Ion beam sputtering (IBS) is a precise and versatile thin-film deposition technique used to modify the surface properties of substrates. It involves bombarding a target material with high-energy ions in a vacuum environment, causing atoms from the target to be ejected and deposited onto a substrate. This process is widely used in applications such as field electron microscopy, low-energy electron diffraction, and Auger analysis, where a clean surface is essential for accurate results. Additionally, IBS is employed in creating optical elements and cutting thick films without damage. The technique offers advantages such as high film density, controlled stoichiometry, and the ability to coat heat-sensitive materials. Below, the key aspects of how ion beam sputtering works are explained in detail.
Key Points Explained:
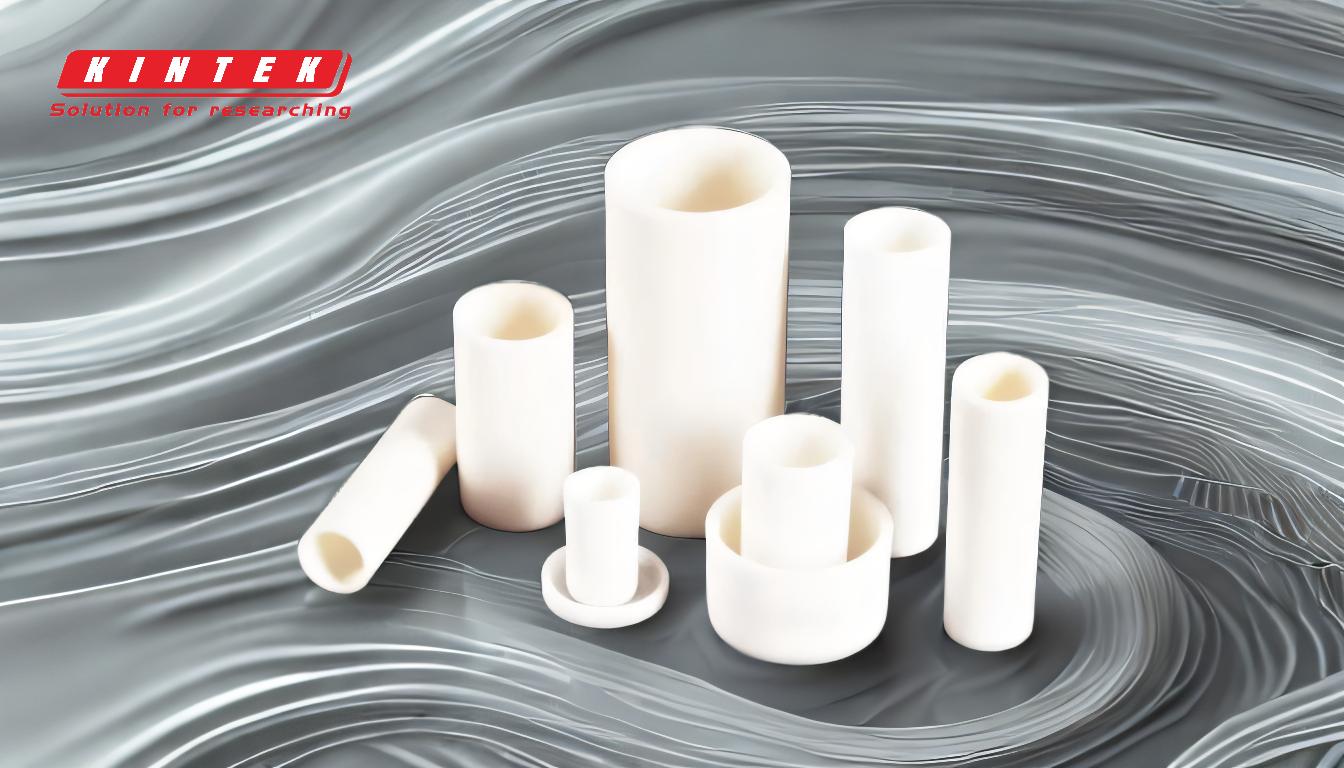
-
Basic Principle of Ion Beam Sputtering:
- Ion beam sputtering involves directing a focused beam of high-energy ions (typically argon or oxygen) at a target material in a vacuum chamber.
- The energy of the ions is sufficient to overcome the surface binding energy of the target atoms, causing them to be ejected from the surface.
- These ejected atoms travel through the vacuum and deposit onto a substrate, forming a thin film.
-
Vacuum Environment:
- The process takes place in a vacuum chamber to prevent interactions between the sputtered particles and air or unwanted gases.
- This ensures the purity and uniformity of the deposited film, as well as the stability of the ion beam.
-
Energy Requirements:
- The energy required to eject target atoms, known as the sputtering threshold energy, depends on the material and is typically a few electron volts (eV).
- The kinetic energy of the sputtered particles is high, which contributes to the formation of dense and well-adhered films.
-
Substrate and Target Configuration:
- The substrate is typically mounted opposite the target material within the vacuum chamber.
- This arrangement allows for uniform deposition of the sputtered atoms onto the substrate.
- Even heat-sensitive substrates, such as plastics, can be coated due to the low temperature of the sputtered particles.
-
Applications in Surface Cleaning and Analysis:
- Ion beam sputtering is used to create clean surfaces for analytical techniques like field electron microscopy, low-energy electron diffraction, and Auger analysis.
- A clean surface is critical for obtaining accurate and reliable results in these applications.
-
Precision Cutting of Thick Films:
- The technique can be used for damage-free cutting of thick films, such as in ion beam slope cutting.
- This is particularly useful for optical elements like dispersive mirrors, glasses, insulators, and lenses, where precision is essential.
-
Film Properties and Stoichiometry:
- Ion beam sputtering can alter the stoichiometry and properties of the deposited film.
- For example, bombarding films with O2+ and Ar+ ions during deposition can increase film density, modify crystal structures, and reduce water permeability.
-
Advantages of Ion Beam Sputtering:
- High precision and control over film thickness and composition.
- Ability to deposit films on heat-sensitive substrates.
- Creation of dense, high-quality films with excellent adhesion.
- Versatility in applications, from optical coatings to surface analysis.
By understanding these key points, one can appreciate the technical sophistication and wide-ranging utility of ion beam sputtering in both research and industrial applications.
Summary Table:
Key Aspect | Description |
---|---|
Basic Principle | High-energy ions bombard a target, ejecting atoms that deposit onto a substrate. |
Vacuum Environment | Ensures purity, uniformity, and stability of the deposited film. |
Energy Requirements | Sputtering threshold energy depends on the material (typically a few eV). |
Substrate & Target Setup | Substrate is mounted opposite the target for uniform deposition. |
Applications | Surface cleaning, optical elements, and precision cutting of thick films. |
Film Properties | Alters stoichiometry, increases density, and modifies crystal structures. |
Advantages | High precision, heat-sensitive substrate compatibility, and dense film quality. |
Discover how ion beam sputtering can enhance your projects—contact our experts today!