Sputtering in scanning electron microscopy (SEM) is a critical process used to prepare non-conductive or poorly conductive specimens for imaging. By depositing a thin layer of conductive material (e.g., gold, platinum, or carbon) onto the sample, sputtering prevents charging effects caused by the electron beam, enhances secondary electron emission, and improves the signal-to-noise ratio, resulting in higher-quality images. This process is particularly important for beam-sensitive and non-conductive materials, as it protects the sample from damage and ensures accurate imaging at nanometer scales. Sputtering also enables the use of X-ray spectroscopy by providing a conductive layer that does not interfere with elemental analysis.
Key Points Explained:
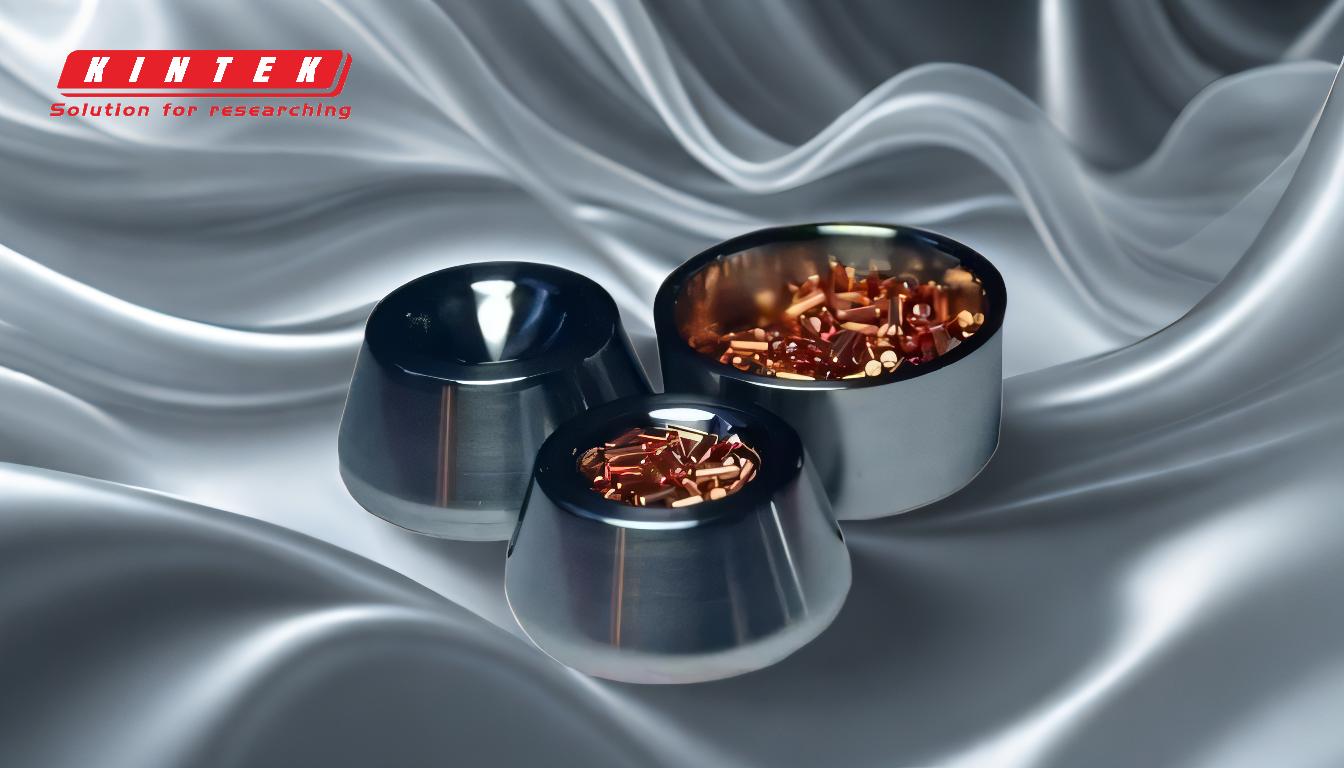
-
Preventing Charging Effects:
- Non-conductive or poorly conductive samples can accumulate electrons when exposed to the electron beam in SEM, leading to charging effects. These effects distort the image and can damage the sample.
- Sputtering deposits a thin conductive layer (2–20 nm) on the sample, providing a pathway for excess electrons to dissipate, thereby preventing charging.
-
Enhancing Secondary Electron Emission:
- Secondary electrons are crucial for creating high-resolution images in SEM. Non-conductive materials often have low secondary electron emission, resulting in poor image quality.
- The conductive coating applied during sputtering enhances secondary electron emission, improving the clarity and detail of the SEM images.
-
Improving Signal-to-Noise Ratio:
- A higher signal-to-noise ratio is essential for producing clear, high-quality SEM images. Sputtering increases the conductivity of the sample, reducing noise and enhancing the signal from secondary electrons.
- This improvement is particularly beneficial for imaging fine details at nanometer scales.
-
Protecting Beam-Sensitive Materials:
- Some samples, such as biological specimens or polymers, are sensitive to the electron beam and can be damaged during imaging.
- The thin conductive layer acts as a protective barrier, reducing beam damage and enabling longer imaging sessions without compromising the sample's integrity.
-
Enabling X-ray Spectroscopy:
- For X-ray spectroscopy, a carbon coating is often preferred over metal coatings because it does not interfere with the elemental analysis of the sample.
- Sputtering with carbon provides a conductive layer that allows for accurate X-ray spectroscopy while maintaining the sample's structural integrity.
-
Material Choices for Sputtering:
- Common materials used for sputtering include gold, gold/palladium alloys, platinum, silver, chromium, iridium, and carbon.
- The choice of material depends on the specific application, such as the need for high conductivity (metals) or compatibility with X-ray spectroscopy (carbon).
-
Applications in Biological and Non-Conductive Samples:
- Biological samples, which are typically non-conductive, require sputtering to ensure clear imaging at nanometer scales.
- Non-conductive materials, such as ceramics or polymers, also benefit from sputtering to prevent charging and improve image quality.
-
Process Details:
- Sputtering involves placing the sample in a vacuum chamber and bombarding a target material (e.g., gold or platinum) with ions, causing atoms from the target to be ejected and deposited onto the sample.
- The thickness of the sputtered layer is carefully controlled (typically 2–20 nm) to ensure optimal conductivity without obscuring fine surface details.
By addressing these key points, sputtering ensures that SEM imaging is accurate, high-resolution, and free from artifacts caused by charging or beam damage. This process is indispensable for a wide range of materials, particularly those that are non-conductive or beam-sensitive.
Summary Table:
Key Benefits of Sputtering in SEM | Details |
---|---|
Prevents Charging Effects | Deposits a thin conductive layer (2–20 nm) to dissipate excess electrons. |
Enhances Secondary Electron Emission | Improves image clarity and detail for non-conductive materials. |
Improves Signal-to-Noise Ratio | Reduces noise, enabling high-quality imaging at nanometer scales. |
Protects Beam-Sensitive Materials | Acts as a barrier to reduce beam damage during imaging. |
Enables X-ray Spectroscopy | Carbon coatings allow accurate elemental analysis without interference. |
Material Choices | Gold, platinum, carbon, and more, depending on application needs. |
Applications | Ideal for biological and non-conductive samples like ceramics and polymers. |
Process Details | Conducted in a vacuum chamber with precise thickness control (2–20 nm). |
Optimize your SEM imaging with sputtering—contact our experts today for tailored solutions!