Increasing ball mill efficiency involves optimizing several factors that influence grinding performance. These include the drum dimensions (diameter and length), the ratio of drum diameter to length, the physical and chemical properties of the feed material, the size and filling of grinding balls, the shape of the armor surface, rotation speed, milling fineness, and the timely removal of the ground product. Additionally, factors such as the residence time of material in the mill, the feed rate, and the nature of the grinding material play a crucial role. By carefully adjusting these parameters, the efficiency of the ball mill can be significantly improved, leading to better productivity and reduced energy consumption.
Key Points Explained:
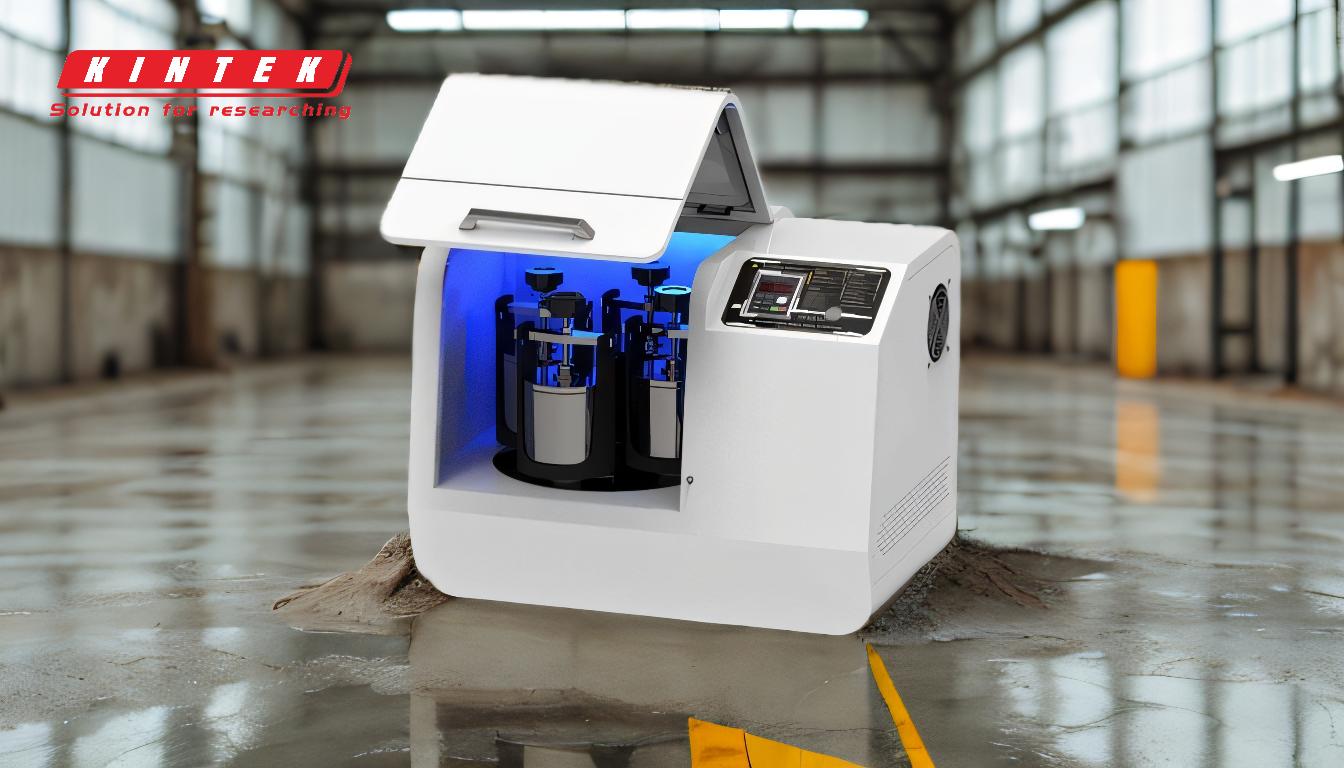
-
Optimize Drum Dimensions and L:D Ratio:
- Drum Diameter: Larger drum diameters can increase the mill's capacity and grinding efficiency.
- Length to Diameter (L:D) Ratio: The optimal L:D ratio for ball mills is between 1.56 and 1.64. This ratio ensures efficient grinding by providing the right balance between the length and diameter of the drum, which affects the residence time of the material and the grinding action.
-
Adjust Ball Filling and Sizes:
- Ball Filling: The percentage of the mill volume filled with grinding balls (filling ratio) should be optimized. Overfilling can lead to inefficient grinding, while underfilling can reduce the grinding action.
- Ball Sizes: Using a mix of different ball sizes can improve grinding efficiency. Larger balls are effective for coarse grinding, while smaller balls are better for fine grinding. A balanced mix ensures that both coarse and fine particles are effectively ground.
-
Control Rotation Speed:
- Critical Speed: The rotation speed of the mill should be close to the critical speed (the speed at which the balls begin to centrifuge). Operating at the right speed ensures that the balls cascade and impact the material effectively, leading to better grinding efficiency.
- Optimal Speed: The optimal speed is usually around 65-75% of the critical speed. This range maximizes the grinding action without causing excessive wear on the mill liners.
-
Manage Feed Material Properties:
- Physical-Chemical Properties: The hardness, density, and moisture content of the feed material can affect grinding efficiency. Softer materials grind more easily, while harder materials require more energy. Adjusting the feed rate and pre-treating the material (e.g., drying) can improve efficiency.
- Feed Rate and Level: Maintaining a consistent feed rate and level in the mill ensures steady grinding conditions. Overloading the mill can lead to inefficient grinding, while underloading can cause excessive wear on the balls and liners.
-
Optimize Milling Fineness and Product Removal:
- Milling Fineness: The desired fineness of the ground product should be balanced with the grinding efficiency. Over-grinding can waste energy, while under-grinding may not meet product specifications.
- Timely Removal of Ground Product: Efficient removal of the ground product from the mill prevents over-grinding and ensures that the mill operates at optimal capacity. This can be achieved by using appropriate discharge mechanisms (e.g., grate discharge, overflow discharge).
-
Consider Armor Surface Shape and Mill Liner Design:
- Armor Surface Shape: The shape and design of the mill liners (armor) can influence the grinding action. Smooth liners promote cascading, while ribbed or lifter liners enhance the lifting and dropping action of the balls, improving grinding efficiency.
- Liner Material: The material of the liners should be chosen based on the type of material being ground and the desired wear resistance. Harder materials like manganese steel are often used for abrasive materials.
-
Monitor and Control Residence Time:
- Residence Time: The time that material spends in the mill chamber affects the degree of grinding. Longer residence times can lead to finer grinding but may also increase energy consumption. Adjusting the feed rate and mill speed can help control residence time.
-
Regular Maintenance and Monitoring:
- Wear and Tear: Regular inspection and maintenance of the mill, including the liners and grinding balls, can prevent unexpected downtime and maintain grinding efficiency.
- Process Monitoring: Continuous monitoring of the grinding process, including particle size distribution and energy consumption, can help identify inefficiencies and allow for timely adjustments.
By systematically addressing these key factors, the efficiency of a ball mill can be significantly enhanced, leading to improved productivity, reduced energy consumption, and better overall performance.
Summary Table:
Key Factor | Optimization Tips |
---|---|
Drum Dimensions | - Larger drum diameter increases capacity. Optimal L:D ratio: 1.56–1.64. |
Ball Filling & Sizes | - Optimize filling ratio. Use a mix of ball sizes for coarse and fine grinding. |
Rotation Speed | - Operate at 65-75% of critical speed for optimal grinding action. |
Feed Material Properties | - Adjust feed rate and pre-treat materials based on hardness, density, and moisture. |
Milling Fineness & Removal | - Balance fineness with efficiency. Use proper discharge mechanisms. |
Armor Surface & Liner Design | - Use ribbed or lifter liners for better grinding. Choose durable liner materials. |
Residence Time | - Control with feed rate and mill speed to avoid over-grinding. |
Maintenance & Monitoring | - Regularly inspect liners and balls. Monitor particle size and energy consumption. |
Ready to optimize your ball mill efficiency? Contact our experts today for tailored solutions!