Pyrolysis reactors can indeed be used for the pyrolysis of plastic waste, but their suitability depends on the type of reactor, the specific type of plastic waste, and the desired outcomes. Horizontal-type pyrolysis reactors are particularly well-suited for processing plastics and tires due to their efficiency and environmental performance. However, not all plastics are suitable for pyrolysis, as some, like PVC and PET, release toxic gases during the process. The process involves heating plastic waste in an oxygen-free, high-temperature environment to convert it into fuel oil, contributing to waste recycling and environmental sustainability. Different reactor designs, such as fluidized bed, fixed bed, and rotary cone reactors, offer varying efficiencies and are used in batch or continuous systems.
Key Points Explained:
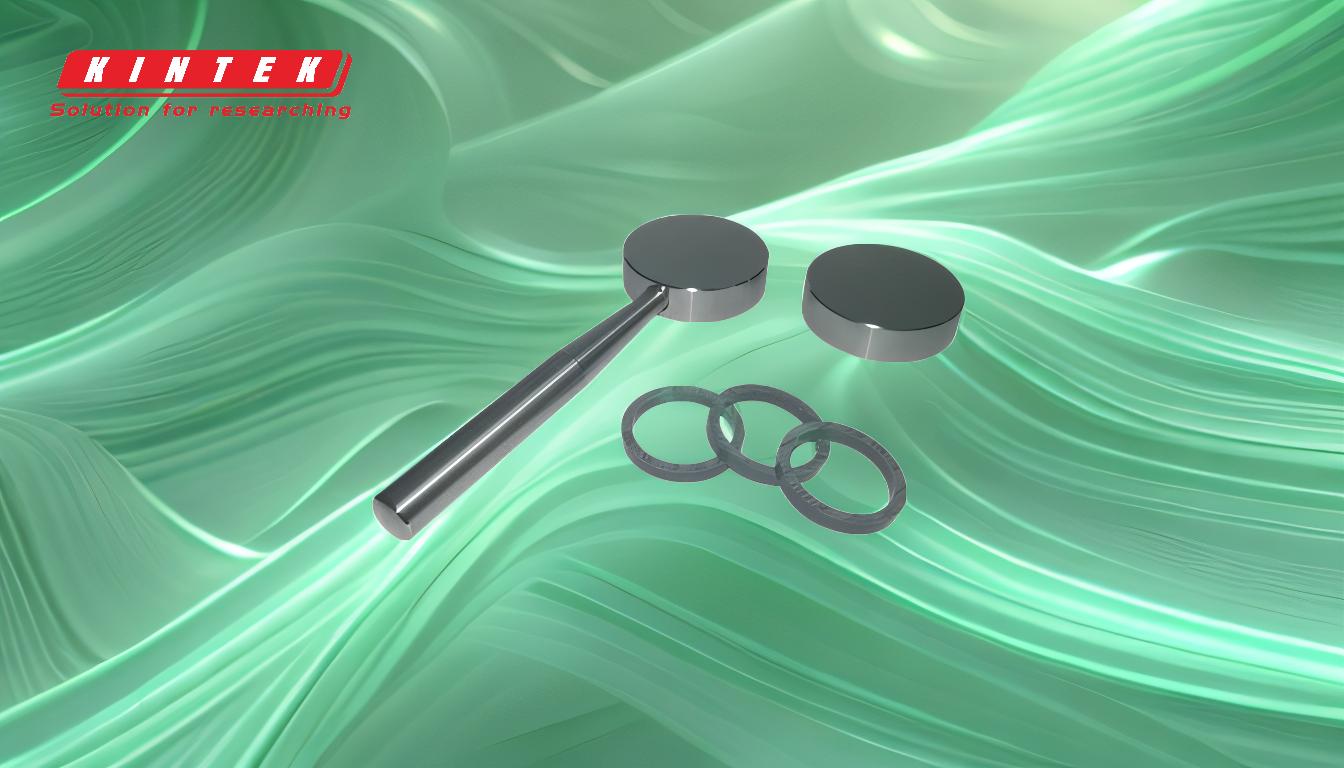
-
Types of Pyrolysis Reactors Suitable for Plastic Waste:
- Horizontal-Type Reactors: These are specifically mentioned as more suitable for the pyrolysis of plastics and tires. They offer better working efficiency and environmental performance compared to vertical-type reactors, which are being phased out.
- Other Reactor Types: Fluidized bed (bubbling and circulating), fixed bed, jet bed, rotary cylinder, cyclonic reactor, and rotary cone reactors are also used for pyrolysis. These can operate in batch or continuous systems, depending on the scale and requirements of the process.
-
Suitability of Plastic Waste for Pyrolysis:
- Suitable Plastics: Post-consumer plastics, municipal solid waste segregated plastics, reject of mechanical recycling, multi-layer packaging, and mixed PET/PVC contaminated plastics can be processed through pyrolysis.
- Unsuitable Plastics: PVC and PET are not suitable for pyrolysis due to the production of toxic gases during the process. This limitation necessitates careful selection and segregation of plastic waste before pyrolysis.
-
Environmental and Efficiency Considerations:
- Pollution-Free Process: Pyrolysis reactors are designed to operate in an oxygen-free, high-temperature environment, minimizing the release of harmful emissions and contributing to a pollution-free and eco-friendly waste management solution.
- Efficiency: The choice of reactor type significantly impacts the efficiency of the pyrolysis process. Horizontal-type reactors, for example, are preferred for their superior performance in handling plastic waste.
-
Applications and Benefits:
- Fuel Oil Production: The primary output of plastic waste pyrolysis is fuel oil, which can be used as an energy source, thereby recycling waste and reducing reliance on fossil fuels.
- Waste Management: Pyrolysis offers a sustainable solution for managing difficult-to-recycle plastics, helping to reduce landfill use and environmental pollution.
-
Operational Considerations:
- Batch vs. Continuous Systems: The choice between batch and continuous systems depends on the scale of operation and the specific requirements of the waste management process. Continuous systems are generally more efficient for large-scale operations, while batch systems may be suitable for smaller, more controlled processes.
- Safety Measures: Given the potential release of toxic gases from unsuitable plastics, safety measures and proper waste segregation are critical to the successful and safe operation of pyrolysis reactors.
In summary, pyrolysis reactors, particularly horizontal-type reactors, are effective for the pyrolysis of suitable plastic waste, offering environmental benefits and contributing to sustainable waste management. However, careful consideration of reactor type, plastic waste suitability, and operational parameters is essential to maximize efficiency and safety.
Summary Table:
Aspect | Details |
---|---|
Suitable Reactor Types | Horizontal-type, fluidized bed, fixed bed, rotary cone, and others. |
Suitable Plastics | Post-consumer plastics, municipal waste, multi-layer packaging, and more. |
Unsuitable Plastics | PVC and PET (release toxic gases). |
Key Benefits | Fuel oil production, pollution-free process, sustainable waste management. |
Operational Systems | Batch or continuous systems, depending on scale and requirements. |
Ready to explore pyrolysis solutions for your plastic waste? Contact us today to get started!