Increasing production in a ball mill involves optimizing various factors that influence its grinding performance. Key factors include the rotation speed, the size and type of grinding medium, the material properties, the filling ratio of the mill, and the operational parameters such as feed rate and residence time. By carefully adjusting these variables, it is possible to enhance the efficiency and output of the ball mill. This involves selecting the right ball size and density, maintaining an optimal L:D ratio, ensuring timely removal of ground product, and balancing the feed rate with the grinding capacity. Below, we explore these factors in detail to provide a comprehensive understanding of how to increase production in a ball mill.
Key Points Explained:
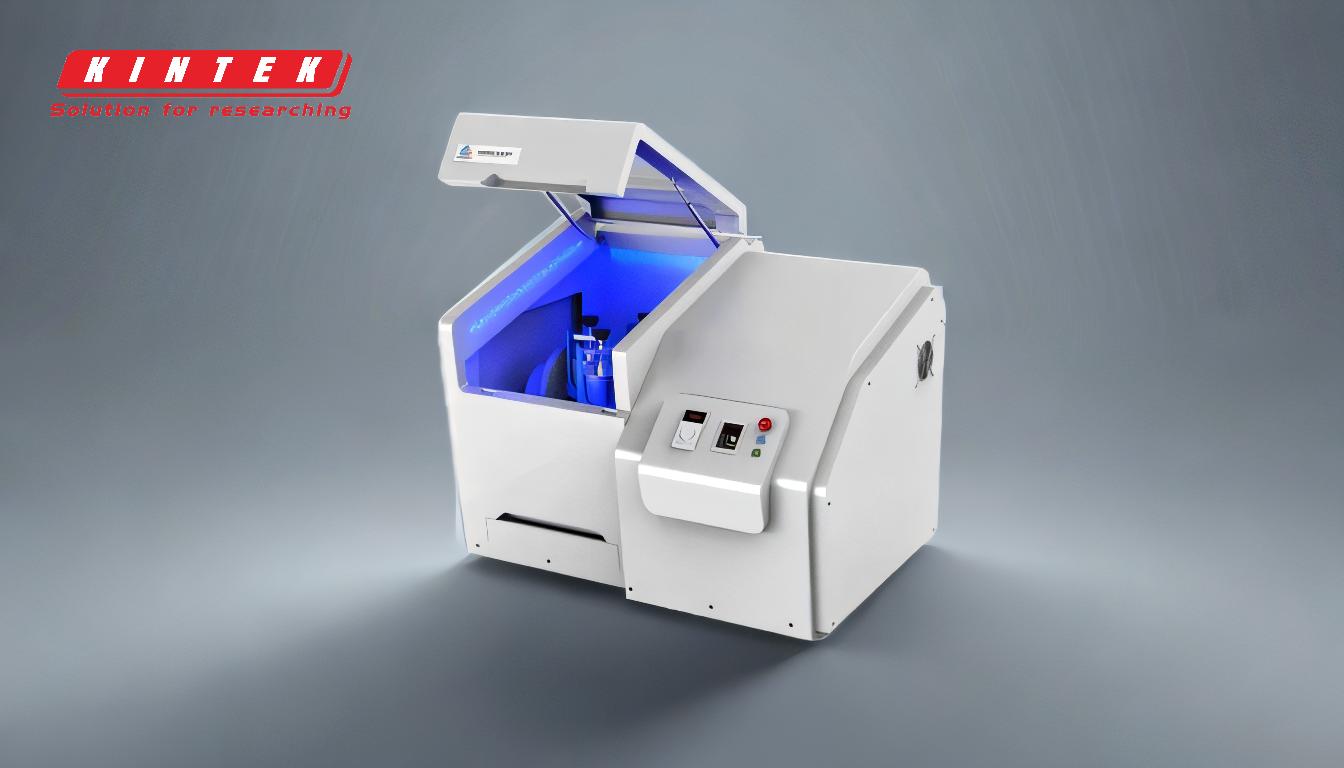
-
Optimize Rotation Speed
- The rotation speed of the ball mill directly affects the grinding efficiency.
- If the speed is too low, the balls will not be lifted high enough to create significant impact, reducing grinding efficiency.
- If the speed is too high, the balls may centrifuge, sticking to the walls of the mill and reducing grinding action.
- The optimal speed is typically 65-75% of the critical speed, where the critical speed is the speed at which the balls begin to centrifuge.
-
Select the Right Grinding Medium
- The size, density, and number of balls significantly influence grinding performance.
- Smaller balls are better for fine grinding, while larger balls are more effective for coarse grinding.
- The density of the balls should match the material being ground; denser materials require denser balls.
- Ensure an appropriate ball-to-material ratio to maximize impact and minimize wear.
-
Control the Filling Ratio
- The filling ratio refers to the percentage of the mill volume filled with grinding medium.
- An optimal filling ratio (typically 30-40%) ensures sufficient grinding action without overloading the mill.
- Overfilling can reduce grinding efficiency, while underfilling may lead to insufficient impact and wear.
-
Adjust the L:D Ratio
- The ratio of the drum length (L) to diameter (D) affects the residence time of the material in the mill.
- An optimal L:D ratio (1.56–1.64) ensures efficient grinding without excessive energy consumption.
- A longer drum increases residence time, which is beneficial for fine grinding, but may reduce throughput.
-
Manage Feed Rate and Material Properties
- The feed rate should be balanced with the grinding capacity of the mill.
- Overloading the mill with material can reduce grinding efficiency and increase energy consumption.
- The physical-chemical properties of the feed material (e.g., hardness, moisture content) also affect grinding performance. Adjustments may be needed based on material characteristics.
-
Ensure Timely Removal of Ground Product
- Efficient discharge of ground material prevents overgrinding and ensures consistent product quality.
- Use appropriate discharge mechanisms (e.g., grate discharge, overflow discharge) based on the material and desired fineness.
- Regularly monitor and adjust the discharge system to maintain optimal performance.
-
Maintain Armor Surface Shape
- The shape and condition of the mill's armor (lining) affect grinding efficiency and wear.
- Smooth linings are suitable for fine grinding, while ribbed or wave linings are better for coarse grinding.
- Regularly inspect and replace worn linings to maintain grinding efficiency.
-
Monitor and Control Milling Fineness
- The desired fineness of the ground product influences the grinding parameters.
- For finer particles, longer grinding times and smaller balls are required.
- Use particle size analysis to monitor fineness and adjust parameters as needed.
By systematically addressing these factors, you can significantly increase the production and efficiency of a ball mill. Each parameter should be carefully optimized based on the specific material and operational requirements to achieve the best results.
Summary Table:
Factor | Optimization Tips |
---|---|
Rotation Speed | Maintain 65-75% of critical speed for optimal grinding efficiency. |
Grinding Medium | Use smaller balls for fine grinding, larger balls for coarse grinding. Match ball density to material. |
Filling Ratio | Keep filling ratio at 30-40% to avoid overloading or underfilling. |
L:D Ratio | Optimize drum length to diameter ratio (1.56–1.64) for efficient grinding. |
Feed Rate & Material | Balance feed rate with grinding capacity; adjust for material hardness and moisture. |
Ground Product Removal | Use appropriate discharge mechanisms to prevent overgrinding. |
Armor Surface Shape | Choose smooth linings for fine grinding, ribbed/wave linings for coarse grinding. |
Milling Fineness | Monitor particle size and adjust grinding parameters for desired fineness. |
Ready to optimize your ball mill production? Contact our experts today for tailored solutions!