learn more about vacuum evaporation and its applications? Contact us today for expert guidance!