A plasma incinerator, also known as a plasma gasifier, works by using high-voltage electrical arcs to create plasma, which is an ionized gas capable of reaching extremely high temperatures. This plasma is then used to break down waste materials into their basic molecular components, often converting them into syngas (a mixture of hydrogen and carbon monoxide) and a solid residue called slag. The process is highly efficient and environmentally friendly, as it minimizes harmful emissions and can handle a wide variety of waste types, including hazardous materials. Below is a detailed explanation of how a plasma incinerator operates.
Key Points Explained:
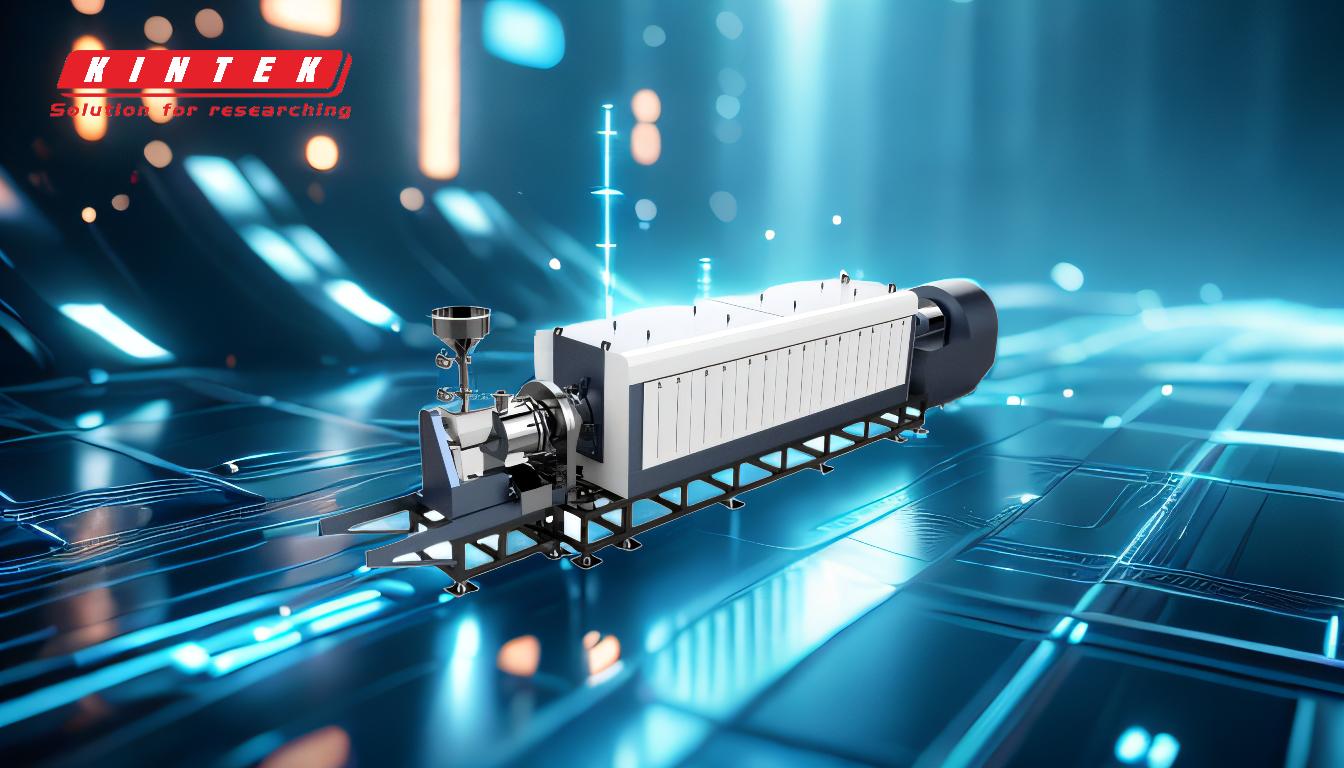
-
Creation of the Plasma Arc:
- High-Voltage Electrical Current: A plasma incinerator uses two electrodes to create an electrical arc. When a high-voltage current is passed between these electrodes, it ionizes the surrounding gas, creating plasma.
- Inert Gas Introduction: Inert gases like argon or nitrogen are often used because they do not react with the waste materials. These gases are pressurized and passed through the electrical arc, further ionizing and heating the gas to create plasma.
-
Waste Material Processing:
- Sealed Container: The plasma arc is directed into a sealed container, known as a plasma converter, where the waste materials are stored.
- Extreme Temperatures: The plasma can reach temperatures between 3,000°C to 7,000°C, which is hot enough to break down almost any material into its basic elements. This process is called pyrolysis.
-
Conversion of Waste:
- Syngas Production: Organic materials in the waste are broken down into syngas, a mixture primarily composed of hydrogen and carbon monoxide. This gas can be captured and used as a fuel or for generating electricity.
- Slag Formation: Inorganic materials, such as metals and minerals, are melted and then cooled to form a glass-like substance called slag. This slag is inert and can be used in construction materials.
-
Environmental and Operational Benefits:
- Reduction of Harmful Emissions: The high temperatures ensure complete combustion of waste, significantly reducing the emission of harmful pollutants.
- Versatility: Plasma incinerators can process a wide range of waste types, including municipal solid waste, medical waste, and hazardous materials.
- Energy Recovery: The syngas produced can be used to generate electricity, making the process energy-efficient.
-
Safety and Control:
- Sealed Environment: The entire process occurs in a sealed environment, preventing the release of any harmful substances into the atmosphere.
- Automated Systems: Modern plasma incinerators are equipped with automated control systems to monitor and adjust the process parameters, ensuring optimal performance and safety.
By understanding these key points, it becomes clear how a plasma incinerator operates to efficiently and safely convert waste materials into useful byproducts, making it a valuable technology in waste management and energy recovery.
Summary Table:
Key Aspect | Details |
---|---|
Plasma Creation | High-voltage electrical arcs ionize inert gases to create plasma. |
Waste Processing | Plasma breaks down waste at 3,000°C to 7,000°C in a sealed container. |
Waste Conversion | Organic waste turns into syngas; inorganic waste forms inert slag. |
Environmental Benefits | Reduces harmful emissions and processes diverse waste types. |
Energy Recovery | Syngas can be used to generate electricity, enhancing energy efficiency. |
Safety Features | Sealed environment and automated systems ensure safety and control. |
Interested in plasma incinerator technology? Contact us today to learn more!