Milling is a process that can reduce particle size, as evidenced by the repeated observation that increasing milling cycles generally increases the number of smaller particles. This indicates that milling, particularly cryomilling, causes larger particles to break down into smaller nanosized fragments. The process steadily erodes larger particles, leading to a reduction in their size over time.
Key Points Explained:
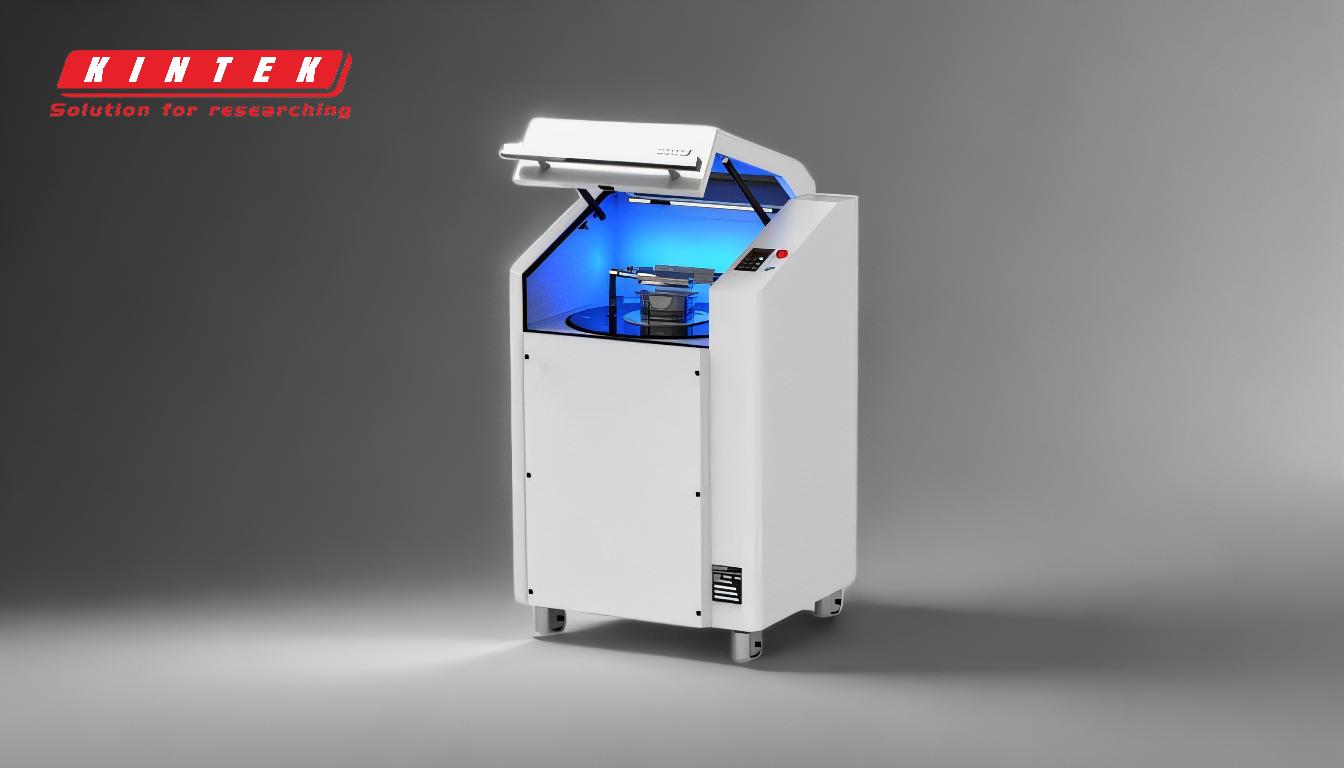
-
Milling Reduces Particle Size:
- Milling, especially cryomilling, is effective in breaking down larger particles into smaller ones.
- The repeated reference to increasing milling cycles leading to more smaller particles underscores this point.
-
Mechanism of Particle Size Reduction:
- During milling, small nanosized fragments break off from larger particles.
- This process of fragmentation and erosion continues with each milling cycle, steadily reducing the size of the particles.
-
Impact of Increasing Milling Cycles:
- The more milling cycles performed, the greater the reduction in particle size.
- This is because each cycle further breaks down the particles, increasing the number of smaller fragments.
-
Cryomilling Specifics:
- Cryomilling, a type of milling performed at cryogenic temperatures, is particularly effective in reducing particle size.
- The low temperatures can make materials more brittle, facilitating easier fragmentation.
-
Practical Implications:
- For equipment and consumable purchasers, understanding that milling can reduce particle size is crucial for selecting the right milling equipment and determining the number of cycles needed to achieve the desired particle size.
- This knowledge can help in optimizing processes and ensuring the quality of the final product.
In summary, milling, particularly cryomilling, is a proven method for reducing particle size by breaking down larger particles into smaller fragments. The number of milling cycles directly impacts the extent of particle size reduction, making it an essential consideration for those involved in material processing and equipment selection.
Summary Table:
Key Aspect | Description |
---|---|
Milling Reduces Particle Size | Breaks down larger particles into smaller ones, especially effective with cryomilling. |
Mechanism of Reduction | Fragmentation and erosion occur during milling, creating nanosized fragments. |
Impact of Milling Cycles | More cycles lead to greater particle size reduction. |
Cryomilling Advantages | Low temperatures make materials brittle, enhancing fragmentation efficiency. |
Practical Applications | Essential for selecting milling equipment and optimizing material processing. |
Ready to optimize your milling process? Contact our experts today for tailored solutions!