A ball mill is a cylindrical device used for grinding materials into fine powders by rotating either horizontally or vertically. It operates on the principles of impact and attrition, where grinding media such as steel balls or rods are tossed around inside the cylinder as it rotates. These balls collide with the material, breaking it down into smaller particles. The efficiency of a ball mill depends on achieving a critical speed, which ensures the balls rotate along the inner walls, maximizing the grinding effect. This process is widely used in industries for material refinement and particle size reduction.
Key Points Explained:
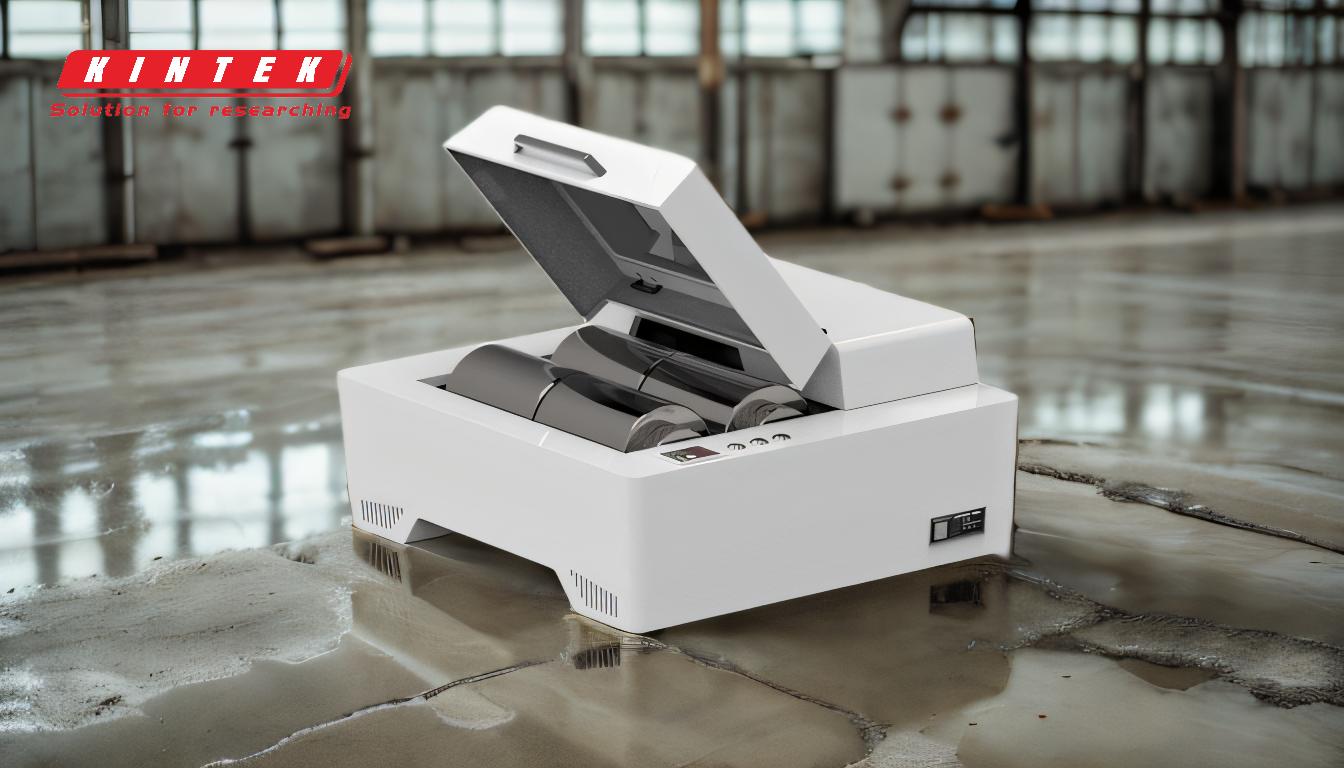
-
Structure and Components of a Ball Mill:
- A ball mill consists of a horizontally or vertically mounted rotating cylinder.
- The cylinder is typically made of durable materials like steel or ceramic to withstand the grinding process.
- Inside the cylinder, grinding media such as steel balls or rods are placed. These media are responsible for breaking down the material.
-
Principles of Operation:
- The ball mill operates on two primary principles: impact and attrition.
- Impact: This occurs when the grinding media (balls or rods) collide with the material, exerting pressure and breaking it into smaller pieces.
- Attrition: This involves the reduction of material size through repeated collisions and friction between the grinding media and the material.
- The rotation of the cylinder causes the grinding media to be tossed around, creating a cascading effect that enhances the grinding process.
- The ball mill operates on two primary principles: impact and attrition.
-
Critical Speed:
- Critical speed is the rotational speed at which the grinding media begins to rotate along the inner walls of the cylinder.
- Achieving critical speed is essential for effective grinding, as it ensures that the grinding media are lifted to a certain height before falling back onto the material, maximizing the impact force.
- If the mill operates below the critical speed, the grinding media will not be lifted high enough, reducing the efficiency of the grinding process.
-
Grinding Media:
- The grinding media used in ball mills are typically made of steel, ceramic, or other durable materials.
- The size and density of the grinding media can vary depending on the material being ground and the desired fineness of the final product.
- The shape of the grinding media (balls or rods) also plays a role in the grinding efficiency, with balls being more commonly used due to their uniform shape and ability to create a cascading effect.
-
Applications of Ball Mills:
- Ball mills are widely used in various industries for grinding materials such as ores, chemicals, and ceramics.
- They are commonly used in the mining industry to grind ores into fine powders for further processing.
- In the chemical industry, ball mills are used to grind raw materials into fine powders for use in manufacturing processes.
- In the ceramics industry, ball mills are used to grind materials into fine powders for use in the production of ceramics and other materials.
-
Advantages of Ball Mills:
- Ball mills are capable of producing very fine powders, making them suitable for applications where a high degree of fineness is required.
- They are versatile and can be used for both wet and dry grinding processes.
- Ball mills are relatively simple to operate and maintain, making them a cost-effective solution for many industries.
-
Limitations of Ball Mills:
- The grinding process in ball mills can be energy-intensive, especially when grinding hard materials.
- The efficiency of the grinding process can be affected by factors such as the size and density of the grinding media, the speed of rotation, and the material being ground.
- Ball mills can generate a significant amount of heat during operation, which may require additional cooling measures in some applications.
In summary, a ball mill is a highly effective and versatile grinding device that operates on the principles of impact and attrition. It is widely used in various industries for grinding materials into fine powders, and its efficiency depends on achieving the critical speed and using the appropriate grinding media. While ball mills have some limitations, their advantages make them a valuable tool in many industrial processes.
Summary Table:
Aspect | Details |
---|---|
Structure | Horizontally or vertically mounted rotating cylinder made of steel/ceramic. |
Principles | Operates on impact and attrition for material breakdown. |
Critical Speed | Essential for maximizing grinding efficiency. |
Grinding Media | Steel or ceramic balls/rods used for grinding. |
Applications | Mining, chemical, and ceramic industries. |
Advantages | Produces fine powders, versatile, and cost-effective. |
Limitations | Energy-intensive, heat generation, and efficiency dependencies. |
Discover how a ball mill can optimize your grinding process—contact our experts today for personalized solutions!