Determining the quality of a metal involves a series of specialized tests that evaluate its physical, mechanical, and chemical properties. These tests include hardness testing, tensile testing, corrosion testing, and others, each designed to measure specific characteristics that define the metal's performance and suitability for various applications. By conducting these tests, manufacturers and engineers can ensure that the metal meets the required standards and specifications, thereby guaranteeing its quality and reliability in real-world use.
Key Points Explained:
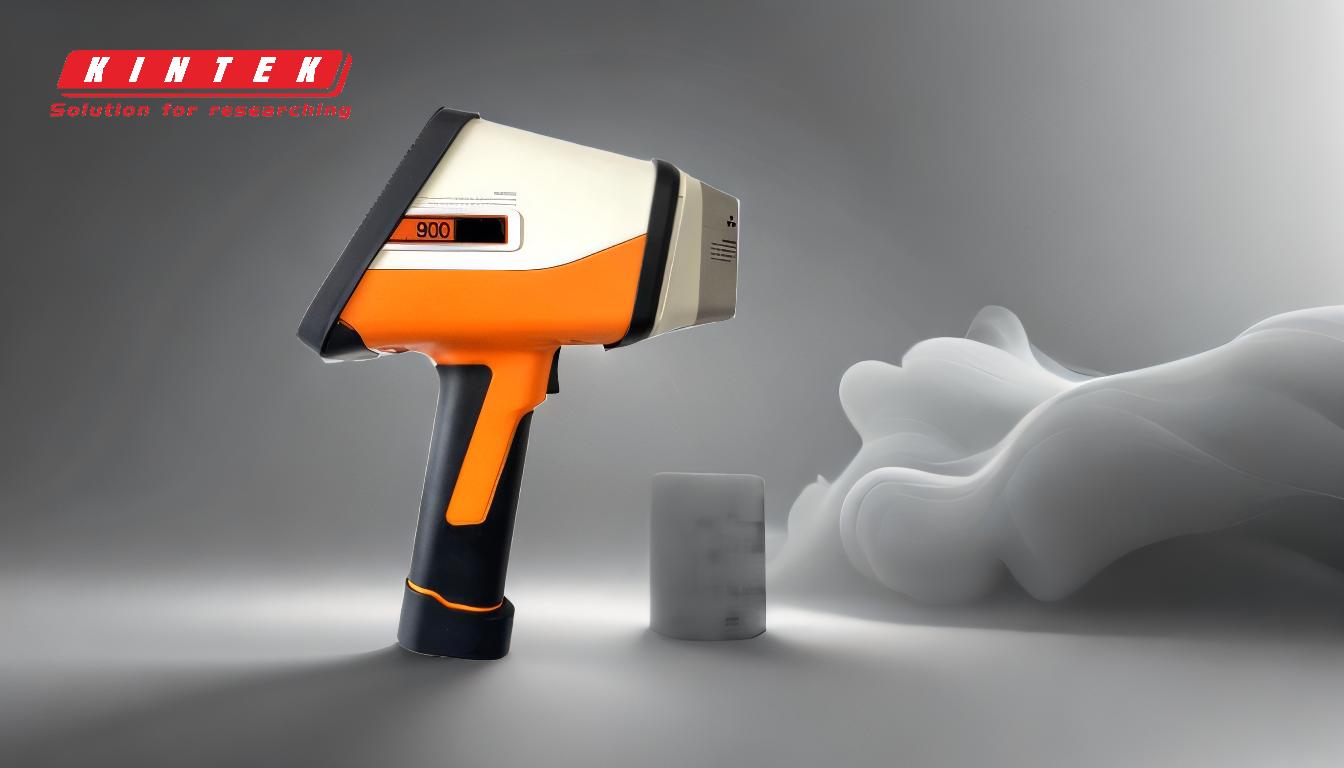
-
Hardness Testing:
- Purpose: Hardness testing measures the resistance of a metal to deformation, indentation, or scratching. This property is crucial for applications where the metal must withstand wear and tear.
- Methods: Common methods include the Brinell, Rockwell, and Vickers hardness tests. Each method uses a different type of indenter and load to measure hardness.
- Applications: Used in industries such as automotive, aerospace, and construction to ensure materials can endure mechanical stress.
-
Tensile Testing:
- Purpose: Tensile testing evaluates the metal's ability to withstand stretching or pulling forces. It determines the metal's tensile strength, yield strength, and elongation.
- Procedure: A sample is subjected to a controlled tension until it fractures. The stress-strain curve obtained provides valuable data on the metal's mechanical properties.
- Applications: Essential for materials used in structural applications, such as bridges, buildings, and machinery, where strength and ductility are critical.
-
Corrosion Testing:
- Purpose: Corrosion testing assesses the metal's resistance to degradation caused by environmental factors like moisture, chemicals, and temperature.
- Methods: Techniques include salt spray testing, immersion testing, and electrochemical methods. These tests simulate harsh conditions to evaluate the metal's durability.
- Applications: Important for metals used in marine environments, chemical processing, and outdoor structures where corrosion resistance is vital.
-
Impact Testing:
- Purpose: Impact testing measures the metal's ability to absorb energy and resist fracture under sudden loading.
- Methods: The Charpy and Izod tests are commonly used, involving a pendulum striking a notched sample to measure the energy absorbed during fracture.
- Applications: Crucial for materials used in impact-prone environments, such as automotive crash components and heavy machinery.
-
Non-Destructive Testing (NDT):
- Purpose: NDT methods evaluate the metal's integrity without causing damage. These tests are essential for quality control and inspection of finished products.
- Methods: Techniques include ultrasonic testing, radiographic testing, magnetic particle testing, and dye penetrant testing.
- Applications: Widely used in industries like aerospace, oil and gas, and manufacturing to detect internal and surface defects.
-
Chemical Composition Analysis:
- Purpose: This analysis determines the elemental composition of the metal, ensuring it meets the required specifications.
- Methods: Techniques include spectroscopy, X-ray fluorescence (XRF), and inductively coupled plasma (ICP) analysis.
- Applications: Essential for verifying the alloy composition in industries like metallurgy, electronics, and aerospace.
-
Microstructural Analysis:
- Purpose: Microstructural analysis examines the metal's internal structure at a microscopic level to assess grain size, phase distribution, and defects.
- Methods: Techniques include optical microscopy, scanning electron microscopy (SEM), and transmission electron microscopy (TEM).
- Applications: Used in research and development, quality control, and failure analysis to understand the metal's properties and performance.
By conducting these comprehensive tests, manufacturers and engineers can ensure that the metal meets the necessary quality standards, providing confidence in its performance and longevity in various applications.
Summary Table:
Test Type | Purpose | Methods | Applications |
---|---|---|---|
Hardness Testing | Measures resistance to deformation, indentation, or scratching. | Brinell, Rockwell, Vickers hardness tests. | Automotive, aerospace, construction. |
Tensile Testing | Evaluates ability to withstand stretching or pulling forces. | Controlled tension until fracture. | Bridges, buildings, machinery. |
Corrosion Testing | Assesses resistance to degradation from moisture, chemicals, or temperature. | Salt spray, immersion, electrochemical methods. | Marine environments, chemical processing, outdoor structures. |
Impact Testing | Measures energy absorption and fracture resistance under sudden loading. | Charpy, Izod tests. | Automotive crash components, heavy machinery. |
Non-Destructive Testing (NDT) | Evaluates integrity without damage. | Ultrasonic, radiographic, magnetic particle, dye penetrant testing. | Aerospace, oil and gas, manufacturing. |
Chemical Composition Analysis | Determines elemental composition. | Spectroscopy, XRF, ICP analysis. | Metallurgy, electronics, aerospace. |
Microstructural Analysis | Examines internal structure at microscopic level. | Optical microscopy, SEM, TEM. | Research, quality control, failure analysis. |
Ensure your metal meets the highest quality standards—contact our experts today for tailored testing solutions!