Calibrating a sieve shaker is a critical process to ensure accurate and consistent particle size analysis. Proper calibration involves verifying the performance of the sieve shaker and ensuring that the test sieves are in good condition. The process includes visual inspection of the sieves, checking the sieve shaker's mechanical components, and performing a test run with a known sample to validate the results. Below is a detailed explanation of the steps involved in calibrating a sieve shaker, along with key considerations for maintaining accuracy and reliability.
Key Points Explained:
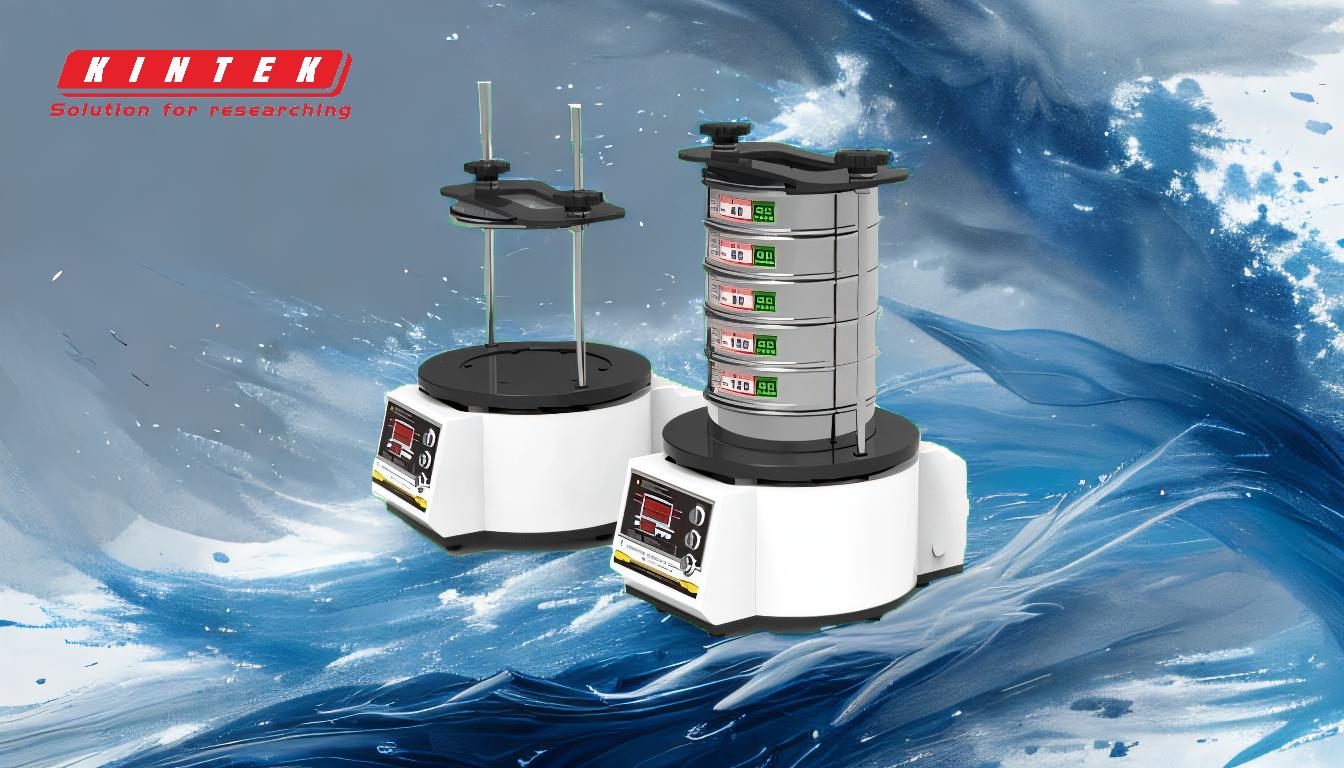
-
Visual Inspection of Test Sieves:
- Purpose: Ensure the sieves are in good condition and free from defects that could affect the sieving process.
-
Steps:
- Examine the sieve mesh for tears, holes, or wavy patterns that could distort results.
- Check the epoxy or solder around the sieve frame for cracks or damage.
- Verify that the sieve frame is not bent or deformed.
- Importance: Damaged sieves can lead to inaccurate particle size distribution results, so this step is crucial before proceeding with calibration.
-
Verify Sieve Shaker Mechanical Components:
- Purpose: Ensure the sieve shaker is functioning correctly and consistently.
-
Steps:
- Inspect the motor and drive mechanism for smooth operation.
- Check the amplitude and frequency settings to ensure they match the manufacturer's specifications.
- Confirm that the sieve stack is securely clamped and properly aligned.
- Importance: Mechanical issues can cause inconsistent sieving, leading to unreliable data.
-
Perform a Test Run with a Known Sample:
- Purpose: Validate the accuracy of the sieve shaker and sieves.
-
Steps:
- Select a sample with a known particle size distribution.
- Run the sample through the sieve shaker using the same parameters (time, amplitude, frequency) as used in regular testing.
- Compare the results with the expected distribution to identify any discrepancies.
- Importance: This step confirms that the sieve shaker and sieves are producing accurate and repeatable results.
-
Data Evaluation and Adjustment:
- Purpose: Identify and correct any deviations from expected results.
-
Steps:
- Analyze the test run data to determine if the sieve shaker or sieves need adjustment.
- If discrepancies are found, troubleshoot the issue (e.g., replace damaged sieves, recalibrate the sieve shaker settings).
- Repeat the test run until the results align with the expected distribution.
- Importance: Ensures the system is properly calibrated and ready for accurate particle size analysis.
-
Cleaning and Maintenance:
- Purpose: Maintain the accuracy and longevity of the sieves and sieve shaker.
-
Steps:
- Clean the sieves thoroughly after each use to prevent cross-contamination.
- Store sieves in a dry, safe environment to prevent damage.
- Regularly inspect and maintain the sieve shaker to ensure consistent performance.
- Importance: Proper maintenance prevents errors and extends the life of the equipment.
-
Documentation and Record-Keeping:
- Purpose: Maintain a record of calibration and maintenance activities for quality control and traceability.
-
Steps:
- Document the results of each calibration test run.
- Record any adjustments made to the sieve shaker or sieves.
- Keep a log of maintenance activities and inspections.
- Importance: Documentation ensures accountability and provides a reference for future calibrations.
By following these steps, you can ensure that your sieve shaker is properly calibrated and capable of delivering accurate and reliable particle size analysis results. Regular calibration and maintenance are essential for maintaining the integrity of your sieving process and ensuring high-quality data.
Summary Table:
Step | Purpose | Key Actions | Importance |
---|---|---|---|
Visual Inspection | Ensure sieves are defect-free | Examine mesh for tears, check frame for cracks, verify alignment | Prevents inaccurate results due to damaged sieves |
Mechanical Verification | Confirm sieve shaker is functioning correctly | Inspect motor, check amplitude/frequency settings, ensure proper clamping | Avoids inconsistent sieving and unreliable data |
Test Run | Validate accuracy with a known sample | Use a sample with known distribution, compare results to expected values | Confirms sieve shaker and sieves produce accurate, repeatable results |
Data Evaluation | Identify and correct deviations | Analyze test data, troubleshoot issues, repeat test until results match expected distribution | Ensures proper calibration for accurate analysis |
Cleaning & Maintenance | Maintain equipment accuracy and longevity | Clean sieves after use, store properly, inspect sieve shaker regularly | Prevents errors and extends equipment life |
Documentation | Maintain records for quality control and traceability | Log calibration results, adjustments, and maintenance activities | Provides accountability and reference for future calibrations |
Need help calibrating your sieve shaker? Contact our experts today for personalized guidance!