To measure a ball mill effectively, it is essential to evaluate several key parameters that define its performance and operational efficiency. These include the mill's dimensions (length and diameter), the speed of rotation (critical speed), the filling ratio of grinding media, the type and size of grinding media, and the power consumption. Additionally, the feed and discharge rates, particle size distribution of the ground material, and the mill's overall efficiency in terms of energy consumption and throughput must be considered. Proper measurement ensures optimal operation, maximizes grinding efficiency, and minimizes wear and energy costs.
Key Points Explained:
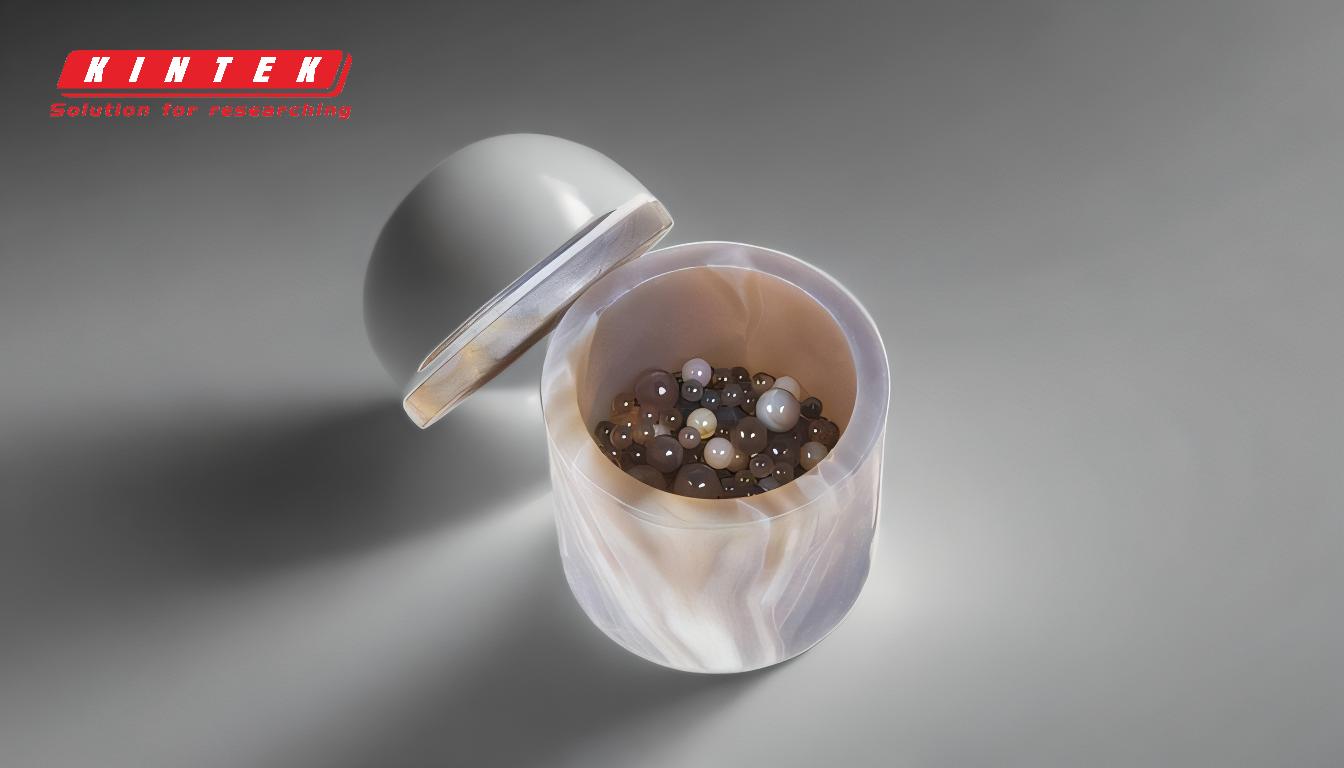
-
Mill Dimensions (Length and Diameter)
- The physical dimensions of a ball mill, specifically its length and diameter, are critical for determining its capacity and grinding efficiency.
- A larger diameter allows for higher impact forces, while a longer mill provides more residence time for grinding.
- These dimensions are typically measured using standard tools like tape measures or laser distance meters.
-
Critical Speed
- The critical speed is the rotational speed at which the grinding media begins to centrifuge, reducing grinding efficiency.
- It is calculated using the formula:
[ N_c = \frac{42.3}{\sqrt{D}} ]
where ( N_c ) is the critical speed in revolutions per minute (RPM) and ( D ) is the mill diameter in meters. - Operating below the critical speed ensures the grinding media cascades and impacts the material effectively.
-
Filling Ratio of Grinding Media
- The filling ratio refers to the percentage of the mill volume occupied by grinding media (balls or rods).
- An optimal filling ratio (typically 30-40% for ball mills) ensures efficient grinding without excessive wear or energy consumption.
- This is measured by calculating the volume of grinding media relative to the total mill volume.
-
Type and Size of Grinding Media
- The size and material of grinding media (e.g., steel balls, ceramic balls) significantly affect grinding efficiency.
- Larger media are suitable for coarse grinding, while smaller media are better for fine grinding.
- The size distribution of the grinding media should be optimized based on the feed material and desired product size.
-
Power Consumption
- Power consumption is a key indicator of the mill's efficiency and is measured using power meters.
- High power consumption may indicate inefficiencies, such as overloading or improper media size.
- Monitoring power consumption helps optimize operational parameters and reduce energy costs.
-
Feed and Discharge Rates
- The feed rate is the amount of material entering the mill, while the discharge rate is the amount exiting.
- These rates are measured using flow meters or weigh feeders to ensure the mill operates within its designed capacity.
- Proper balancing of feed and discharge rates prevents overloading and ensures consistent product quality.
-
Particle Size Distribution
- The particle size distribution of the ground material is a critical measure of grinding efficiency.
- It is typically analyzed using sieves or laser diffraction analyzers.
- A narrow particle size distribution indicates efficient grinding, while a wide distribution may suggest issues with media size or mill operation.
-
Overall Efficiency
- Overall efficiency is evaluated by comparing energy consumption to the amount of material ground.
- This includes assessing throughput (tons per hour) and specific energy consumption (kWh/ton).
- High efficiency ensures cost-effective operation and minimal environmental impact.
-
Wear and Maintenance
- Regular measurement of wear on grinding media and mill liners is essential for maintaining performance.
- Wear is assessed by inspecting media and liners for size reduction or damage.
- Timely replacement of worn components prevents inefficiencies and prolongs mill life.
-
Operational Monitoring and Optimization
- Continuous monitoring of operational parameters (e.g., temperature, vibration, noise) helps identify issues early.
- Data from sensors and control systems can be used to optimize mill performance and reduce downtime.
- Implementing predictive maintenance strategies further enhances reliability and efficiency.
By systematically measuring and analyzing these parameters, operators can ensure the ball mill operates at peak efficiency, delivering consistent product quality while minimizing costs and environmental impact.
Summary Table:
Parameter | Description | Measurement Method |
---|---|---|
Mill Dimensions | Length and diameter determine capacity and grinding efficiency. | Tape measure or laser distance meter. |
Critical Speed | Rotational speed at which grinding media begins to centrifuge. | Calculated using formula: ( N_c = \frac{42.3}{\sqrt{D}} ). |
Filling Ratio | Percentage of mill volume occupied by grinding media (optimal: 30-40%). | Volume calculation of grinding media. |
Grinding Media Type/Size | Size and material affect grinding efficiency (e.g., steel or ceramic balls). | Optimized based on feed material and product. |
Power Consumption | Key indicator of efficiency; high consumption may indicate issues. | Measured using power meters. |
Feed/Discharge Rates | Amount of material entering and exiting the mill. | Flow meters or weigh feeders. |
Particle Size Distribution | Measure of grinding efficiency; analyzed using sieves or laser diffraction. | Sieves or laser diffraction analyzers. |
Overall Efficiency | Energy consumption vs. material ground (throughput and specific energy). | Throughput (tons/hour) and kWh/ton analysis. |
Wear and Maintenance | Regular inspection of grinding media and liners for wear. | Visual inspection and size reduction checks. |
Operational Monitoring | Continuous monitoring of temperature, vibration, and noise for optimization. | Sensors and control systems. |
Optimize your ball mill's performance today—contact our experts for a consultation!