Increasing the pressure in a reactor is a critical aspect of many chemical and industrial processes. The pressure can be increased through various methods, including heating, agitation, manual pressurization, and leveraging the reaction itself. Each method has its own advantages and considerations, and the choice depends on the specific requirements of the reaction and the safety measures in place. Pressure relief valves are essential to ensure that the pressure does not exceed safe limits, preventing potential hazards.
Key Points Explained:
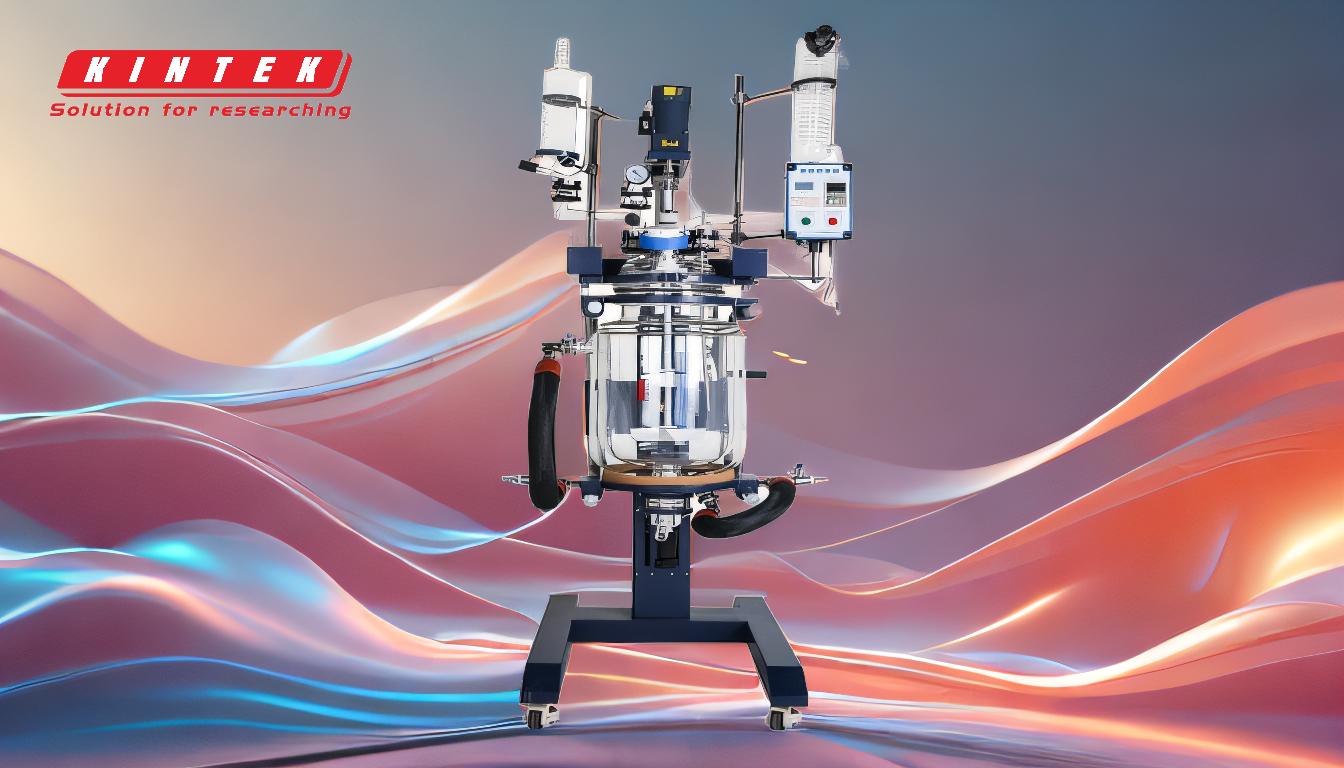
-
Heating the Reactor:
- Mechanism: Heating a sealed pressure vessel increases the temperature of the gases or liquids inside, which in turn increases the pressure due to the ideal gas law (PV=nRT). As the temperature rises, the molecules move faster and exert more force on the walls of the reactor.
- Advantages: This method is straightforward and can be easily controlled by adjusting the heat source. It is particularly useful for reactions that benefit from higher temperatures.
- Considerations: Heating must be done carefully to avoid overheating, which could lead to unsafe pressure levels or damage to the reactor. Additionally, some materials may degrade at high temperatures.
-
Agitation:
- Mechanism: Agitation involves stirring or mixing the contents of the reactor. This can increase the pressure by accelerating the reaction rate, especially if the reaction itself generates gas or heat.
- Advantages: Agitation can enhance the uniformity of the reaction, leading to more consistent pressure increases. It is particularly useful in reactions where mixing is critical.
- Considerations: The design of the agitator and the speed of mixing must be carefully controlled to avoid excessive pressure buildup or mechanical stress on the reactor.
-
Manual Pressurization:
- Mechanism: Manual pressurization involves introducing a pressurized gas (such as nitrogen or argon) into the reactor using a compressor or a pre-compressed canister. This directly increases the pressure inside the reactor.
- Advantages: This method provides precise control over the pressure and is useful when the reaction does not generate sufficient pressure on its own or when heating is not appropriate.
- Considerations: The gas used must be inert to avoid unwanted reactions. Additionally, the equipment for pressurization must be properly maintained to prevent leaks or failures.
-
Reaction-Induced Pressure:
- Mechanism: Some chemical reactions naturally produce gas or heat, which can increase the pressure inside the reactor. For example, decomposition reactions or gas-evolving reactions can lead to pressure increases.
- Advantages: This method leverages the reaction itself, reducing the need for external energy sources. It can be highly efficient if the reaction is well-understood and controlled.
- Considerations: The reaction kinetics must be carefully monitored to ensure that the pressure does not rise too quickly or exceed safe limits. Safety measures, such as pressure relief valves, are essential.
-
Safety Measures - Pressure Relief Valves:
- Mechanism: Pressure relief valves are designed to open at a predetermined pressure, allowing excess gas or liquid to escape and thus preventing the pressure from exceeding safe levels.
- Advantages: These valves are critical for maintaining safety in high-pressure reactors. They provide a fail-safe mechanism to prevent explosions or other hazards.
- Considerations: The valves must be regularly inspected and maintained to ensure they function correctly. The set pressure must be carefully chosen based on the reactor's design and the specific reaction conditions.
-
Material and Design Considerations:
- Mechanism: High-pressure reactors are made from sturdy materials (such as stainless steel or specialized alloys) that can withstand high pressures and temperatures. The design includes safety features like reinforced walls, seals, and pressure relief systems.
- Advantages: Robust materials and design ensure the reactor can handle the increased pressure without failure. This is crucial for both safety and the longevity of the equipment.
- Considerations: The choice of materials and design must be tailored to the specific reaction conditions, including the maximum expected pressure and temperature. Regular maintenance and inspection are necessary to ensure the integrity of the reactor.
In summary, increasing the pressure in a reactor can be achieved through various methods, each with its own set of advantages and considerations. The choice of method depends on the specific requirements of the reaction, the design of the reactor, and the safety measures in place. Proper control and monitoring are essential to ensure that the pressure remains within safe limits and that the reaction proceeds as intended.
Summary Table:
Method | Mechanism | Advantages | Considerations |
---|---|---|---|
Heating | Increases temperature, raising pressure via ideal gas law (PV=nRT). | Easy to control; useful for high-temperature reactions. | Risk of overheating; material degradation at high temperatures. |
Agitation | Stirring accelerates reaction rate, increasing pressure if gas/heat is generated. | Enhances reaction uniformity; ideal for mixing-critical reactions. | Requires careful control to avoid excessive pressure or mechanical stress. |
Manual Pressurization | Introduces pressurized gas (e.g., nitrogen) to directly increase pressure. | Precise control; suitable for reactions lacking self-generated pressure. | Requires inert gas; equipment maintenance is crucial to prevent leaks/failures. |
Reaction-Induced | Leverages gas/heat produced by the reaction to increase pressure. | Efficient; reduces need for external energy sources. | Requires careful monitoring to avoid rapid pressure spikes; safety valves needed. |
Pressure Relief Valves | Opens at preset pressure to release excess gas/liquid, preventing overpressure. | Critical for safety; prevents explosions and hazards. | Regular inspection and maintenance required; set pressure must be carefully chosen. |
Need help optimizing your reactor's pressure control? Contact our experts today for tailored solutions!