Carburizing is a heat treatment process that involves adding carbon to the surface of steel to enhance its hardness and wear resistance. Steel containing carbon, particularly low-carbon steels, is commonly used for carburizing. This process creates a hard, wear-resistant surface while maintaining a softer, more ductile core, making it ideal for applications requiring both durability and toughness. The process is widely used in industries such as automotive, aerospace, and tool manufacturing. Below, we explore the key aspects of why carbon-containing steel is suitable for carburizing and how the process benefits the material.
Key Points Explained:
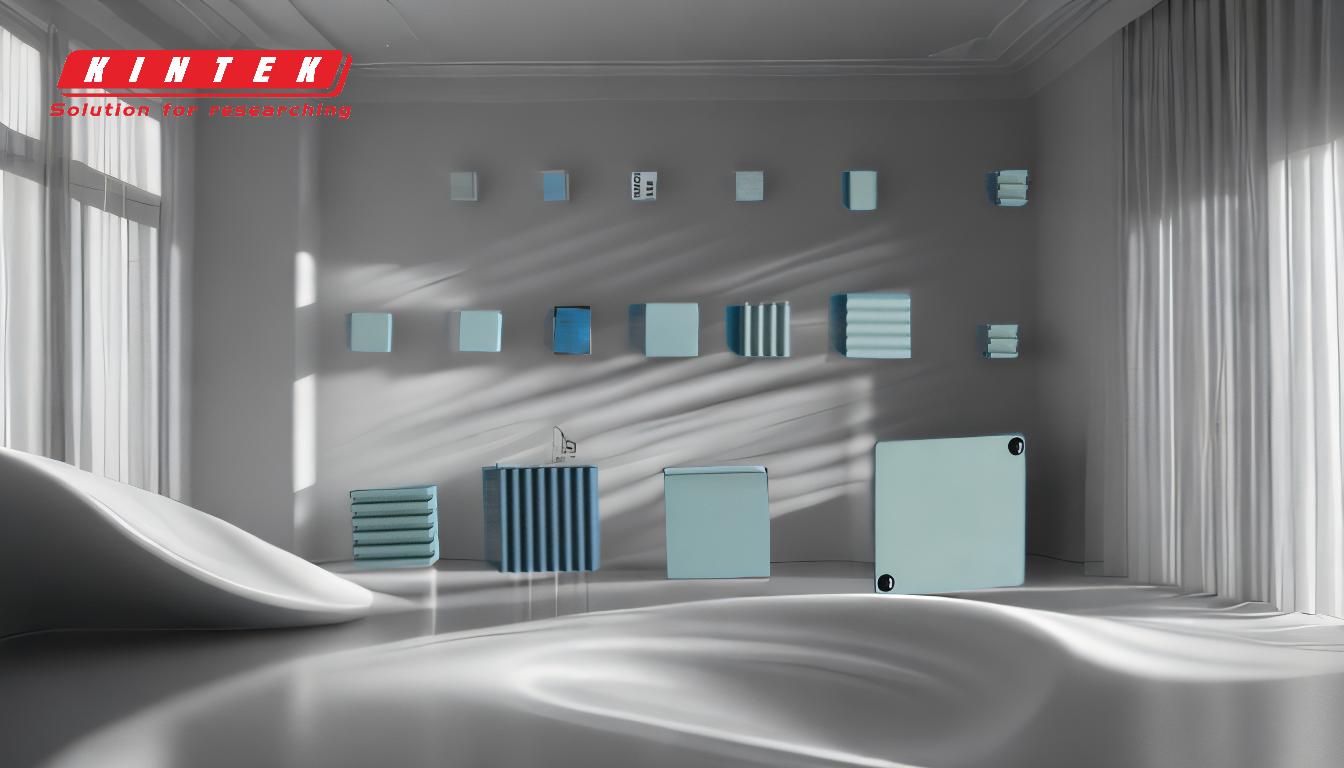
-
What is Carburizing?
- Carburizing is a thermochemical process that introduces carbon into the surface of steel. This is typically done by heating the steel in a carbon-rich environment (e.g., gas, liquid, or solid medium) at high temperatures (usually between 850°C and 950°C).
- The carbon diffuses into the surface of the steel, increasing its carbon concentration and forming a hardened layer. The core of the steel remains relatively soft and ductile.
-
Why is Carbon-Containing Steel Used for Carburizing?
- Carbon-containing steels, particularly low-carbon steels (e.g., 1018, 1020), are ideal for carburizing because their low initial carbon content (typically 0.1% to 0.3%) allows for effective carbon diffusion during the process.
- The addition of carbon to the surface increases hardness and wear resistance, while the low-carbon core retains its toughness and ductility.
-
Benefits of Carburizing Carbon-Containing Steel:
- Surface Hardness: The carburized layer can achieve high hardness levels, making the steel suitable for applications requiring wear resistance, such as gears, shafts, and bearings.
- Ductile Core: The core remains soft and ductile, providing toughness and resistance to impact and fatigue.
- Precision Control: The depth of the carburized layer can be precisely controlled, allowing for tailored material properties based on specific application requirements.
-
Comparison with Alloy Steels:
- While carbon steels are commonly used for carburizing, alloy steels (e.g., 38CrMoAlA) are more suitable for processes like gas nitriding due to their ability to form stable nitrides (e.g., AlN, CrN). These nitrides provide high hardness and wear resistance but are not typically used in carburizing.
- Carbon steels are preferred for carburizing because they lack alloying elements that could interfere with the carbon diffusion process.
-
Applications of Carburized Steel:
- Automotive Industry: Carburized steel is used for gears, camshafts, and other components requiring high surface hardness and wear resistance.
- Tool Manufacturing: Tools and dies benefit from the long-wearing surfaces created by carburizing, as mentioned in the reference about Low Pressure Carburizing.
- Aerospace and Machinery: Components subjected to high stress and wear, such as bearings and shafts, often use carburized steel.
-
Process Variations:
- Gas Carburizing: Involves heating the steel in a carbon-rich gas atmosphere, such as methane or propane.
- Liquid Carburizing: Uses a molten salt bath containing carbon-rich compounds.
- Solid Carburizing: Employs a solid carbon medium, such as charcoal, packed around the steel parts.
- Low Pressure Carburizing (LPC): A modern method that uses a vacuum environment to achieve precise carbon diffusion, reducing oxidation and distortion.
-
Limitations of Carburizing:
- Distortion: The high temperatures involved in carburizing can cause distortion in thin or complex parts.
- Cost: The process can be expensive due to the energy and materials required.
- Limited to Low-Carbon Steels: High-carbon steels are not suitable for carburizing because their carbon content is already too high to allow effective diffusion.
-
Conclusion:
- Steel containing carbon, particularly low-carbon steels, is widely used for carburizing due to its ability to achieve a hard, wear-resistant surface while maintaining a tough and ductile core. This makes it an ideal choice for applications requiring both durability and toughness. While alloy steels are better suited for processes like gas nitriding, carbon steels remain the preferred material for carburizing due to their compatibility with the carbon diffusion process.
Summary Table:
Aspect | Details |
---|---|
Process | Thermochemical process adding carbon to steel surface for hardness. |
Ideal Steel Type | Low-carbon steels (e.g., 1018, 1020) with 0.1% to 0.3% carbon content. |
Key Benefits | High surface hardness, wear resistance, and a tough, ductile core. |
Applications | Automotive gears, aerospace components, tools, and machinery parts. |
Process Variations | Gas, liquid, solid, and low-pressure carburizing methods. |
Limitations | Distortion risks, higher costs, and limited to low-carbon steels. |
Learn how carburizing can improve your steel components—contact our experts today!